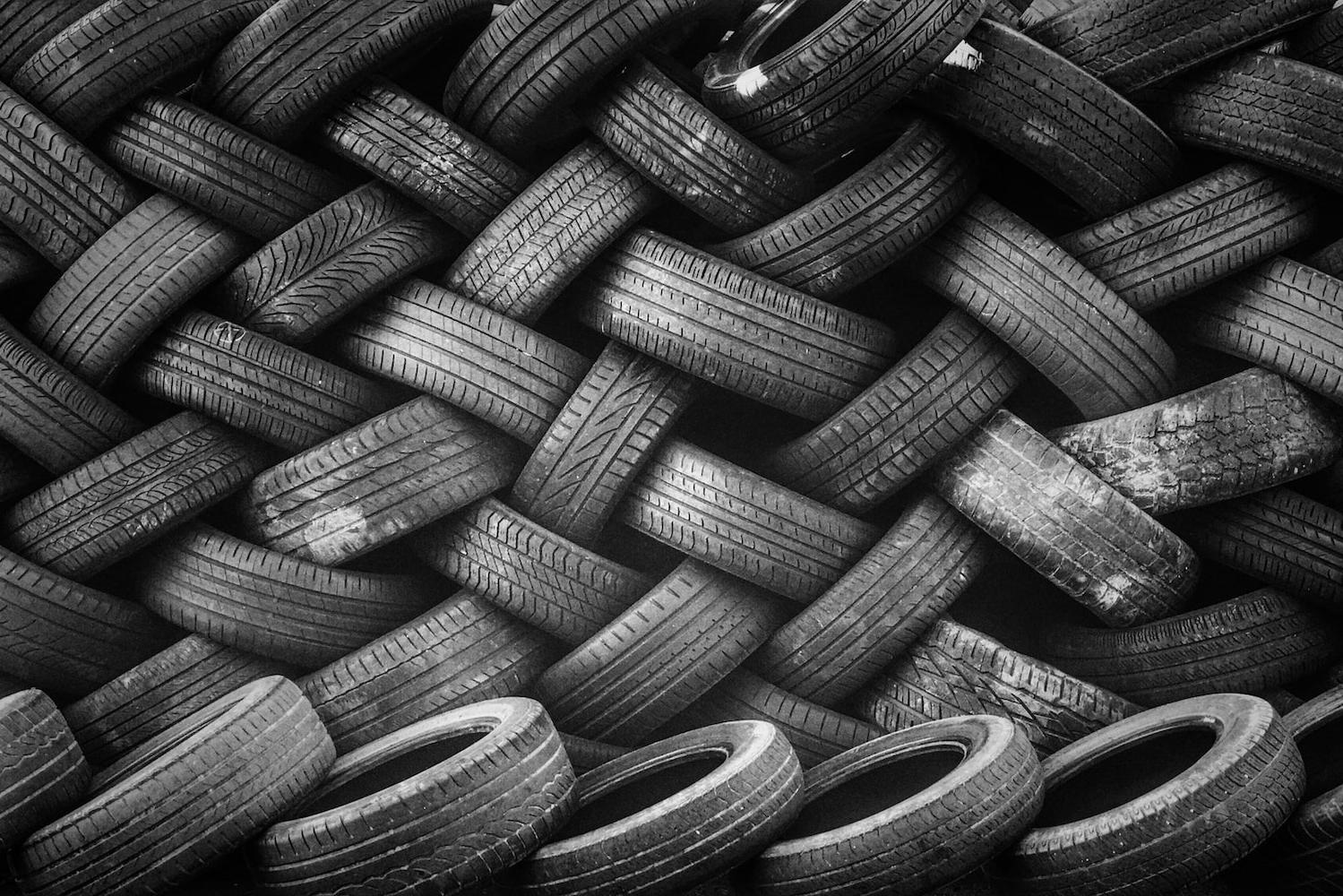
Tires may not be the first commodity that comes to mind when imagining a circular economy. Their numbers are hidden in plain sight. Globally, approximately 1 billion tires reach the end of their lives each year, and the potential consequences of discarding, stockpiling and dumping tires can include catching fire and breeding mosquitoes.
The good news is that end-of-life tires, or ELT, are a valuable resource for the circular economy. Natural rubber, of course, is a significant component, but it only constitutes about a fifth of a passenger vehicle’s tire. Elements like synthetic polymers, steel and textiles also play a part. Each has a unique purpose for tire performance, and each remains valuable, even at end of life. Ensuring that these components get to an appropriate end use, however, takes deliberate research, planning and management.
Most end-of-life tires are already recovered. Circularity is the next step.
The bulk of ELT are already recovered, according to the 2019 Global ELT Management report from the Tire Industry Project (TIP), a CEO-led sustainability forum for the tire industry that sits under the umbrella of the World Business Council for Sustainable Development (WBCSD). Within the 45 countries considered, accounting for over 80 percent of the world’s vehicles in use, 86 percent of ELT were recovered. These findings represent a significant improvement over the last few decades. Only 30 years ago, the United States was recovering 17 percent of its ELT, compared to 75 percent in 2019.
The tire industry continues to roll along, and its next destination is circularity. Members of TIP, leaders in the tire industry, provide useful indications of where the industry is growing. Some companies have been reworking the resources they use in their tires. Goodyear, for example, has replaced petroleum-based components with soybean oil in some tread compounds. Pirelli aims to use at least 40 percent renewable materials in select consumer tires by 2025.
