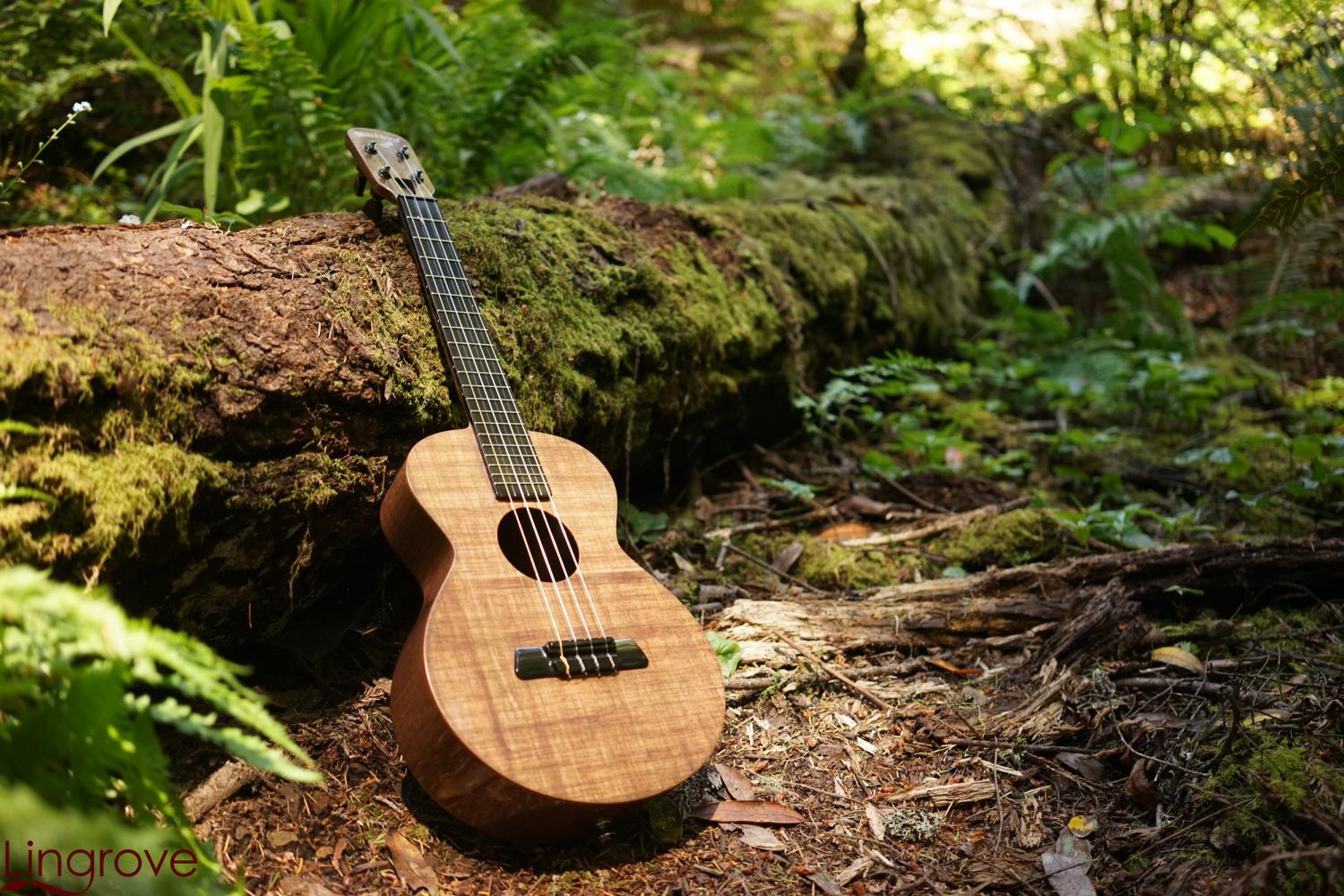
In spite of efforts by organizations like the Forest Stewardship Council (FSC) to increase sustainably harvested wood, deforestation continues to be a major problem worldwide, and it is getting worse. Annually, development, from farms to building tracts, has resulted in the destruction of more than 32 million acres of forests.
