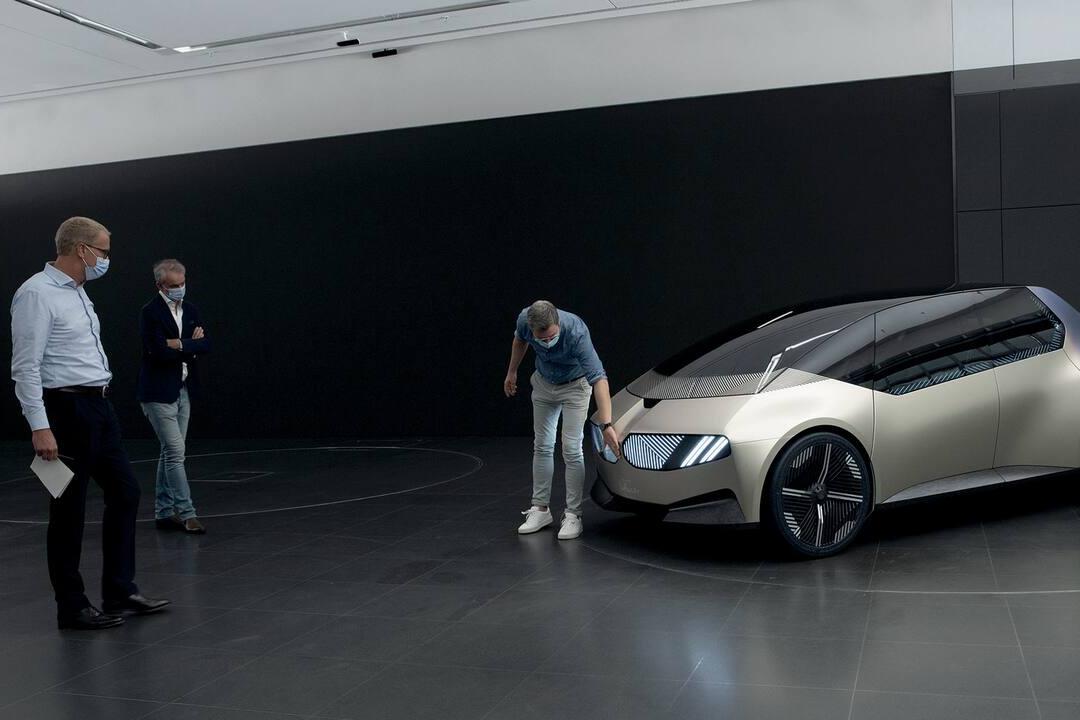
BMW says it has a vision of a circular and sustainable model for the future of mobility.
The global auto industry generally gets good marks for recycling, mainly because most car parts are made of metals that are fairly easy to recover. That state of affairs is about to be upended by the electric vehicle (EV) revolution, which will send millions of spent EV batteries and other materials into the recycling stream. Automakers that seek to capture the hearts and minds of sustainability-minded car buyers are beginning to engineer new elements of the circular economy into their lineups, and BMW provides a good example of that effort.
Car buyers expect cars to be recycled
It seems to be common knowledge that the recycling rate for conventional vehicles is fairly high, and that is actually the case.
The U.S. Environmental Protection Agency (EPA) explains that “approximately 75 percent (by weight) of a vehicle is composed of metals that are recycled. The remainder — auto shredder fluff (consisting of plastics, textiles, glass, and other nonmetallic materials) — is disposed of primarily in landfills.”
That sounds reasonable enough. The recycling rate is even more impressive for the lead-acid batteries used in conventional cars, at 99 percent.
However, it’s still the case that approximately 25 percent of materials in a conventional vehicle are not recycled. EPA estimates that more than 10 million vehicles go to salvage yards and other recovery facilities every year, so the amount of unrecovered vehicle waste adds up considerably.
“Greater emphasis on designing vehicles with recovery in mind is pushing vehicle manufacturers to reduce toxic and hazardous constituents in vehicles and improving the prospect for recovering more of the non-metallic material inputs,” EPA optimistically noted in a recently archived overview of vehicle recycling in the U.S.
Pushing the sustainable car envelope
Automakers and other industry stakeholders have been introducing more sustainable materials into non-metallic car parts in recent years. Dandelion rubber is one early example that dates back to the 20th century. Goodyear is still pursuing that pathway, along with soybean oil, rice husks and other sustainable alternatives to natural rubber.
In more recent years, Ford has assembled a laundry list of bio-based inputs for various car parts including soy, castor, wheat, kenaf, cellulose, wood, coconut and rice. Captured carbon dioxide and recycled materials like plastic bottles, carpeting and old blue jeans are also part of the company’s sustainability plan.
