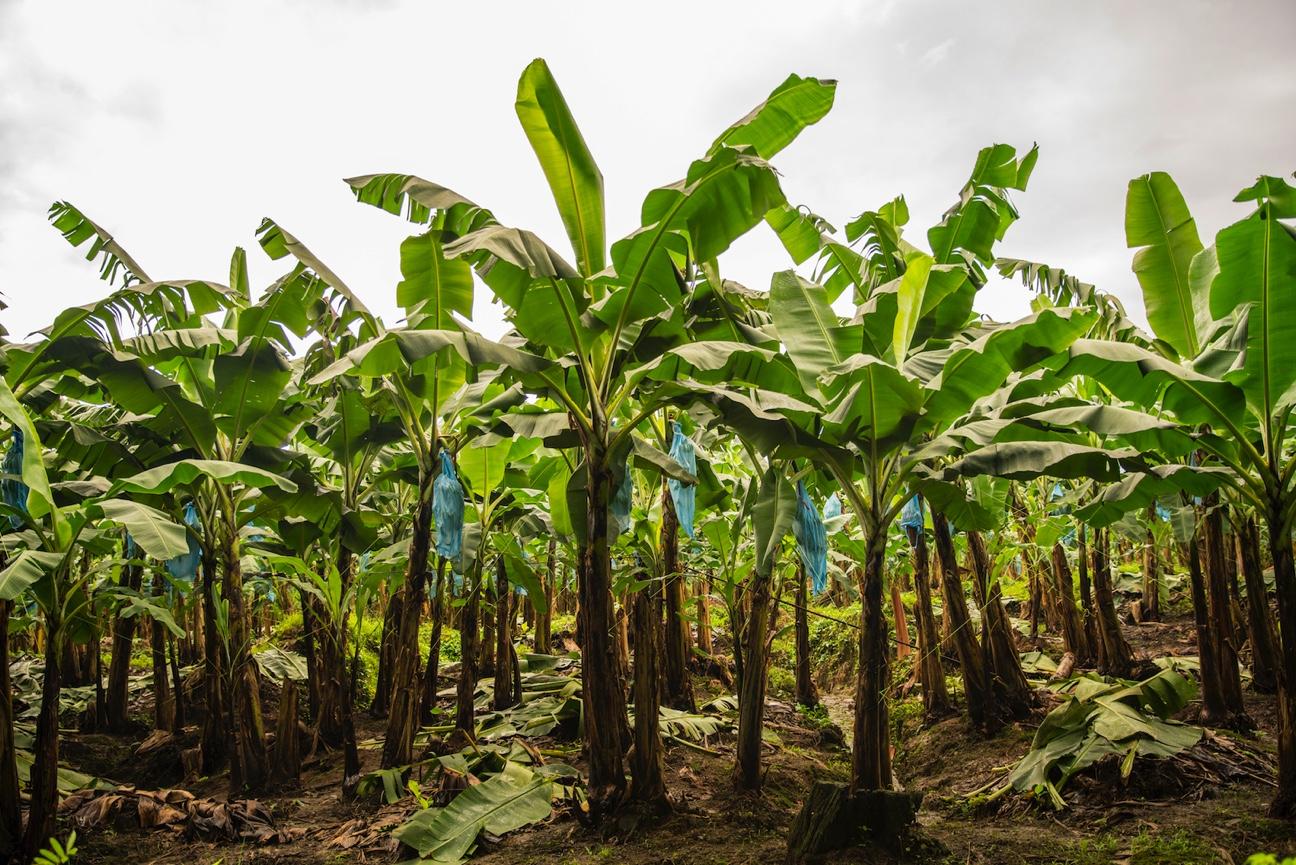
The fashion industry is in a position to make changes that can engender sustainable growth once we recover from this current public health and economic crisis. Materials sourcing is one opportunity, and it’s due for a makeover — especially as petrochemical-based synthetics have grown to 60 percent of clothing material.
Transforming the sourcing and creation of fibers and materials can set a company apart from the crowd and, if done correctly, can help sustain the industry for years to come.
Bleak predictions for fashion in 2020
Even before the COVID-19 outbreak became a full-blown global crisis, McKinsey’s State of Fashion survey reported that executives, thought leaders and pioneers were apprehensive about fashion’s prospects this year. Fashion executives across segments and regions saw growth slowing in 2020. Only 9 percent of respondents to McKinsey's survey said they expect conditions to improve in 2020, compared with 49 percent in 2019.
Among the 10 defining themes McKinsey identified as driving the fashion industry in 2020 are building resilience, putting sustainability first and revolutionizing materials.
“Fashion players need to swap platitudes and promotional noise for action on sustainability measures such as energy consumption, pollution, and waste,” the report reads.
