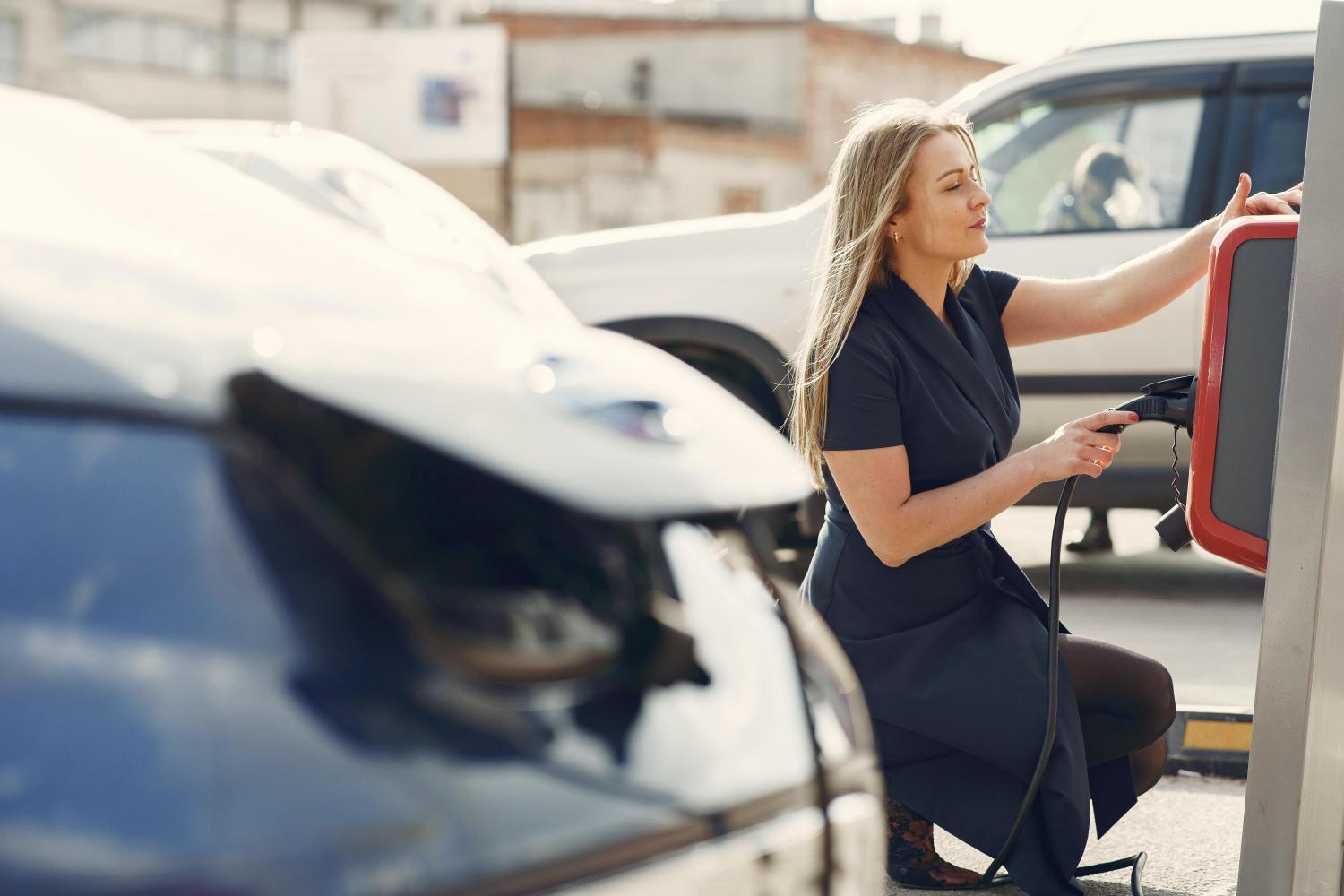
The global lithium-ion battery market is expected to grow by a factor of five to 10 in the next decade. Reaching aggressive targets for electric vehicles (EVs) and battery-based energy storage system production relies on materials such as lithium and rare earth metals. However, material shortages could stall the manufacturing of some clean energy technologies, which is concerning from a climate perspective.
