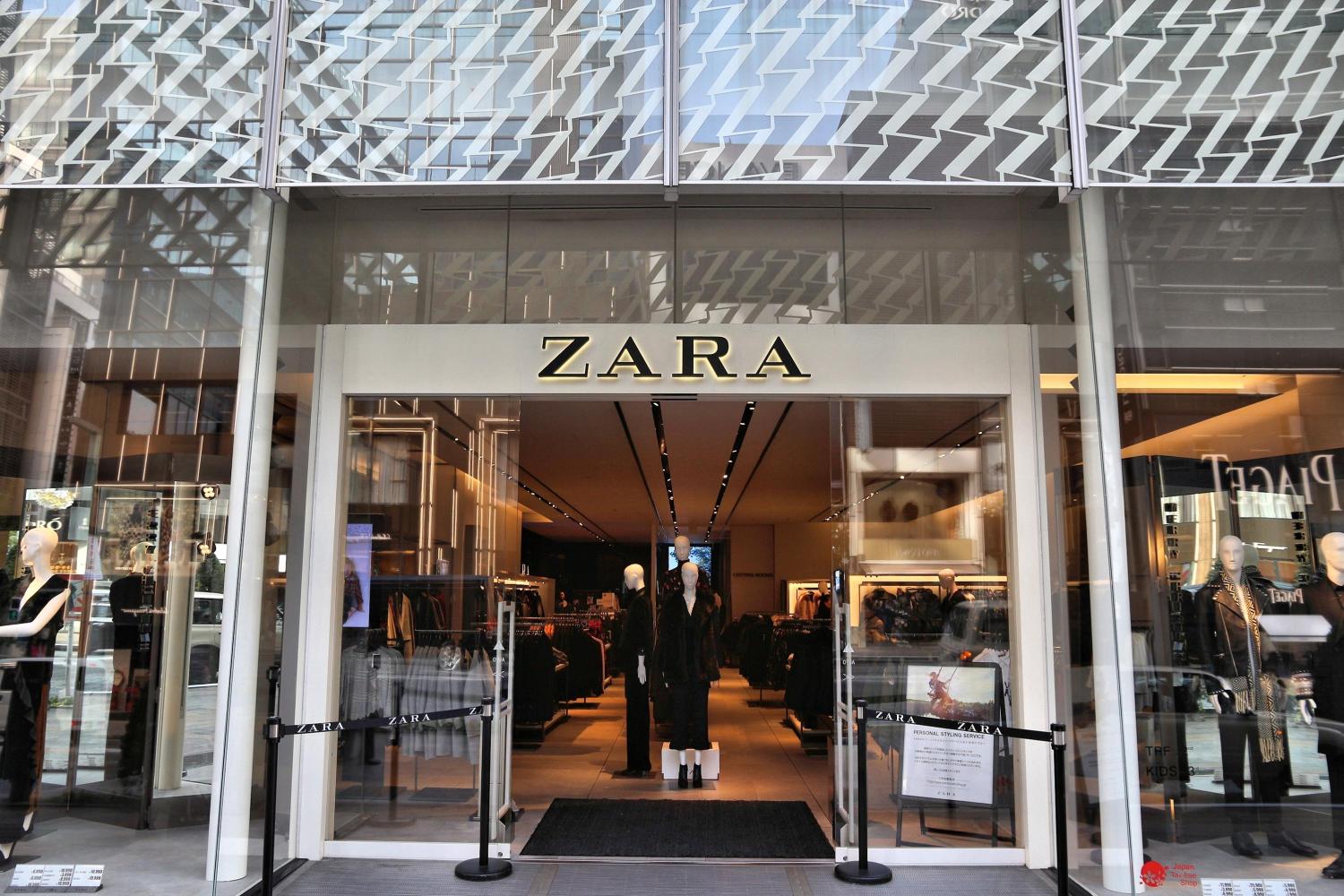
It may seem like magic, but it’s real. The global retailer Inditex is producing a new capsule collection of party dresses for its largest retail branch, the well-known Zara chain of apparel stores, made with fabric sourced from recycled carbon. The new collection is a partnership with the high-tech recycling company LanzaTech.
