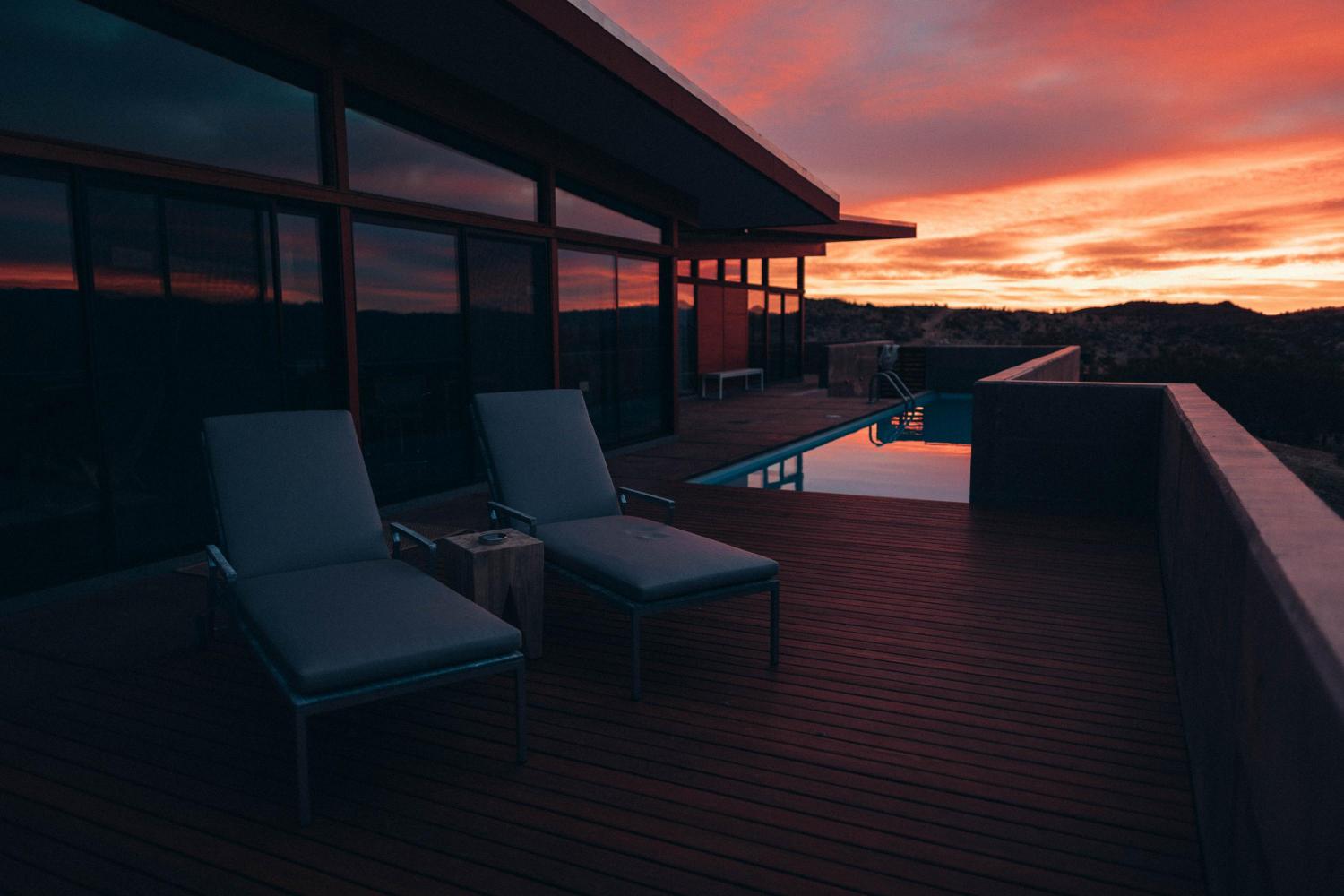
The picnic table at which you’re enjoying your summer BBQ may have been a plastic glove, shoe cover or chemical container involved in the manufacturing of biopharmaceuticals in its past life.
