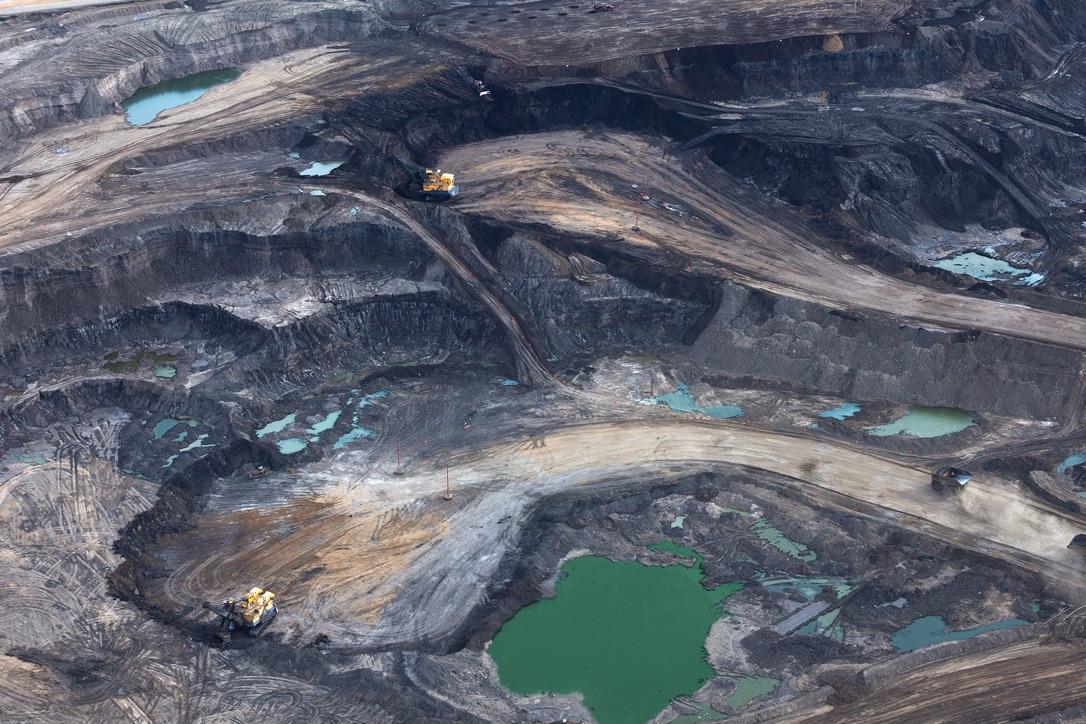
It seems safe to say the future of the automobile is electric. Though today the internal combustion engine still dominates, more and more automakers are pledging all-electric vehicle line-ups in the near future. Each year, consumers have a growing choice of electric vehicles (EVs) to suit their needs, and as gas prices soar, the case to go electric only grows. As both supply and demand for EVs increases, so too will demand for the batteries comprised of lithium that power them.
And with the growth in demand for batteries, so too will come growth in demand for lithium itself. By 2025, around 75 percent of all lithium produced is expected to be used in vehicle batteries. And by 2030, global demand for this element is projected to exceed two million metric tons, a figure that represents a doubling of the demand projected for 2025.
Lithium, a soft silvery-white metal, is not a particularly scarce resource since it’s found quite broadly deposited around the world. But where lithium is found, it’s bound up with salts and minerals, and often not highly concentrated, so extracting it in its pure form requires a lot of processing.
South American countries, notably Bolivia, Chile and Argentina, have some of the worlds’ largest deposits while on other continents, China and Australia are also rich in this resource. In fact, in 2021, Australia was the world's biggest producer at 55,000 metric tons with Chile and China ranking second and third.
Despite the fact the United States has large reserves of lithium, so far it has not been tapped extensively in the country. But this could change going forward and better extraction technologies are likely to help increase both production and extraction efficiency while limiting the environmental footprint of getting at domestic lithium.
TriplePundit recently spoke to John Peichel, global market developer, at Suez - Water Technologies & Solutions, about the traditional methods of extraction common in South America, and how the innovations that Suez is developing can optimize production efficiencies going forward.
Unlike in Australia, where lithium is extracted from hard rock, the element extracted in South America is derived from brines found in salt deserts prevalent there, known as salars. The brine is brought up from underground sources into large above ground basins, where the process of extraction begins.
Lithium is dissolved in these brines, but is very weakly concentrated. However, as water is evaporated off under the sun in these basins, the element becomes increasingly concentrated. When lithium concentration increases to around 6 percent in the brine solution, it is cost effective to transport the brine off the salar for final treatment in processing plants in order to extract the lithium and process into a form that can be sold for battery production.
