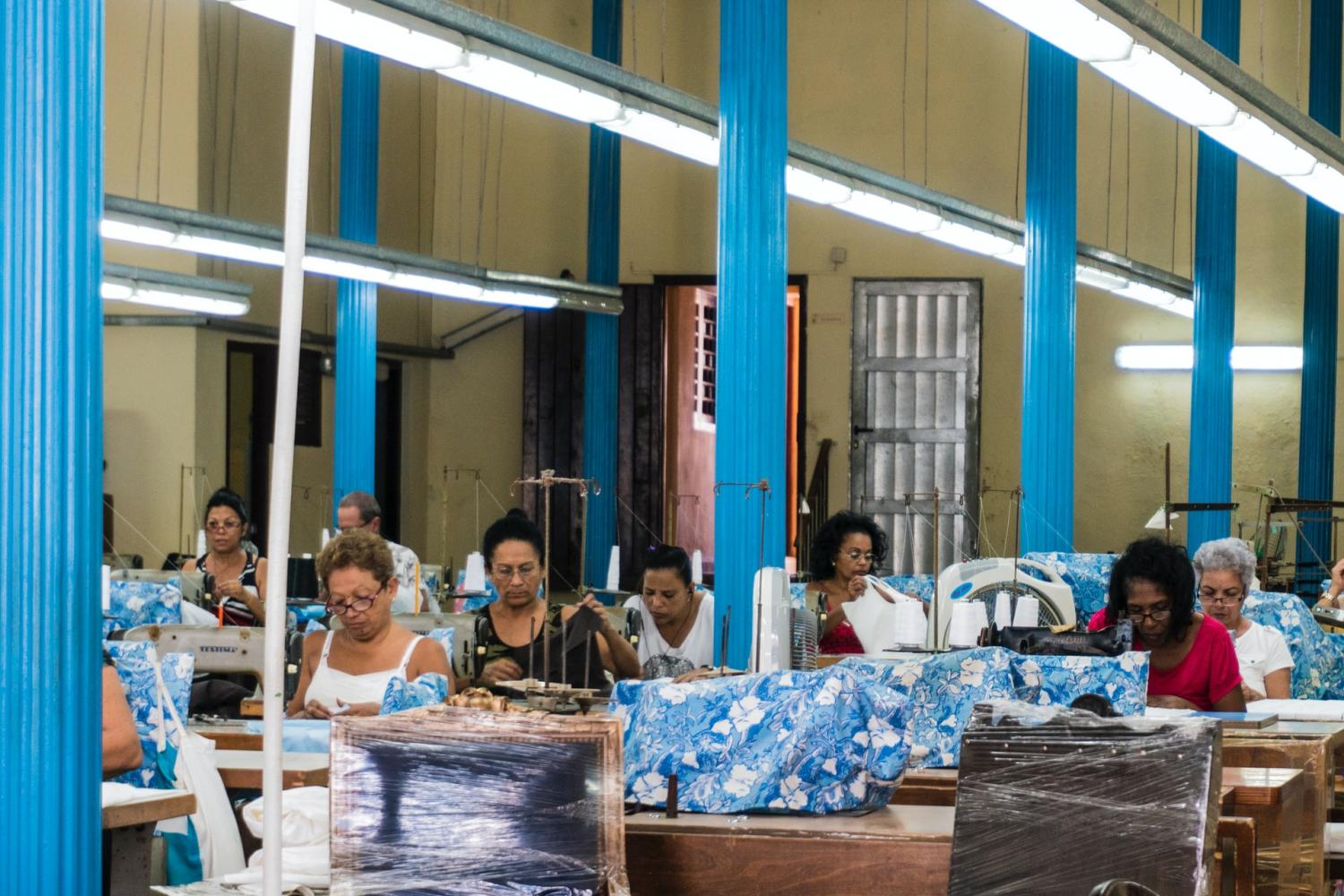
One unexpected consequence of the COVID-19 pandemic starting to come to light is a setback in a long-standing progression toward ethical working conditions in factories. While the immediate economic impacts of our reactions to a global pandemic are fairly predictable, most of us didn’t expect (or didn’t have the time to consider) how one virus’ disruption of a globalized economy could set back years of progress in ethical working conditions.
