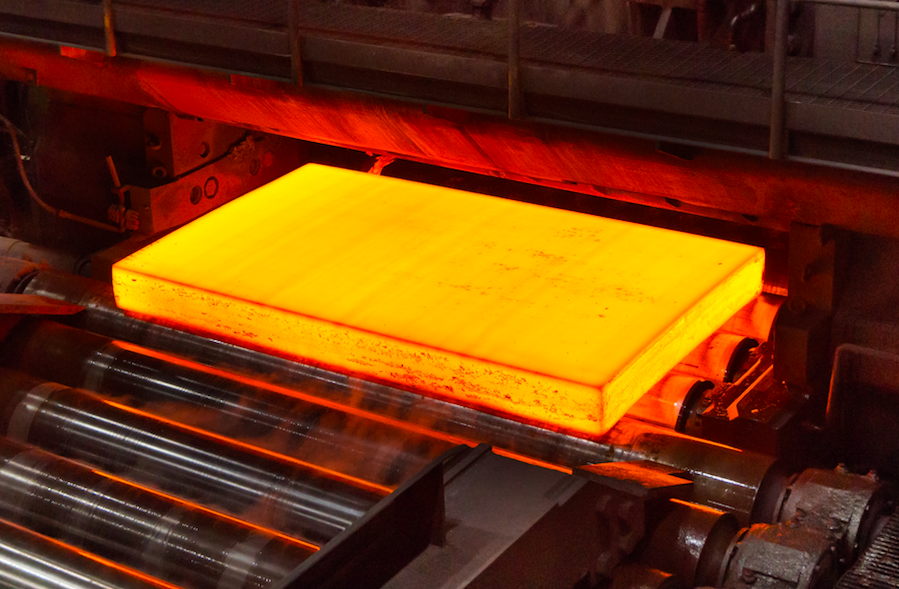
It doesn’t take much intuition to sort out that the manufacturing of steel is carbon-intensive. The reality is also that steel provides much of the backbone that makes our daily lives possible, from home to work and getting just about anywhere in between or far away.
The global steel industry recognizes that it has its part to play if the world will ever fully transition to a low-carbon economy; consultancies such as McKinsey has said the sector had better get moving if steel producers don’t want to see a good portion of their assets vulnerable to risks in the near future.
Considering the recent news coming from the IPCC and the general agreement that climate change is occurring faster than we had thought just a few years ago, time is of the essence. And with most estimates agreeing that global steel production accounts for about 7 percent of the world’s total emissions, the industry can certainly make a difference with new investments allowing for the use of next-generation fuels. That is, of course, if they can scale up.
One Swedish company says it’s already embarking on such a path.
Earlier this week, the Stockholm-based steel producer SSAB announced it had delivered its first batch of steel that is made completely without burning coal or coke. Instead, the company was able to produce this material for Volvo by using its own proprietary technology, which runs on energy that is 100 percent fossil fuel-free, i.e. “green hydrogen.”
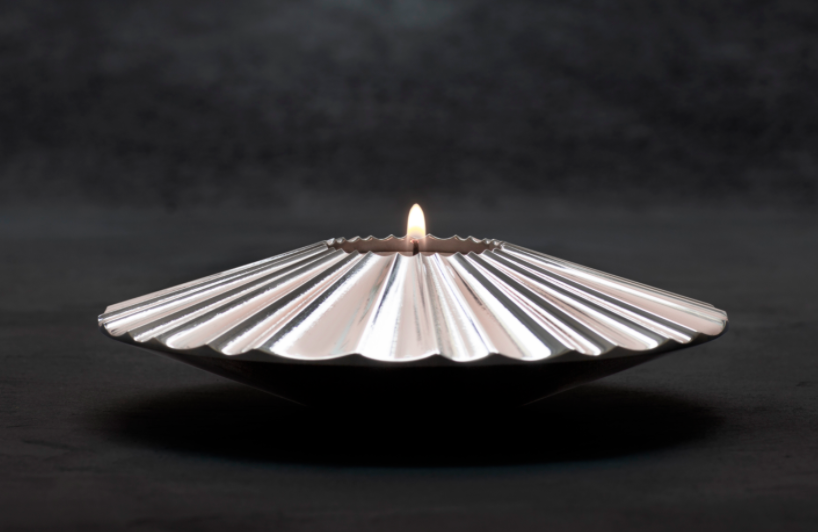
SSAB and Volvo first revealed this partnership back in April. Should the companies’ partnership continue as planned, the automaker will build some concept cars with the low-carbon steel this year. Smaller-scale production will launch in 2022, and assuming SSAB will be able to accelerate the production of its steel using green hydrogen, commercial-level manufacturing could start in 2026.
