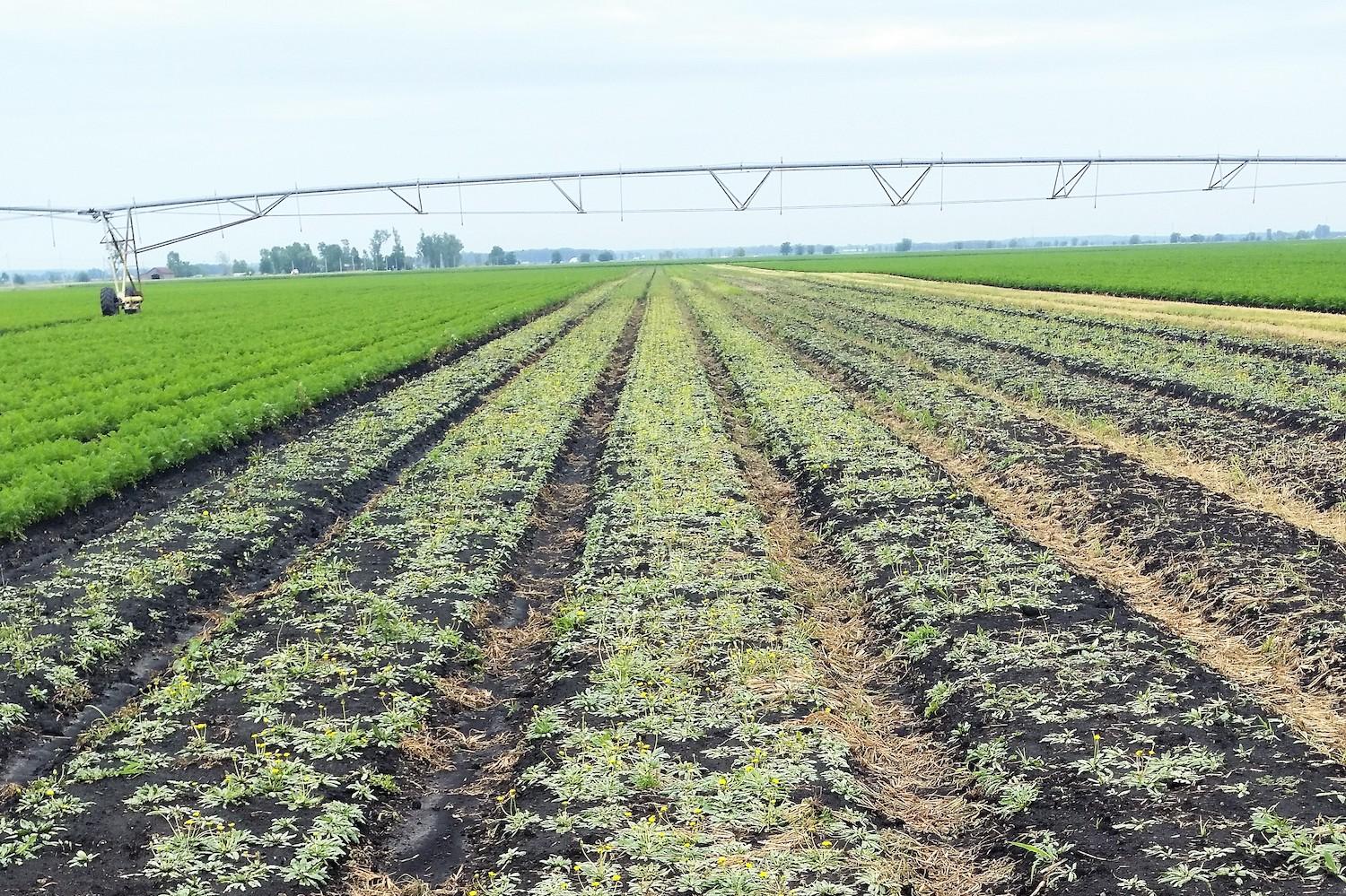
In partnership with the U.S. Air Force Research Laboratory and tire company Goodyear, Ohio-based startup Farmed Materials is cultivating a particular species of dandelion that can replace natural rubber in tires.
The bioeconomy of the future is beginning to take shape, and it is emerging in many different directions. Replacing petrochemicals with plant-based material is still a leading concern. Researchers are also taking advantage of new tools and methodologies to deploy a wider range of renewable materials, and to use those materials in ways that create new efficiencies. Here are five to follow in 2023.
1. The look of linen, from squid
Squitex is a delicate looking, ivory colored fiber that can be spun into a twine-like yarn. However, it is not made from hemp, linen, cotton, jute or any other plant. Squitex is made from squid or, more precisely, from the proteins found in the circular “teeth” embedded in the suction cups of a squid’s tentacles.
Squid may seem like an odd place to look for inspiration in the bioeconomy, but their teeth have evolved over 350 million years to arrive at a state of highly durable, flexible and self-healing functionality, all of which are highly desirable traits in fabrics and other coverings.
Squitex was created in the laboratory of Penn State professor Melik Demirel, who specializes in leveraging biomimicry to develop sustainable materials. His team cultivated large samples of squid protein by piggybacking it onto E. coli bacteria.
As described by Penn State, Squitex fiber is strong enough to lift 3,000 times its own weight. It is biodegradable, and it can also be recycled if augmented with acrylic or cellulose.