This loss of forests contributes significantly to climate change: the FSC says deforestation causes 20 percent of total greenhouse gas emissions--let alone damaging lands in which wildlife and people that rely on forests live.
Drastic action must be taken and the XPRIZE’s Future of Forests Impact Roadmap identifies 10 breakthroughs needed to slow or stop the destruction. First is “super-wood,' defined as a “sustainably-produced alternative for wood” that has similar properties, thus shifting the reliance on virgin wood away from natural forests.
Barking up the right tree
Lingrove, a start-up in San Francisco, is well on its way to achieving this breakthrough with its product called Ekoa. The biomaterial was originally developed for Blackbird Guitars as a tonewood (wood most suitable for acoustic instruments) replacer and its name is derived from koa, an exotic Hawaiian wood used for ukuleles and guitars. In 2014, Blackbird Guitar's Clara ukulele won JEC's Composite Innovation Award. Its Savoy guitar also received a very positive review from a music publication in 2018 - so clearly, Lingrove’s product can compete on both durability and quality.
Ekoa combines Canada-grown flax (linen) fiber with a cashew-based bioresin. Flax is a fast growing and hardy grass-like plant that can survive drought and poor soil conditions. The flax fibers help provide the natural grain look of the product. More importantly, the fibers are considered carbon-negative because they sequester carbon during the growth cycle, which isn’t released during processing of the composite material.
Third-party testing results that Lingrove has disclosed make the point that Ekoa could perform even better than wood and other competing materials as follows:
-
Three times the vibration damping of glass
-
30 percent lighter than carbon fiber
-
Stiffer than aerospace-grade fiberglass
-
Stable over a wide temperature range
-
Flame and humidity resistant
Its cost, according to Lingrove, is much lower than premium wood and similar to aerospace-grade fiberglass.
Conventional processing combined with sustainability
Flax fibers are combined with resins in a continuous process. Conventional composites processing methods are used including vacuum bagging, compression molding, wet layup, autoclave and bladder molding. Specifications such as color, moisture, ultraviolet and fire resistance can be designed into the raw fibers or resin before the composites process. Specialty backings can also be introduced during this process to add thickness or other functional benefits, such as acoustic performance. The finished material is available as rollstock.
In late 2017, Lingrove launched Ekoa TP, which uses a lignin-based thermoplastic for industrial-scale fast processing and recyclability. The look and feel of wood is still obtained but with much better sustainability. After the product is cut and layered in a mold, it’s easily compression molded into three-dimensional composite shapes for interior and furniture applications.
Ekoa is now being produced at a continuous sheet production capacity of 2,500 feet per day, with a goal to scale up to 5,000 feet per day. In the future, Lingrove is looking at incorporating more agricultural waste, more bio-plastics and more post-industrial, post-consumer recycled resins in its formulation.
Besides Blackbird Guitar, Steelcase is a major customer. Lingrove also has projects underway with large companies in interiors, transportation, sports and some consumer electronics. Some products applicable to the construction market include moldable veneers for furniture and surfaces, and structural panels.
Although Lingrove claims it has no direct competitors, it does compete with the same applications made from high-energy consuming materials such as fiberglass, carbon fiber, polyvinyl chloride and vinyl, reconstituted wood and even some metals.
Not out of the deforestation woods yet
Despite no direct competitors, Lingrove still has marketing challenges to overcome. “Disrupting the materials landscape is easier said than done,” says Elaine Chow, a co-founder of the company and Lingrove’s director of business development. “There are a lot of rules and regulations around what materials can be used and where.”