As TriplePundit has long reported, hydrogen is crucial to the global economy, as it is used for countless products, from food processing to manufacturing pharmaceuticals. Hydrogen is also easily transported by sea, rail or pipelines. The problem is that ample reserves of hydrogen do not exist in nature, so it must be extracted from another source, which usually is natural gas.
But if hydrogen can be extracted cost-effectively from water through a process called electrolysis, which applies an electrical current to unleash bubbles of hydrogen – and if that can be so with renewable energy sources such as solar and wind resources, therein lies a game-changer. That scenario would be especially true of the automotive sector – and a few such companies are already taking notice. Much of this talk has revolved around what would power next-generation cars, as in fuel cells versus all-electric drive trains versus the internal combustion engine.
Volvo’s investment, in contrast, is focused on the materials needed to manufacture the cars in itself; and if Sweden’s iconic automaker and SSAB can figure this out, then other companies beyond the automotive sector can solve the puzzle long challenging the global business community – how to clean up those massive, complicated and polluting supply chains.
Image credits: SSAB
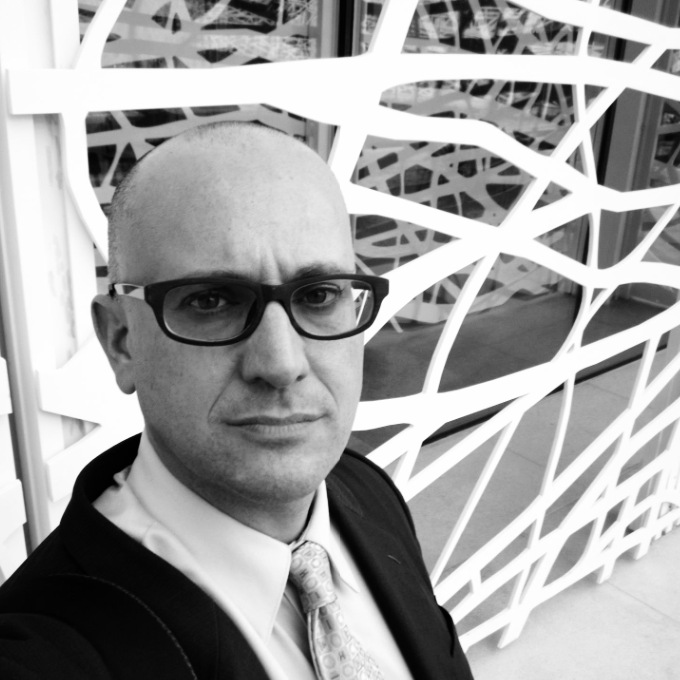
Leon Kaye has written for 3p since 2010 and become executive editor in 2018. His previous work includes writing for the Guardian as well as other online and print publications. In addition, he's worked in sales executive roles within technology and financial research companies, as well as for a public relations firm, for which he consulted with one of the globe’s leading sustainability initiatives. Currently living in Central California, he’s traveled to 70-plus countries and has lived and worked in South Korea, the United Arab Emirates and Uruguay.
Leon’s an alum of Fresno State, the University of Maryland, Baltimore County and the University of Southern California's Marshall Business School. He enjoys traveling abroad as well as exploring California’s Central Coast and the Sierra Nevadas.