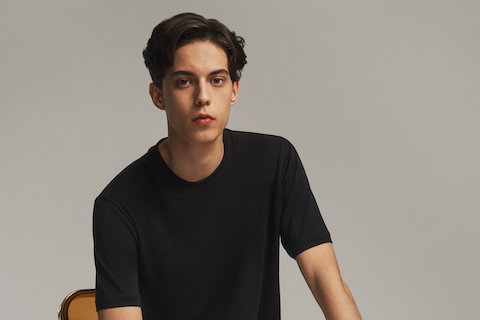
Among its many environmental impacts, it’s estimated that the fashion industry consumes about 10 percent of water used by industry worldwide. While some companies are tackling the adverse impacts of the global fashion industry with the type of raw materials they use, and others look to revamp one or more stages of the textile manufacturing process, Seattle-based Evrnu says it is creating systemic change. The company has recently launched what it claims to be the world’s first high-performance recyclable lyocell material made from 100 percent textile waste.
Evrnu’s mission dates back to when its co-founder, Stacy Flynn, spent a month in China, where she noticed the effects of toxic wastewater from textile factories on local communities. Founded by Flynn and Christopher Stanev, both former employees of big-name textile companies, Evrnu aims to address textile waste and pollution as a whole. With its textile engineering system, NuCycl, the company says it can generate its NuCycl r-lyocell fabric using only cotton textile waste as its base material.
The company's manufacturing process begins with the sorting of textile waste, then shreds it and in the end, purifies it. The recycled textile pulp is then transformed into a highly durable ‘r-lyocell’ fiber through a closed-loop method. The final fiber, says Evrnu, is one of superior durability, and can replace and even outperform virgin cellulosic and plastic-based fabrics, which account for 90 percent of all current textile fibers.
Evrnu recently debuted this material with a T-shirt designed by Carlos Campos; in the past, the company has worked with brands such as Levi Strauss that explored using waste materials to manufacture apparel.
How Evrnu disrupts the textile manufacturing process
Evrnu’s lyocell product is regenerative as it is made entirely from cotton textile waste.
For decades, man-made cellulosic fibers have been generated from dissolved pulp, often from virgin wood. Evrnu’s technology uses recycled textile pulp in the place of virgin tree pulp and processes it into lyocell. In contrast to synthetic fibers including nylon and rayon, which have a chemical makeup entirely different from wood-based cellulose, Evrnu’s lyocell product can be recycled multiple times as its structure has not been altered. That is in contrast to synthetic fibers such as rayon and nylon, which cannot be recycled due to the fabrics’ chemical structure. In industry speak, the process Evrnu uses is a non-derivative method, while conventional materials like rayon and nylon rely on a derivative chemical process.
The result is a bio-based alternative to polyester, nylon and other man-made cellulosic fibers. The resulting fabric also provides the apparel industry a means of reducing carbon emissions and plastic shedding. Evrnu adds that its lyocell material exceeds the performance of the polyester and man-made cellulosic fibers currently available.
Rethinking how fabrics are made
Evrnu sees discarded textiles as an untapped natural resource. The company designed its NuCycl technology with the goal of growing the global textile industry, and doing so sustainably and responsibly, by accessing the full potential of resources that already exist and do not need to be extracted. As estimates suggest that the world’s fashion industry generates about 92 million metric tons of waste annually, Evrnu says it is helping to reduce this global problem by turning what was once simply something to look at and then discard as waste into a renewable resource.
By diverting that textile waste from landfills, Evrnu’s process also prevents the leaching of chemicals and microfibers into the environment. The company’s system not only reduces the amount of energy and chemicals required during the dyeing process, but it is also highly water-efficient — in fact, it uses 98 percent less water than what is needed to manufacture fabric out of cotton, an Evrnu representative explained in an email exchange with TriplePundit.
Pushing the apparel sector into the circular economy
Evrnu’s current plans are to become a player in the global apparel sector’s value chain. Its current plan is to license out the company’s technology with the goal to ramp up the adoption of its fabric and to allow the NuCycl manufacturing process to scale up. To date, the company says it has raised $29 million, with the number expected to increase to $31 million by the end of this month. As part of its long-term strategy, the company is currently building a commercial demonstration factory in the U.S. so it can demonstrate to potential licensees what its technology can make possible. Once completed, the facility will have the capacity to process 17,000 metric tons of pulp and 2,000 tons of fiber.
The result of Evrnu’s efforts is a step forward for the circular economy and a bolder effort to divert textile waste from landfills and prevent more chemicals and contaminated water from leaching into the environment. The company joins other brands in their efforts to rethinking how clothing is both purchased and discarded, including Worn Again Technologies, For Days and Everywhere Apparel.
Image credits via Evrnu
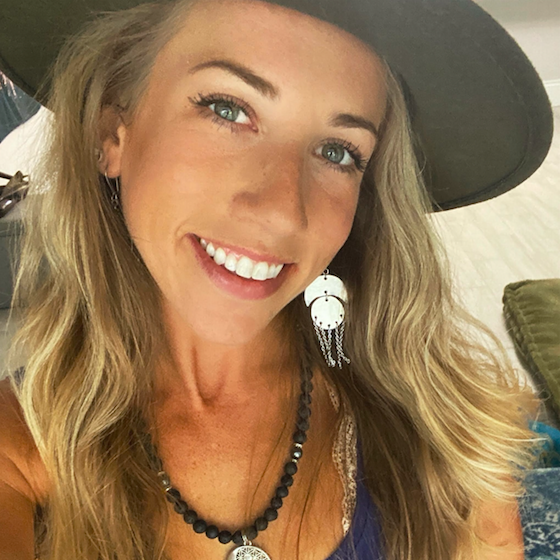
Shelby Gorstein is a writer, yoga teacher, and jeweler based in Delray Beach, Florida. Passionate about health, wellness, and sustainability, Shelby covers topics like plant-based living, renewable energy, food waste and nature.