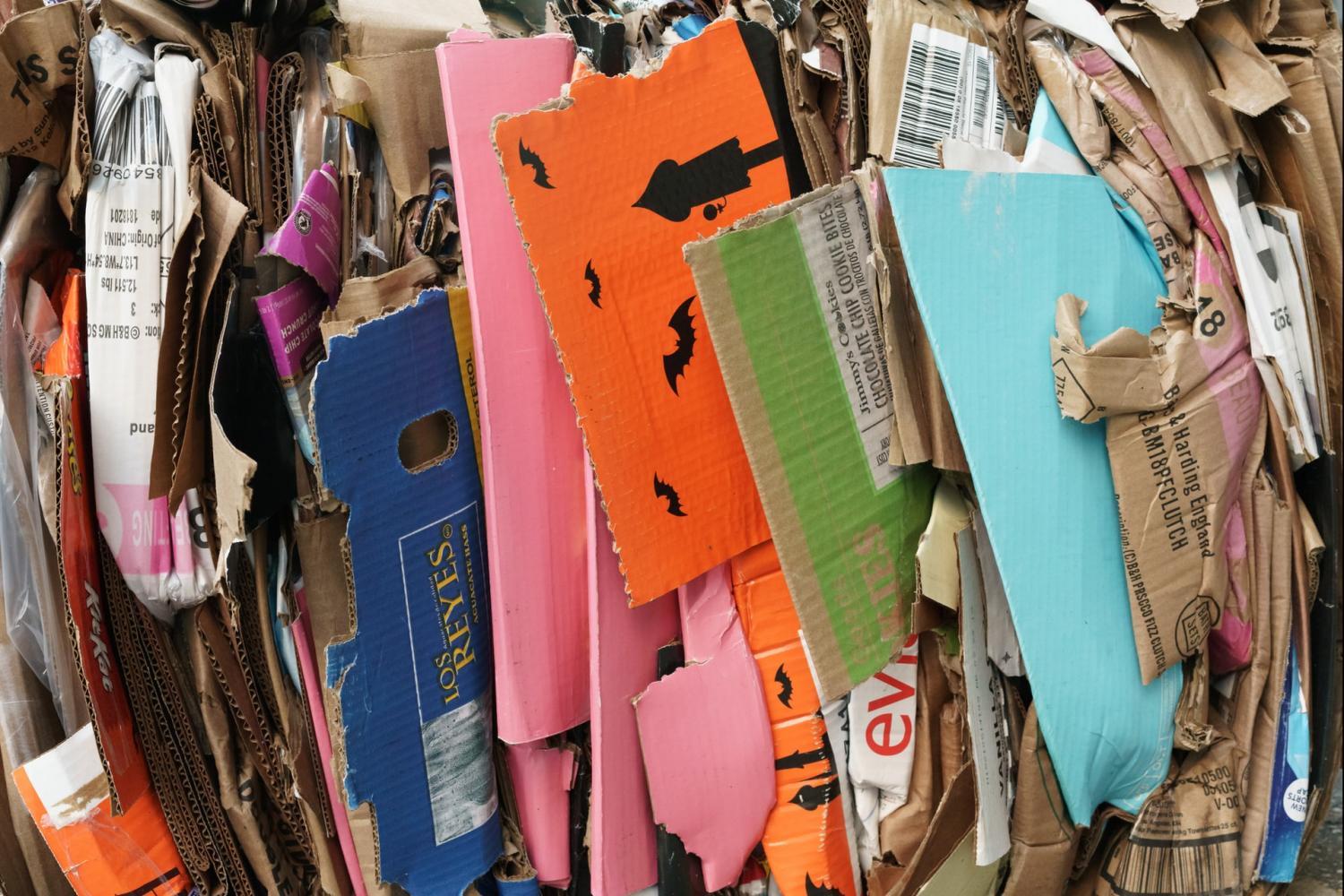
Analysts were already predicting the end of recycling last year, when mountains of waste began to pile up after China and other countries began refusing to accept such shipments from overseas. The COVID-19 outbreak has further complicated global recycling markets. However, there are indications that the recycling industry can emerge from the crisis as a stronger and more resilient force than ever before.
Not all recycling is created equal
First, it is important to note that every recyclable material has its own market. The COVID-19 crisis has had a differing impact on different types of recyclables.
Paper is a case in point. The crisis has touched off a surge in demand for paper products typically made with recycled fibers, like toilet paper and cardboard shipping boxes.