More data, but also more non-compliance
Since the pandemic started in 2020, the number of factories failing inspections for ethical practices has gone up considerably. Supplier audit data from the international inspection company QIMA, shows a clear trend from 2020 to 2021. The number of “critically non-compliant” factories increased from 18 percent in 2020 to 28 percent in 2021. This bucks a three-year growth in progress where more and more factories were moving out of the “critical” category and into the “compliant” category.
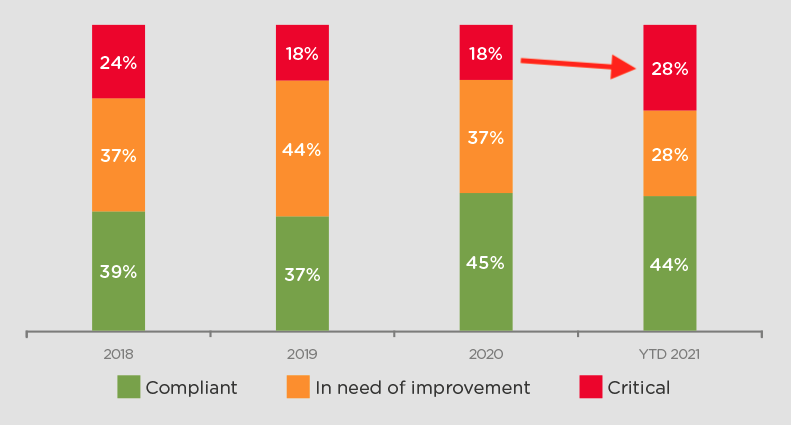
(Image: QIMA.com Q4 Supply Chain Industry Report)
These are factors most of us consider fundamental rights, which organizations ranging from small local groups to international organizations like the United Nations have been working on for decades. Since the industrial revolution factory working conditions have slowly evolved to be better in most dimensions of ethics. The most recent reports, however, show that the ongoing pandemic has been a setback.
How the pandemic affected ethical working conditions
As was expected, the in-and-out of lockdowns across the world starting in the Spring of 2020 changed the demand for goods and services around the world. While the demand for PPE like masks and gloves soared, demand for most other products declined.
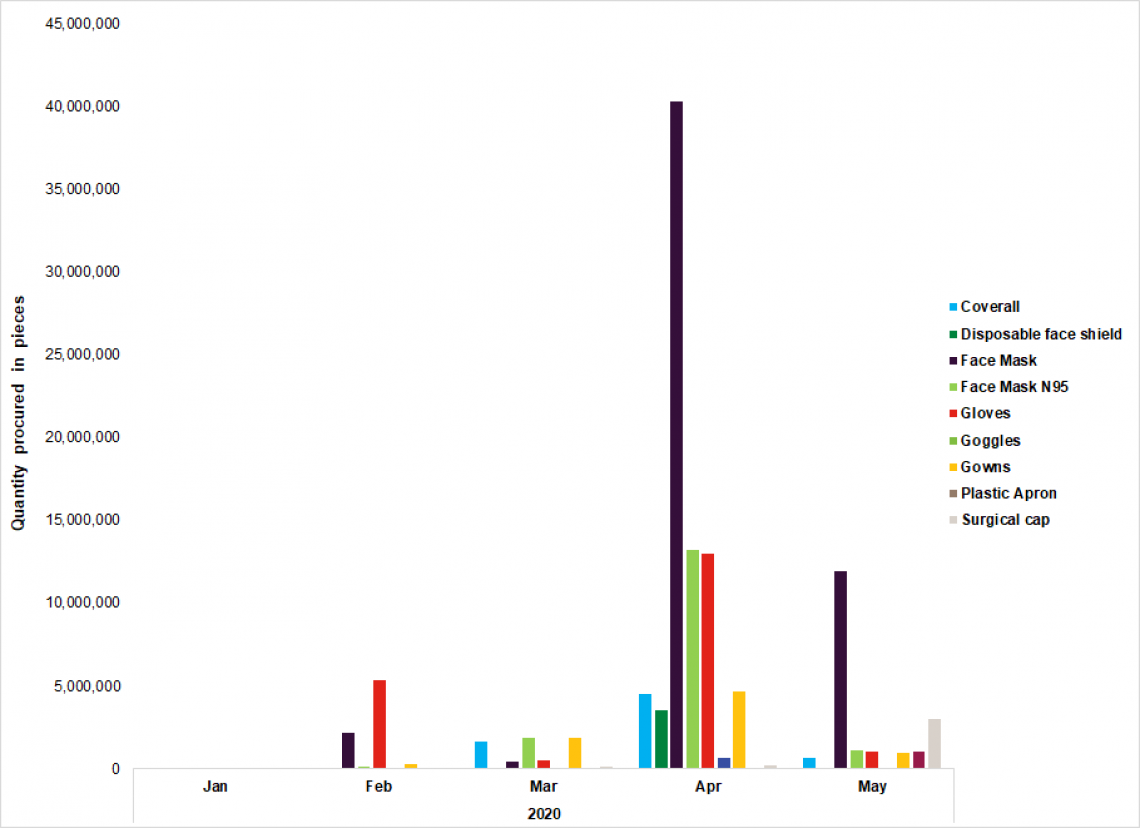
While most of us in western cities are worried about the distractions of working from home or not being able to meet up with friends, we’re now starting to realize that some of the biggest economic burdens are falling on overseas suppliers. These manufacturers tasked with producing the majority of our commodities not only saw a reduction in orders, but in some cases