Recycled carbon steps into the limelight
Recycled carbon is beginning to emerge for industrial uses, but so far, the most common area is in fossil fuel extraction, where captured carbon is deployed to enhance production from oil wells.
That’s not exactly a climate-friendly use of recycled carbon. A more helpful approach under development is to cut emissions related to cement production.
Another emerging example is in the agricultural sector, where crops grown in greenhouses can be stimulated with extra carbon captured from the outside air.
For the most part, this activity has been taking place out of the public view. Zara’s new line of recycled carbon clothing brings it out from behind the curtain.
Introducing the new collection as a line of eye-catching party dresses does not add much volume to the market for recycled carbon fabric, but it adds an audacious twist that could stimulate more interest and help demand scale up quickly.
This is not your father’s recycled carbon party dress
As for the magic, that is becoming almost commonplace. LanzaTech is among a growing number of innovators that have developed technology that can capture airborne pollutants and deploy them as chemical building blocks.
Much of the technology is still in development, but LanzaTech has been running ahead of the pack with a system that deploys engineered microbes to digest airborne pollutants, with a focus on harvesting carbon dioxide emissions from steel mills. The system can also apply to agricultural waste among other sources.
The digestion process is more familiarly known as fermentation. Instead of yeast, though, the LanzaTech process deploys waste carbon. The end result is a propriety brand of ethanol, called Lanzanol.
Ethanol is better known as a fuel for cars, made from corn and other organic matter. It is even better known as the alcohol that makes fermented beverages intoxicating.
Ethanol is also among the most common building blocks for industrial use. It is an intermediate step in many chemical processes, including those leading to the production of plastics.
For the next step in the pathway to recycled carbon fabric, Lanzanol is converted to monoethylene glycol, which is the feedstock for polyester yarn among many other plastics.
The company India Glycols Limited has been topped for that part of the process. Capping off the sequence is Far Eastern New Century, which spins the monoethylene glycol into yarn.
Group hug for U.S. taxpayers
If LanzaTech’s partnership with Zara sparks more activity in the pollution-to-fashion field, U.S. taxpayers can give themselves a pat on the back for providing the company with a financial assist.
In 2013, LanzaTech won a $4 million grant from the U.S. Department of Energy, for a project under a new research initiative called REMOTE, for "Reducing Emissions using Methanotrophic Organisms for Transportation Energy.” The initiative was aimed at converting waste methane into new fuels and other chemicals.
Michigan Technological University also partnered in the project to assess environmental impacts. Louisiana State University contributed its bio-reactor modeling expertise, and City College of New York contributed design work for the reactor.
Growing the market for recycled carbon
The market for recycled carbon could break out of the chicken-or-egg phase, now that the Zara collaboration has demonstrated the potential for demand.
That leaves the supply side to be addressed, and LanzaTech appears to have that in hand as well.
Last week the global steel maker ArcelorMittal announced a $30 million investment in LanzaTech, building on a carbon recycling collaboration that began in 2015.
The carbon capture side of the project is currently under construction at an ArcelorMittal plant in Ghent, Belgium.
With the addition of LanzaTech’s fermentation technology, ArcelorMittal anticipates that the plant will produce 80 million litres of bio-ethanol per year while reducing the carbon footprint of the facility.
Image credit: Adobe Stock
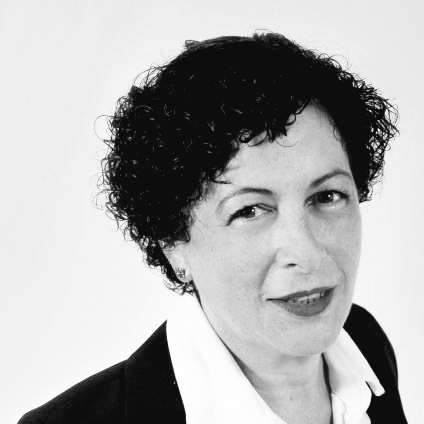
Tina writes frequently for TriplePundit and other websites, with a focus on military, government and corporate sustainability, clean tech research and emerging energy technologies. She is a former Deputy Director of Public Affairs of the New York City Department of Environmental Protection, and author of books and articles on recycling and other conservation themes.