“Despite modest progress, fashion hasn’t yet taken its environmental responsibilities seriously enough. Next year, fashion players need to swap platitudes and promotional noise for meaningful action,” the consultancy said in a video summarizing the research.
At last count, the global textile industry emitted 1.2 billion tons of greenhouse gas emissions a year, a quantity that rivals that of the automobile industry. Pesticides, water use and water pollution are just a few other blights the fashion industry needs to tackle to remain sustainable. That’s not to mention the stubborn presence of child labor and unethical employment in many of its supply chains.
Enter Agraloop, a trademarked regenerative process for creating natural fiber from food crop waste that can be scaled across the globe. The system could also serve as a template for local sourcing as global supply chains are threatened with disruption. And that’s exactly what Agraloop’s creators aim to do.
Decentralizing fashion to support the globe, the industry and farming communities
Circular Systems — the startup that created Agraloop, as well as a host of other waste-transforming technologies — has completed a pilot of its mill in China and says it has plans to launch a fully-localized operation in Belgium. The technology won the H&M Foundation’s 2018 Global Change Award.
While the pilot in China used oilseed hemp food crop waste from Canada and the European Union, the system in Belgium will rely entirely on feedstock from local farms to make garments in Europe. Operations will run on renewable energy from Belgium’s grid, and wastewater effluents will return to local farms in the form of organic soil amendments.
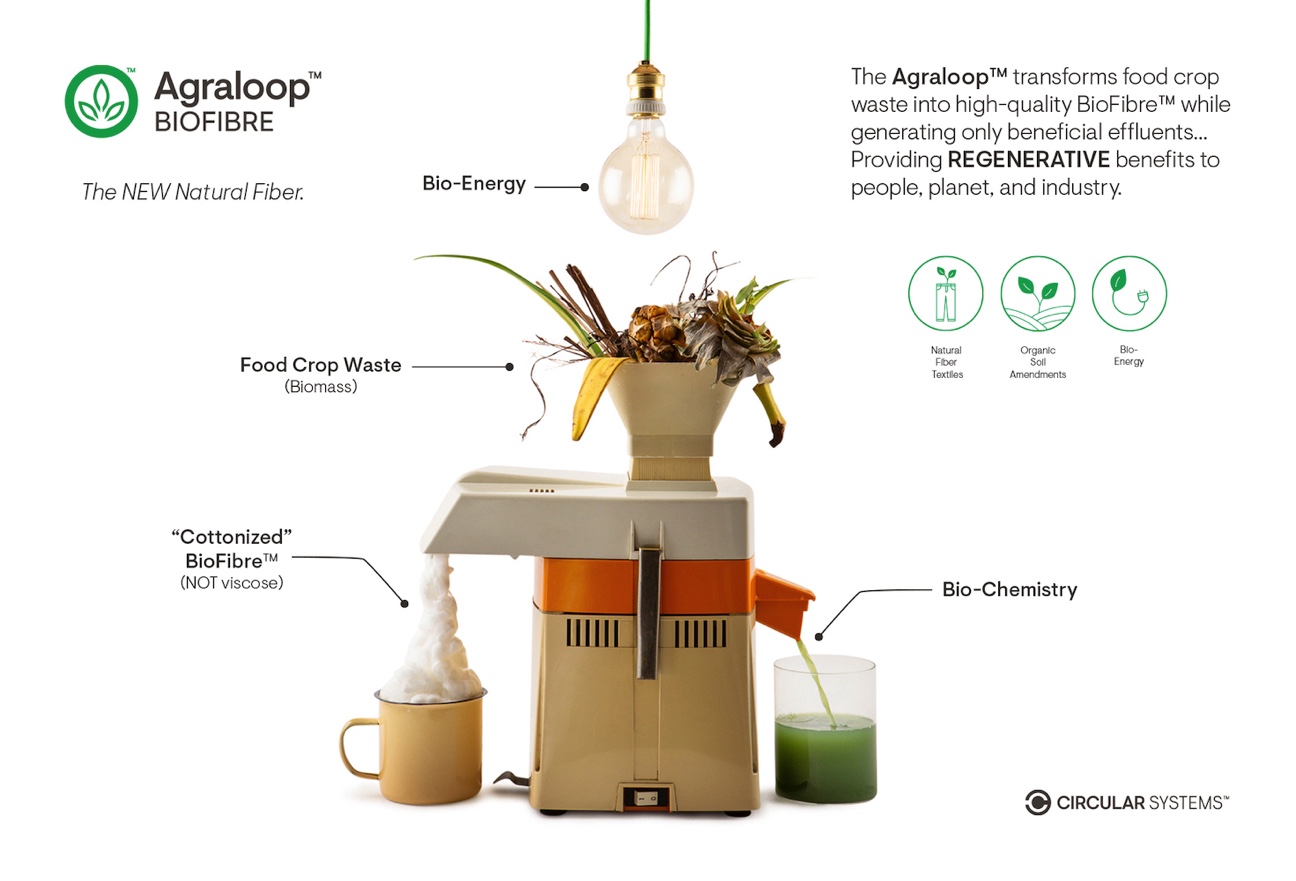
(Image: A quick layperson's description of how the Agraloop system works.)