Toward more sustainable natural rubber, and to lessen reliance on Hevea brasiliensis — the trees which provide the world’s supply of natural rubber — Bridgestone has invested in the development of an alternative source, guayule, a rubber-producing plant indigenous to the hot and dry environments of the southwestern United States and north-central Mexico. And the Michelin Group’s 2050 target — to source all of its materials from recycled or renewable sources — will do its part to move the industry’s needle toward circularity. The group is also engaged in recycling end-of-life tires.
Understanding the importance of research for continued progress, as a whole, TIP members focus on advancing global knowledge about ELT management (through initiatives like its state of knowledge reports). Tire manufacturers, recyclers and regulators are all calling for more research and innovation in support of the sustainable management of ELT. Last year, the U.S. Tire Manufacturers Association (USTMA) reported a 20 percent decrease in tire recycling nationwide since 2013, noting the importance of market development.
“Three decades after we successfully eliminated 94 percent of the over 1 billion scrap tires stockpiled around the country, this report reveals that efforts to find and develop new uses for scrap tires have stalled,” Anne Forristall Luke, president and CEO of USTMA, said in a statement. “We must take immediate steps to grow new and existing markets to recycle 100 percent of scrap tires. This not only protects our health and the environment — it drives innovation and jobs.”
Rubber modified asphalt a promising ELT innovation
Organizations like The Ray — a nonprofit pursuing net-zero roadway solutions on an 18-mile stretch of interstate highway in Georgia — are forging the way to a circular economy for tires through research, experimentation and advocacy. This year, The Ray worked with USTMA to examine the environmental impacts and benefits of one destination for end-of-life tires: rubber modified asphalt, an innovative paving material made from asphalt cement and ground ELT that carries a significantly lower carbon footprint compared to traditional asphalt pavement.
The Ray has already installed rubber modified asphalt on one mile of the interstate’s four lanes, upcycling over 40,000 pounds of rubber from ELT in the process. While testing the pavement, the organization is looking to investigate previous research, Allie Kelly, executive director of The Ray, says — pursuing questions such as: Does rubber modified asphalt really make quieter and longer-lasting roads that resist cracking, as researchers hope? Do these roads manage stormwater more effectively? Can adding rubber reduce tire wear?
"When you understand the knowns, you also understand the gaps, and then you can more strategically find any follow-up studies or follow-up research,” Kelly says. Results were published last summer with an immediate call for more research. In reviewing more than 300 scholarly sources and surveying 26 state highway agencies, the study found that rubber modified asphalt is a promising circular solution that reduces costs over the life of the asphalt, extends pavement life and reduces roadway noise, among other verified benefits.
Valuing ELT, innovating toward a circular economy
Kelly emphasizes that a key to successfully giving tires a “second life and beyond” is changing how we view ELT. “The problem is that when the tire gets to the end of its life on a vehicle, we don't regard it as a commodity. We regard it as scrap,” she says. “And we don't really invest in scrap.”
There has been great innovation in manufacturing tires, Kelly notes — from airless tires to sensor additions to 3D printable tires. The Ray, recognizing the value in ELT, is advocating for innovation throughout the tire lifecycle, she says.
The shift from standard ELT recycling practices has only just begun. While rubber modified asphalt has great potential as a destination for ELT, Kelly recognizes a broader purpose for organizations like hers in the growth of this corner of the circular economy: “I think what our role is at The Ray, with partners like USTMA, is to make sure that we're taking full advantage of end-of-life opportunities for scrap tires,” she says.
Driving progress, together
As The Ray pursued its study on rubber modified asphalt, TIP was rolling out a series of value-chain workshops for sustainable ELT management that aimed to improve the exchange of knowledge and good practices between stakeholders. The fruits of these efforts included the recently published ELT Toolkit for Improved ELT Management Systems. The toolkit is directed toward markets that have the potential to recover more ELT; TIP also plans to establish a digital platform to facilitate knowledge-sharing among stakeholders.
Citing how little of the world has achieved circularity, the World Economic Forum claims that a circular economy “requires unprecedented collaboration.” The ten member companies of TIP certainly can’t transform the global management of ELT on their own. That’s the beauty of TIP’s knowledge-sharing approach — good practices and approaches that work should be shared so they can reach the stakeholders and regions where they are most needed. Toward a circular economy for tires, knowledge sharing and stakeholder cooperation will be the key drivers of progress.
This article series is sponsored by the Tire Industry Project and produced by the TriplePundit editorial team. Members of the Tire Industry Project (in alphabetical order) are Bridgestone, Continental, Goodyear, Hankook, Kumho Tire, Michelin, Pirelli, Sumitomo Rubber, Toyo Tires, and Yokohama Rubber.
Image credit: Imthaz Ahamed/Unsplash
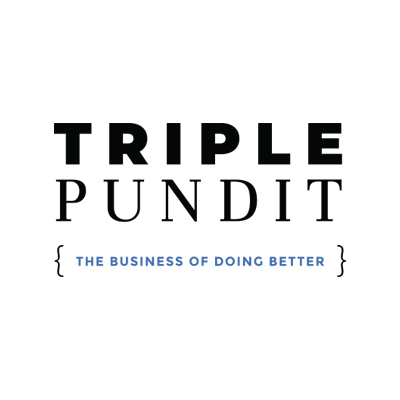
TriplePundit editors offer news and insights on sustainable business.