The demand side is just one aspect of the COVID-19 effect, though. The crisis has also had an impact on the incoming stream of paper for recycling, as workers around the globe are confined to home. The recycled paper supply chain was stronger when more workplaces were open. With more people working from home, less paper is available for recycling.
Expanding the market for recycled paper with new technology
That demand-supply tension could remain challenging for paper manufacturers, all the more so as new recycling technology emerges.
One especially interesting development is a new recycling facility planned for the city of Lancaster, California. It will take in mixed paper from the municipality and subject it to a patented gasification process, to produce reclaimed hydrogen.
Hydrogen is used in many common industrial processes, from steelmaking to food production. Its role in the transportation sector has also been growing.
Fossil fuels comprise the main source of hydrogen today, but green hydrogen alternatives are emerging. So far, the activity has mainly focused on splitting water with an electrical current, deploying wind or solar power.
The gasification option could provide an additional commercial pathway for green hydrogen, while also helping municipal governments develop more sustainable and economical waste management plans.
The company behind the hydrogen project, SGH2, also has its eye on gasifying other types of waste.
There is keen interest in the success of the SGH2 project across the industry. In addition to support from the city’s policy makers, the project is being shepherded by a public-private consortium that includes the Department of Energy’s Lawrence Berkeley National Laboratory, UC Berkeley, and the companies Fluor, Thermosolv, Integrity Engineers, Millenium, HyetHydrogen and Hexagon.
Upcycling for better foam recycling
Another interesting technology breakthrough is taking place in the area of polyurethane foam recycling.
The foam problem is a significant one because of its sheer size, as polyurethane is the common denominator in mattresses and cushions among many other items.
Foam resists melting and reformation, so it cannot be recycled like other plastics. Until now, the main approach has been to shred it and downcycle it in the form of carpet padding and similar products, or simply burn it for energy.
The solution may be at hand. Researchers at Northwestern University and the University of Minnesota have developed a new process that transforms foam into a durable, moldable plastic, creating new pathways for upcycling.
As with the paper-to-hydrogen project, the new approach does not simply reduce a material into smaller bits. Instead, it transforms the material into a new substance that can then be deployed for other uses.
Making industrial waste better than new
Industrial waste is another area in which the transformative approach could have a significant impact.
One recent example comes from an Australian research consortium, which has combined waste cooking oil, waste sulfur, and the petroleum refinery waste chemical dicyclopentadiene to create a new kind of rubber.
According to the researchers, the new rubber is durable enough to use for car tires.
The new rubber can also self-repair seamlessly and return to its original strength within minutes, by applying a simple catalyst at room temperature.
Flinders University, which hosts the research, notes that every year the equivalent of 48 million tires reach the end of their useful lives in Australia alone, and only 16 percent are recycled. Making tires with a more durable, repairable form of rubber would have a significant impact on the tire disposal problem as well as providing a new market for industrial waste.
Bio-based solutions for plastic waste
This kind of two-tiered thinking is also evident in the field of bio-based recycling, where microbes and natural digestive processes do the heavy lifting.
One recent example is an entire food system envisioned at Pennsylvania’s Clarion University, where researchers are exploring the use of moth larvae that can digest polyethylene.
The new system is a complete waste-to-food cycle in which larvae at recycling centers are eventually fed to chickens for human consumption.
The discovery of a plastic-eating microbe by a Germany-based research team holds similar promise. The research is part of a broader European Union effort aimed at breaking down petrochemical waste into biodegradable materials for re-use.
As the bottom line motivation for green products and packaging continues to accelerate, look for new, transformative recycling pathways to emerge. Recycling as we know it may be going away, but only because the recycling industry of the future is beginning to take shape.
Image credit: Michael Jin/Unsplash
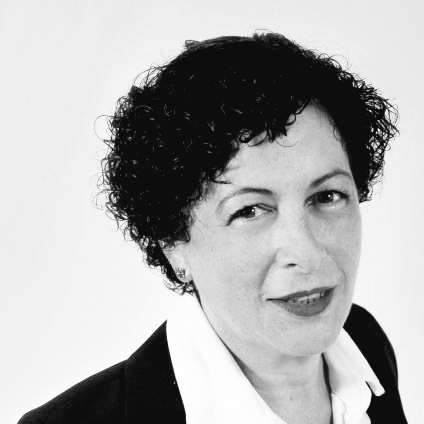
Tina writes frequently for TriplePundit and other websites, with a focus on military, government and corporate sustainability, clean tech research and emerging energy technologies. She is a former Deputy Director of Public Affairs of the New York City Department of Environmental Protection, and author of books and articles on recycling and other conservation themes.