Mineral salts like potassium chloride used in fertilizer are also extracted from these brines, and in fact, historically, lithium was a by-product of fertilizer production - but extracting the element from brine in this traditional way has some significant drawbacks.
Foremost, it is very land-intensive to use evaporation ponds, and the process is damaging to the local environment since it involves heavy earth moving equipment and demands inputs of added chemicals. The photo shown above gives a sense of the scale of an operation and the consequent land degradation associated with the process.
Importantly, too, as a way to capture lithium, the use of evaporation ponds is quite inefficient. This process alone takes 18 to 24 months, so it’s very time consuming. Furthermore, there are significant resource losses, with a little more than 50 percent of the lithium originally dissolved in the brine remaining unrecovered in the process. What this means is, as this commodity becomes more valuable, a loss of yield to this degree becomes increasingly problematic.
To address the environmental problems while yielding higher amounts of lithium from brine, newer direct lithium extraction (DLE) processes, which Suez is developing in its partnership with other producers, are likely to become increasingly important.
To begin with, instead of using evaporation ponds, DLE can be done in on-site processing plants where subterranean brine is pumped up and passed directly through what is known as an extraction media. Lithium binds to the media, while allowing all the other brine salts to pass through. Thousands upon thousands of gallons of brine at a time can be passed through the media, where the element begins to accumulate in a concentrated form. Periodically, the extraction media is removed, and clean water is introduced to dissolve the lithium from it. Finally, by a process of reverse osmosis, concentrated lithium is extracted from the freshwater solution, which is then processed into its salable form.
There are many benefits to DLE. Firstly, it avoids the problem of using large swaths of land which evaporation ponds require, meaning it leaves a comparatively minuscule footprint. Secondly, production time for extracting this resource is reduced to a matter of days, as opposed to close to two years by evaporation methods. And thirdly, the yield from brine is significantly increased; DLE captures 90-plus percent of the lithium from brine compared with only about 45 percent using evaporation techniques.
Peichel of Suez added that with the company’s approach to DLE, one of the key environmental concerns with the process would be mitigated. In order to dissolve lithium from the extraction media, fresh water must be used, which is scarce in desert environments. Indeed, one feature which evaporation ponds do avoid is the use of freshwater. However, Suez’s process involves recycling the freshwater used in a closed loop system, allowing water to be used for dissolving lithium from the media repeatedly.
DLE could be suitable wherever lithium is extracted from brine, and it may also help unlock its production in the U.S. Peichel explained that in environments within the U.S., it’s not just a matter of old techniques of extracting lithium competing with newer ones, but that in some places, conditions do not support evaporation ponds. In such cases, DLE potentially opens up opportunities for such production that would not otherwise exist. Also, where existing lithium mining from brine is currently active (e.g. the Silver Peak Lithium Mine in Nevada), Peichel pointed out that further expansion is challenging due to environmental concerns over evaporation ponds, making DLE a potentially attractive alternative in recovering additional lithium without expanding the operational footprint.
Of course, no resource extraction method is flawless. DLE, since it uses reverse osmosis, requires energy inputs. But the process itself would not exclude renewable energy playing a part in the future, and in any case, there are always trade-offs. DLE avoids the energy used in building and maintaining traditional evaporation ponds, transporting brine offsite for processing, and bringing in the required chemical inputs.
As Peichel explained to 3p, “DLE is definitely in the early stages of commercialization from a number of different companies and approaches.” so just what the future holds for the technology is still an unfolding story. Nevertheless, what DLE would offer is a much more efficient means of recovering lithium, a smaller environmental footprint, and as demand for lithium increases, the technology could be poised to play an important part in meeting it.
Image credit via Suez Water Technologies & Solutions
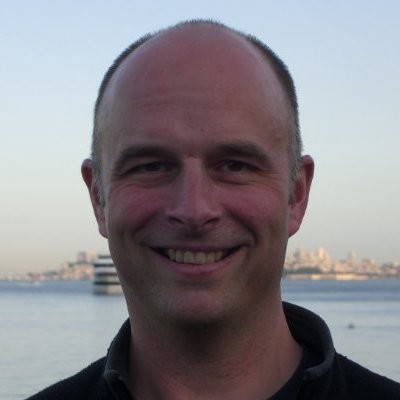
Phil Covington holds an MBA in Sustainable Management from Presidio Graduate School. In the past, he spent 16 years in the freight transportation and logistics industry. Today, Phil's writing focuses on transportation, forestry, technology and matters of sustainability in business.