Energy storage capacity is critical for the clean energy transition away from fossil fuels as renewables are an intermittent power source. For example, energy storage systems at utility-scale wind farms and solar plants enable these facilities to deliver power when demand is high but renewable energy supply is low. Likewise, batteries for EVs are critical for phasing out the use of the internal combustion engine.
Can the supply chain keep up with the soaring demand for EVs and battery storage systems? What needs to happen to prepare for a surge in lithium-ion battery production?
Lithium supply chain issues could stall adoption of EVs
Lithium is a critical material in manufacturing the batteries used in EVs and energy storage systems. However, from September 2021 to March 2022, the price of the element increased by more than 400 percent, though it has recently leveled off. Nevertheless, skyrocketing material costs will result in higher prices for consumers.
Joe Lowry of Global Lithium doesn’t expect future lithium supplies to keep up with demand. “In the next two years, even though there will be significant growth in supply, it will be less than demand, so the gap will just continue to grow,” he explained in a recent interview with Bloomberg.
For example, the lack of advancement in lithium extraction and additional investment in the industry’s supply chain could stall EV adoption. Yet, lithium supplies are not the only value chain shortage wreaking havoc on the EV industry. The ongoing semiconductor shortage has caused automakers to close factories temporarily, and EVs commonly need twice as many of them per vehicle compared to models with traditional internal combustion engines.
Although this situation has been exacerbated by factory closures and shipping bottlenecks created by the COVID-19 pandemic, it could be a cautionary tale about how supply chain shortages can slow EV manufacturing while boosting expenses.
Establishing a secure supply for lithium-ion batteries
Batteries are expected to account for 95 percent of global lithium demand by 2030, and forward-looking organizations are examining how to establish a secure supply to promote the deployment of clean energy. For example, the current U.S. Secretary of Energy, Jennifer Granholm, is calling for a secure, domestic supply of lithium and developing a domestic manufacturing base for EV batteries and stationary grid storage.
Li-Bridge is a public-private collaboration dedicated to accelerating the development of a robust and secure domestic supply chain for lithium batteries. Argonne National Laboratory coordinates Li-Bridge and brings together key stakeholders to make the United States competitive in the global battery supply chain.
The U.S. Department of Energy’s national blueprint also calls for materials recycling and promoting the growth of domestic materials processing. Collaboration among a variety of stakeholders is critical in keeping up with demand.
Increasing the capacity of batteries with fewer materials
One potential way to mitigate supply chain shortage issues is by increasing the capacity of batteries without proportionately increasing the quantity of materials. Michelle Tokarz, a Ph.D. and Vice President of Partnerships and Innovation at The Coretec Group, is examining how to apply innovation, bridging the gap between scientific innovation and business needs.
The Coretec Group is developing silicon anodes for lithium-ion storage batteries that will enable them to charge faster, last longer, and need fewer materials to manufacture. Tokarz explained in an interview with TriplePundit that this approach involves replacing graphite on the anodes of batteries with silicon, which can increase their energy density. “We are examining if we can get more out of our materials, so we don’t need to use as much lithium,” says Tokarz.
But materials don’t always respond in apparently predictable ways, so it’s critical to test and evaluate a variety of ideas. Such innovation is critical for boosting the performance of lithium-ion batteries.
Ushering in the clean energy economy requires establishing reliable supply chains for necessary materials. Not adequately preparing for a surge in demand could hinder efforts to dramatically reduce greenhouse gas emissions. Ensuring secure supplies of lithium and other critical materials while also promoting design innovation can mitigate future supply chain issues for lithium-ion batteries.
Image credit: Gustavo Fring via Pexels
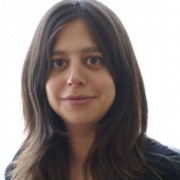
Sarah Lozanova is an environmental journalist and copywriter and has worked as a consultant to help large corporations become more sustainable. She is the author of Humane Home: Easy Steps for Sustainable & Green Living, and her renewable energy experience includes residential and commercial solar energy installations. She teaches green business classes to graduate students at Unity College and holds an MBA in sustainable management from the Presidio Graduate School.