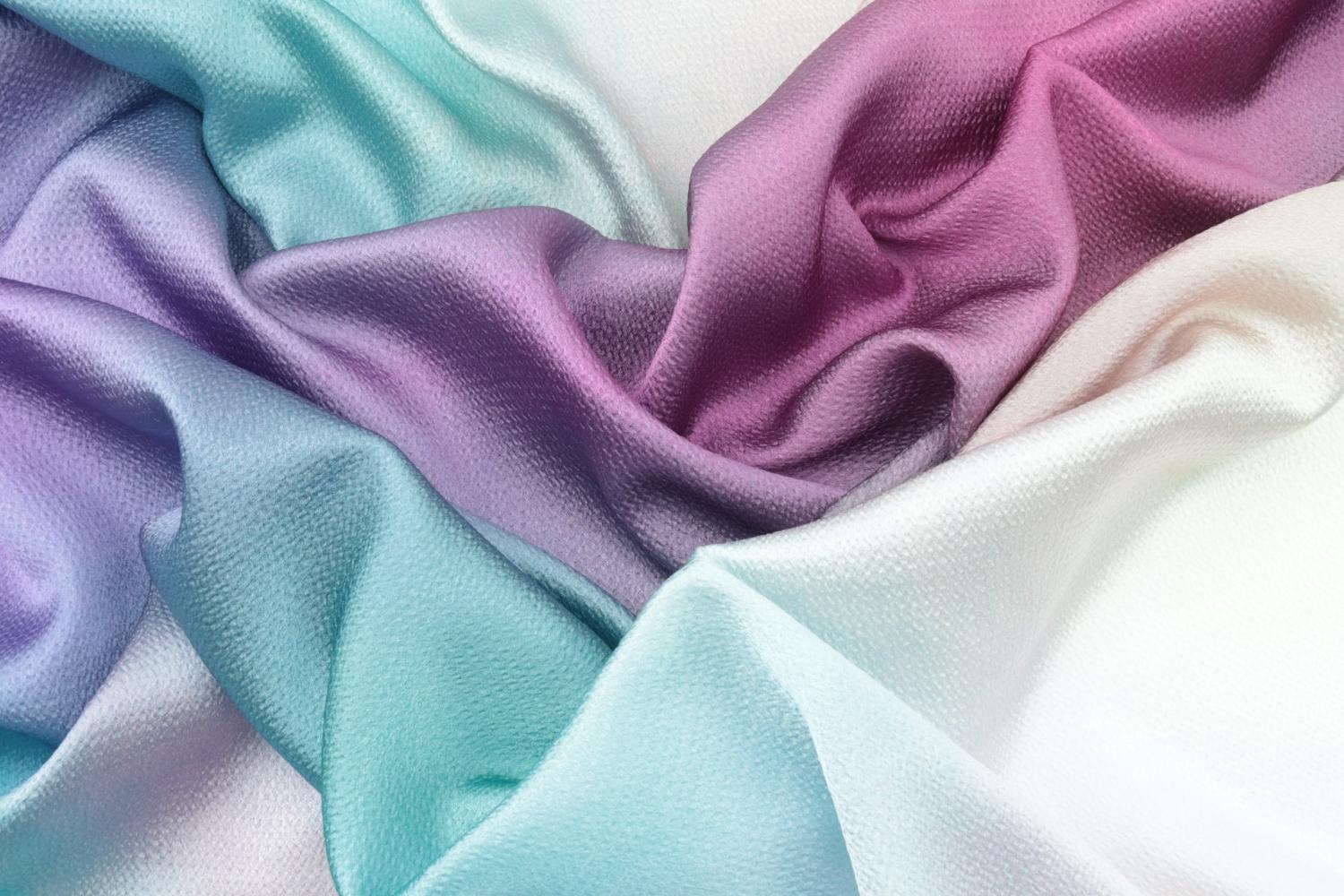
The industry consortium Fashion for Good launched last year with the goal of bringing innovative, disruptive solutions for recycling rayon and other synthetic cellulosic fibers to the global textile market. Now the group has broadened its reach to include polyester. In both cases, they are aiming high. Rather than downcycling recovered fibers, Fashion for Good is aiming to increase fabric recycling and send such fibers back into the apparel manufacturing stream.
Chipping away at a mountain of fabric waste, with chemistry
Based in Denmark, Fashion for Good is a soup-to-nuts partnership founded with a singular purpose: to deploy innovative new chemical recycling processes in the fashion industry.
Conventional fabric recycling typically involves mechanical or heat-based processes, such as shredding or melting. The resulting fibers are often of lesser quality, which limits the scope of the market for recycled material.
For example, until recently plastic bottles could not be recycled into new plastic bottles. The market for recycled paper was similarly limited.