The power of Agraloop is in its ability to benefit agricultural regions, all while transforming the global fashion industry.
The system is micro-regional, Isaac Nichelson, co-founder and CEO of Circular Systems, told TriplePundit. The mills would serve less than a 150-mile radius and would be fed by three to five pre-processing substations where the materials are first handled and processed.
As Agraloop scales, the Circular Systems team hopes to license the technology and joint venture with regional stakeholders to build and operate the mills, Nichelson said. Circular Systems wants local stakeholders to become controlling shareholders of the technology. “The goal is empowering that local community to be in charge of its own destiny with dignity,” he told us.
Nichelson sees Agraloop bringing income and jobs to communities and fertilizer and support to farmers.
Ecological benefits, from global warming to water
Not only does the company make use of waste; its process also eliminates greenhouse gas emissions normally produced from fiber production, upcycles wastewater and generates organic fertilizer that returns to the farms Agraloop relies on.
That fertilizer helps increase the ability of soils to sequester carbon. Fortifying soil health can be effective in reducing atmospheric greenhouse gases.
On a more technical, but no less important, note, the Agraloop process does not include sodium hydroxide, which textile companies use during the mercerization process that allows fabric fibers to become both dyed and strengthened. Nichelson explained further: “The makers of sodium hydroxide will tell you, ‘What’s to worry about? It’s just salts.’ But unfortunately, these salts are extremely caustic, and they are a disposal problem after water filtration, during fiber extraction and upgrading, and during all dye processing and fabric finishing.”
Agraloop has been able to move away from sodium hydroxide by using its own bio-alkali, which keeps all byproducts organic and nontoxic.
The business case for creating a waste-based natural fiber
The business case for Agraloop is larger than helping apparel companies connect with ecologically-minded consumers — though that is a significant segment of the population. Agraloop can supply natural fiber in a landscape where there’s not enough cotton to meet global fashion needs, Nichelson said.
“We’ve hit peak cotton," he told us. "The market needs a new, scalable and cost-effective natural fiber.” Agraloop, which uses oil-seed hemp, oil-seed flax, pineapple leaves, banana trees, cane bagasse and rice straw, can fill that niche.
The technology is seeing support from major brands, including H&M Group and Converse. H&M said, as of now, it will launch products using Agraloop-based material during the 2020 holiday season. Converse is developing Agraloop-based apparel and flagship products.
Once Circular Systems tests its facility in Belgium, the company’s driving goal will be to replicate Agraloop around the world as quickly as possible. Nichelson says the team is building with precision so that it can scale successfully. In the meantime, Agraloop is seed fundraising to help expand and optimize the commercial production that has already started.
Image credits: Circular Systems
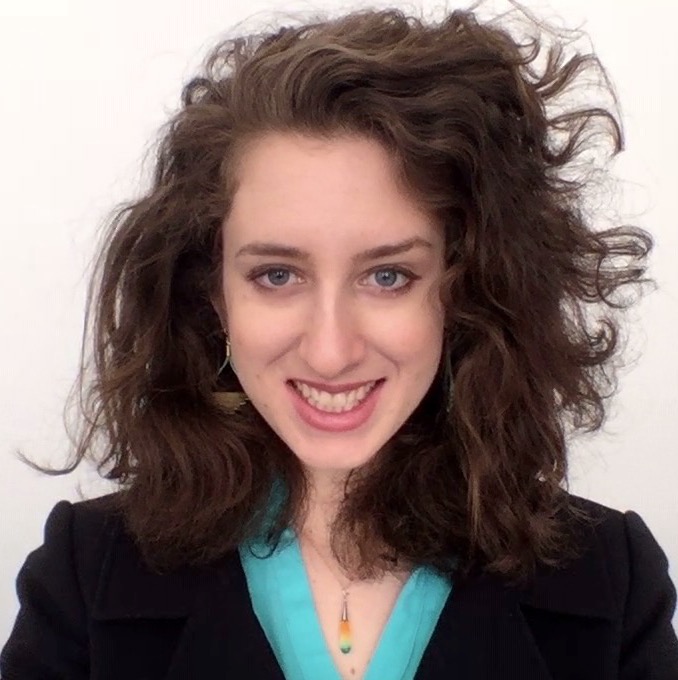
Roya Sabri is a writer and graphic designer based in Illinois. She writes about the circular economy, advancements in CSR, the environment and equity. As a freelancer, she has worked on communications for nonprofits and multinational organizations. Find her on LinkedIn.