Squitex was one of five materials to win the top prize in the 2021 Microfiber Innovation Challenge, hosted by the startup incubator Conservation X Labs.
2. The feel of leather, from plants
Petrochemicals have long been the go-to source for formulating synthetic suede and other alternatives to natural leather. Producing a high-quality leather alternative from non-petroleum resources within the bioeconomy has been a far greater challenge, but scientists from the company Modern Meadow have cracked the code. Their “Bio-Alloy” process incorporates proteins with natural plant-based polymers.
Earlier this year, Modern Meadow introduced Bio-Tex, the first material produced with Bio-Alloy technology. In partnership with Modern Meadow, the Italian firm Limonta is using Bio-Tex to produce BioFabbrica, described as a “vegan plant-based material family" that is "lightweight and delivers superior color vibrance and performance while reducing GHG emissions by over 90 percent compared to traditional, chrome-tanned leather.”
The partners say they are also working to incorporate more recycled and waste bio-materials into the process.
3. Sustainable tires, from dandelions
Electric vehicles are an important feature of the global energy transition, but they still contribute to the tire waste stream. That includes microplastic pollution from wear and tear on the streets, in addition to whole tires.
Automotive stakeholders have been searching for solutions. One seemingly obvious choice would be to use more natural rubber. However, that pathway is not available, at least not in terms of the current supply chain.
The rubber tree, Hevea brasiliensis, is the only supplier of natural rubber to the global economy. The entire species is now under threat from climate change and other issues, including a destructive blight. Demand for natural rubber is anticipated to outstrip supply in less than 10 years unless alternative sources emerge.
Dandelions could be it. Dandelion rubber already has a history dating back to the 1940s when researchers scouted for new sources after World War II disrupted supply chains.
More recently, the U.S. Air Force Research Laboratory has been working on a modern version with Goodyear for application to aircraft tires. Earlier this year, the lab upped the ante with a multi-year R&D commitment that pairs Goodyear with the Ohio company Farmed Materials, which is raising the dandelion species Kok-saghyz, or TK for short.
The roots of TK yield a natural rubber when crushed. The processing will be undertaken through the BioMADE program, a public-private bioeconomy partnership supported by the U.S. Department of Defense. Goodyear will incorporate the rubber into tires that meet Air Force specification. If the new tires meet performance expectations, Goodyear foresees applications throughout its product line.
4. Renewable “steel,” from trees
The global steel industry has been leaning on green hydrogen, electrification and recycling to decarbonize. A different kind of solution has emerged in the form of high-strength alternative materials. One example is MettleWood, a cellulose-based material described as “60 percent stronger than construction-grade steel but 80 percent lighter, much less expensive and far more sustainable.”
MettleWood was created in the laboratory of the startup InventWood. The company is a University of Maryland spinoff founded by Liangbing Hu, who is the Herbert Rabin distinguished professor in the school’s Department of Materials Science and Engineering and director of its Center for Materials Innovation.
MettleWood can be made from many different trees. The common denominator is a new process that removes the lignin “glue” that normally binds tree cells. The remaining wood can be compressed to a higher degree, resulting in an extremely dense but lightweight material.
The U.S. Department of Energy recently awarded InventWood with $20 million in funding to scale up MettleWood for widespread use. The InventWood research team has calculated that replacing steel structural beams, columns and connections with MettleWood would reduce greenhouse gas emissions in the construction industry by 37.2 gigatons in 30 years, which is roughly equivalent to the entirety of emissions from human activity for a year.
5. Recovering cobalt, with ostrich bones
For all the recent advances in materials science and the bioeconomy, researchers have barely begun to scratch the potential for bio-based alternatives to outperform their synthetic counterparts. New research from a team of scientists in the U.S. and Iran provides a glimpse into the possibilities.
The team modified ostrich bone waste with hydrogen peroxide to create a highly efficient process for recovering cobalt and other valuable substances from industrial wastewater.
The particular focus of attention is wastewater containing dyes, including cobalt-base dyes, produced by various leading industries including textiles, leather, paper, food, agriculture and pharmaceuticals, among others.
Among other uses, cobalt is a key material for manufacturing electric vehicles and for producing solar and wind energy. Manufacturers currently rely on a cobalt supply chain that is vulnerable to conflict issues and human rights violations. Wastewater recovery through the bioeconomy could provide an alternative route, while also helping to increase the supply of cobalt as demand rises.
Image courtesy of Goodyear
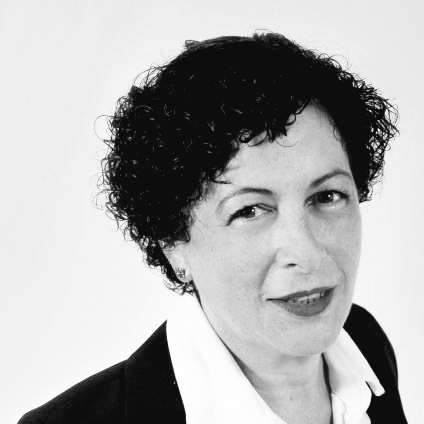
Tina writes frequently for TriplePundit and other websites, with a focus on military, government and corporate sustainability, clean tech research and emerging energy technologies. She is a former Deputy Director of Public Affairs of the New York City Department of Environmental Protection, and author of books and articles on recycling and other conservation themes.