New advances in recycling technology have expanded the market for recycled paper and plastics. That includes new chemistry-based processes that break down plastic waste into elemental building blocks, which can be reassembled into new materials that perform as well as — or even better than — the source materials.
Textile-to-textile fabric recycling would certainly disrupt the fashion industry as we know it today. When Fashion For Good started its “Full Circle Textiles Project - Scaling Innovations in Cellulosic Recycling” program last year, the organization stated that up to 73 percent of clothing globally ends up in the trash, and less than 1 percent of recycled fiber makes its way back into fabric for the fashion industry.
Polyester fiber targeted for recycling
Those figures probably haven’t budged much since last year, but Fashion for Good’s collaborative, team-based strategy demonstrated enough progress on cellulosic fiber recycling to form the basis for a second team, focusing on polyester.
“The Full Circle Textiles Project – Polyester brings together a consortium of stakeholders including brands, innovators, supply chain partners and catalytic funders – a structure that has proven successful in driving and scaling disruptive innovation in the industry,” explains Fashion for Good.
The polyester team includes the catalytic funder Laudes Foundation, along with Adidas, Bestseller, C&A, PVH Corp., Target and Zalando. Also affiliated with the team are Arvind Limited, the Fabrics Division of W. L. Gore & Associates and Teijin Frontier.
On the chemistry side, the firms Cure Technology, Garbo, Gr3n and Perpetual are among the recycling innovators selected to apply chemical processes to post-consumer textile waste.
“The project aims to validate the technologies and the scaling potential; prompting further implementation/offtake agreements to drive chemical recycling in the industry and mobilize more funding into the technology,” Fashion for Good explains.
This is not your parents’ fabric recycling
The Fashion for Good polyester team already has a running start. Cure Technology, for example, has a pilot plant up and running. Its chemical-based process can recycle other plastics in addition to polyester textiles, including PET bottles, films, and carpets.
The diversified firm Garbo has formed extensive industry contacts since its roots in 1997 within the field of materials recovery for the semiconductor industry. Among its current collaborations is the Reciplast initiative aimed at plastics used in the packaging and auto industries.
Garbo states that its “ChemPET” process is “able to treat most of the PET-based waste that is currently not recoverable.” The process yields a building block called BHET (bis-hydroxy-ethylene-terephthalate). Once purified, BHET can be used in place of virgin petrochemical inputs.
The firm Gr3n demonstrates a similar level of cutting edge-technology. Its energy-efficient process takes place in microwave-assisted reactors.
“We can obtain terephthalic acid (TPA) and monoethylene glycol (MEG) starting from bottles and textile in less than 10 minutes and working at less than 200°C,” the company notes.
More bad news for oil and gas stakeholders
Rounding out the innovation team is Perpetual, which emphasizes that its chemical “deconstruction” process yields a drop-in replacement for virgin petrochemicals.
“…the filtered ester stream is ready to be reformed into long repetitive chains (i.e. polyester) using the same equipment and comparable process conditions as would be used for conventional petrochemicals; except, in this case, the source material is used post-consumer bottles and not environmentally harmful new crude oil petrochemical derivatives,” Perpetual explains.
That emphasis on drop-in replacement should be a warning sign for those hoping to keep demand for oil, natural gas, and coal humming along.
Fossil energy stakeholders are depending on increasing demand for plastic and other petrochemicals to stay afloat in future years, now that both the power generation and the transportation markets have begun to show signs that rapid decarbonization is immanent. However, plastics are no longer a sure thing.
The trend towards reducing fossil energy and petrochemical dependency already shows signs of accelerating in the power generation and transportation markets.
With partnerships like Fashion for Good, the fabric recycling movement is poised to disrupt the global textile market as well.
Image credit: Divazus Fabric Store via Unsplash
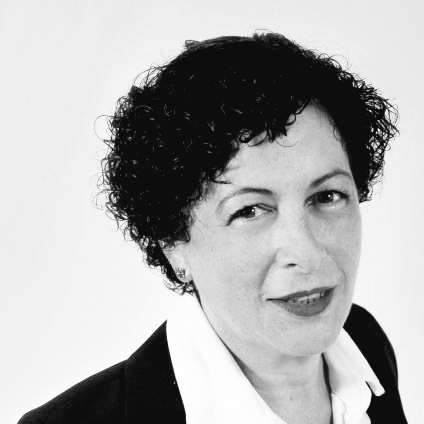
Tina writes frequently for TriplePundit and other websites, with a focus on military, government and corporate sustainability, clean tech research and emerging energy technologies. She is a former Deputy Director of Public Affairs of the New York City Department of Environmental Protection, and author of books and articles on recycling and other conservation themes.