Volkswagen upped the ante just last week by making sustainability a main feature in its promotion of the ID.LIFE concept electric vehicle. Pitched as a small, affordable EV for first-time car buyers, the concept features a clear coat on the body parts tinted with wood chips and reinforced with a bio-based hardener.
“The air chamber textile for the roof and front cover is made from 100 percent recycled PET bottles. In the interior, wood in the dashboard and rear seat surrounds is combined with ArtVelours Eco for the seat surfaces and door trims. Bio-oil, natural rubber and rice husks are just some of the materials that serve as a basis for the tires on the ID. LIFE,” Volkswagen adds (note: ArtVelours is partly made with recycled PET bottles).
BMW and adding cars to the circular economy
BMW appears to have put all the pieces together in a circular economy package that takes the sustainability theme a step farther.
Earlier this year the company previewed its forthcoming “Neue Klasse” lineup of electric vehicles, and last week it announced a series of steps linking EV manufacturing to the circular economy.
One of those steps is joining the Science Based Targets Initiative (SBTi), which commits BMW to measurable actions in support of the Paris Agreement on climate change.
Those actions go far beyond reducing tailpipe emissions. In the new announcement, BMW committed to the goal of reducing full lifecycle carbon dioxide emissions per vehicle by at least 40 percent, including emissions related to the upstream supply chain as well as manufacturing the cars, and providing liquid fuel or electricity during their driving lifespan.
The plan also includes increasing the use of secondary materials to as high as 50 percent. BMW makes it clear that the development of new engineering strategies and new markets will be required to meet that goal, but the company has given itself a head start through collaborations with BASF and the recycling firm ALBA for plastics recycling. Rather than down cycling plastic car parts into carpet fiber and other low-value materials, the aim is to use chemical processes and other new recycling methods to up-cycle old plastic car parts into high-performing materials for new cars.
Cutting down on conflict materials and social costs
The BMW plan also pays particular attention to the materials used in EV batteries. Many other EV car parts are similar or identical to conventional car parts, but EV batteries introduce additional materials into the recycling stream, including cobalt and nickel along with aluminum for the battery housings.
BMW notes that there are both market and sustainability reasons for focusing on secondary materials for EV batteries. In addition to a savings on lifecycle global warming emissions, BMW emphasizes that the use of secondary materials helps to avoid ecosystem impacts related to mining.
The use of recovered materials can also help automakers avoid becoming associated with human rights abuses related to overseas supply chains.
“The mining and trading of conflict materials carries the possible risk of associated infringements of environmental and social standards,” BMW explains. “The BMW Group has established numerous measures to counteract this risk, including membership of the Responsible Minerals Initiative. However, the most efficient strategy for avoiding risks is to minimize the mining of such primary materials.”
Recycling: easier said than done
BMW has already introduced its concept for the circular economy electric vehicle of the future. However, there is still one important loose end to be addressed.
As amply demonstrated by the dismal state of affairs in the global plastics recycling industry, significant policy gaps and enforcement pitfalls can easily spin recyclable materials out of the circular economy loop and into the environment.
In addition, illegal or substandard recycling operations can give rise to new impacts. For example, the rate of 99 percent recycling for lead-acid batteries looks pretty on paper, but recent investigations have revealed significant public health and environmental impacts related to lead-acid battery recycling operations in Asia and elsewhere.
The focus on sustainable materials and lifecycle impacts is a good start, but auto manufacturers like BMW will have to extend their reach to include the development of safe, efficient recycling streams in order to claim their place in the circular economy of the future.
Image credit: BMW corporate site
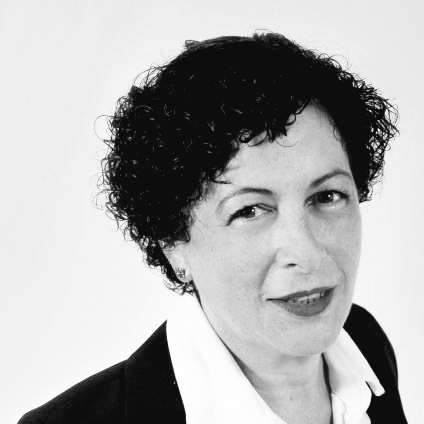
Tina writes frequently for TriplePundit and other websites, with a focus on military, government and corporate sustainability, clean tech research and emerging energy technologies. She is a former Deputy Director of Public Affairs of the New York City Department of Environmental Protection, and author of books and articles on recycling and other conservation themes.