cancelling and nonpayment of those already in production. According to an October 2020 report from Penn State’s Center for Global Workers’ Rights, over half of the suppliers they contacted were forced to accept prices for orders below the cost of production and wait longer than usual for payments.
Furthermore, 77 percent of suppliers surveyed reported that when the pandemic disruptions first hit, they had at least some of their orders cancelled and did not receive payment.
Suppliers' struggles falls on the backs of workers
In our globalized economy the burden of unexpected events flows downstream and often lands hardest on the lowest rung of the ladder: individual workers. Fear, uncertainty, and doubt in developed countries, paired with business closures reduces consumption of goods. To compensate, brands cut down on orders as they scramble to reduce costs wherever possible. As suppliers are not paid, underpaid, or have payments delayed, they too scramble to meet operational costs and as a result, retract to unethical practices.
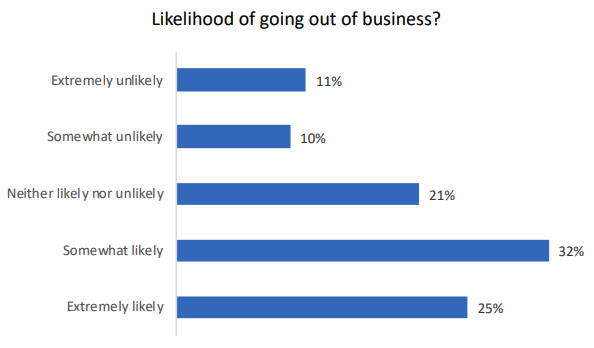
While the long-term implications of this trend are yet to be seen, it is clear that a substantial portion of suppliers are feeling the stress. Like many other changes brought by COVID-19, we hope this will be an asterisk on our timeline of progress, not a substantial setback.
Image credit: Allan Wadsworth via Unsplash
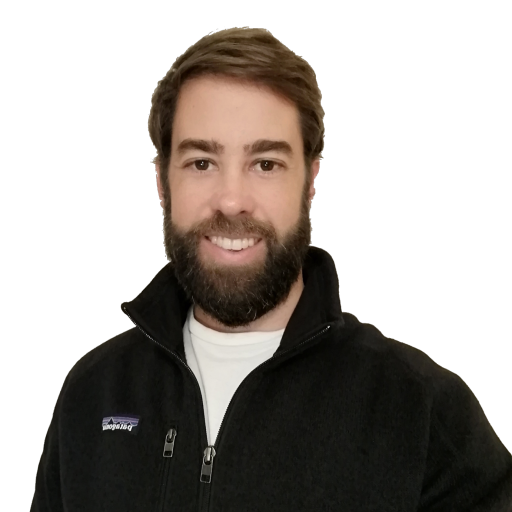
David Evans writes to share uncommon insights with people who want to understand their world a little bit better. His main focus is on our relationship with the natural environment, but he also explores other interests like how tech is reshaping our future and how the human experience is changing.