She also explains the many reasons why bio-based and upcycled materials have been slow to gain traction. These factors include higher cost, smaller scale, lower performance and a less desirable aesthetic. “At Lingrove, we want to reframe what bio-based and recycled materials look, feel and work like,” says Chow. “We believe Ekoa sits at the intersection of ecology, desirability, scale and high performance.”
Image credit: Lingrove
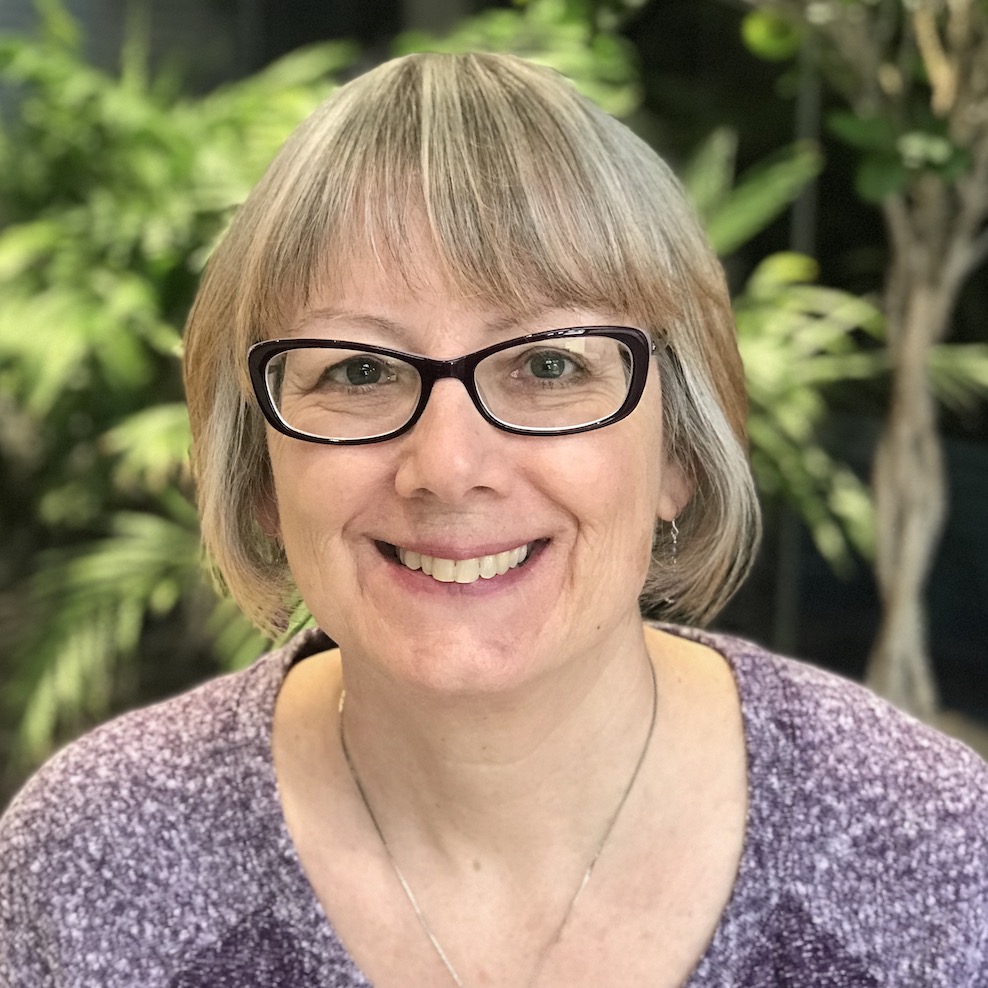
Laurel has extensive experience writing about energy efficiency, clean energy, sustainability and green building. She was formerly Senior Energy Content Specialist for a digital marketing firm serving the utilities industry where she generated story ideas and wrote content for several e-newsletters. Laurel is also a member of the Ohio chapter of the U.S. Green Building Council and participates on several committees for the Central Ohio region.