Thanks to a partnership between global biopharmaceutical products supplier MilliporeSigma and specialty waste management company Triumvirate Environmental, a portion of single-use biopharma plastic scrap is now being diverted from landfills and upcyled into salable products.
30,000 tons of biopharma plastic waste are landfilled or burned annually
Globally, an estimated 30,000 tons of biopharma single-use products are landfilled or burned each year. One reason is that recycling biopharma plastics isn’t as simple as recycling ordinary plastic. The plastic items used in the production of pharmaceuticals – such as bioreactor bags, tubing, filtration systems and chemical containers -- often contain a combination of materials such as silicon, polyethylene and polypropylene. When combined, these materials are difficult to separate.
Despite the difficulty, MilliporeSigma, which manufactures such items, wasn’t deterred. The company is part of German-based Merck KGaA, which reports a commitment to using its “expertise to improve the sustainability balance” of its products, as well as to developing new solutions that support its customers in reducing their environmental impact.
As part of its commitment, MilliporeSigma piloted a recycling program where staff manually cut up items to separate the different plastics before they were shipped to a reclaimer.
Jacqueline Ignacio, global manager of customer sustainability solutions for MilliporeSigma, recently explained to Plastics Recycling Update that the approach was neither safe nor cost-effective, and it couldn’t provide the volumes the recycling vendor needed.
“Obviously, if we were to roll out a program like that, the cost of that would have outweighed the benefits and we would not have been able to maintain it,” Ignacio said.
Persistence pays off
But MilliporeSigma and Ignacio didn’t give up. They found a willing partner in 2015 with Triumvirate Environmental, a Massachusetts-based company that provides collection and disposal of dangerous chemicals and bio-hazardous waste. Together, they developed the Biopharma Recycling Program, which finally found an efficient way to fully recycle single-use and disposable single-use biopharma plastic products without segregation or disassembly.
This is how it works: MilliporeSigma’s customers in the Eastern half of the United States contract with Triumvirate to have their scrap plastic materials collected. Triumvirate transports the plastics to its Pennsylvania facility where they grind, shred and separate the plastics before blending them into a homogenous mix. If any plastics have been in contact with biohazardous waste, they also sterilize them.
Triumvirate employees then mold the mix into plastic lumber, speed bumps and shipping palettes. Voila! Closed-loop.
Triumvirate sells the products under its BestPLUS brand. Available in multiple sizes and colors, the lumber is used in landscaping, picnic tables and other applications. Triumvirate also sells the plastic shipping pallets to biopharmaceutical manufacturers to reduce the risk of contamination brought into facilities by wooden pallets.
To date, MilliporeSigma is the only company that has partnered with a waste management company to address the unique and challenging disposal issues that come with single-use products. In recognition of its efforts, in 2018, it was awarded a Pharma Innovation Award by Pharmaceutical Manufacturing magazine.
All eyes on the West Coast
Due to the cost and environmental impact of transport, Triumvirate currently only collects plastics from biopharmaceutical manufacturers east of the Mississippi River. Not a bad place to start, however, given that East Coast biopharmaceutical drug sites generate an estimated 4,500 tons per year of single-use plastics.
Ultimately, MilliporeSigma and Triumvirate would like to find a way to serve manufacturers on the West Coast as well.
“Hopefully, in the next year we’ll have a way to at least collect and condense the shipments from the West Coast to the east so that it makes more sense from a greenhouse gas footprint – carbon footprint – as well as the transportation costs,” Ignacio said during her interview with Plastics Recycling Update.
As biopharmaceutical manufacturing continues to increase and with it the use of single-use plastics, MilliporeSigma’s and Triumvirate’s Biopharma Recycling Program will continue to do its part to divert the waste from landfills and incinerators. Hopefully others will join them.
Image credit: Roberto Nickson/Unsplash
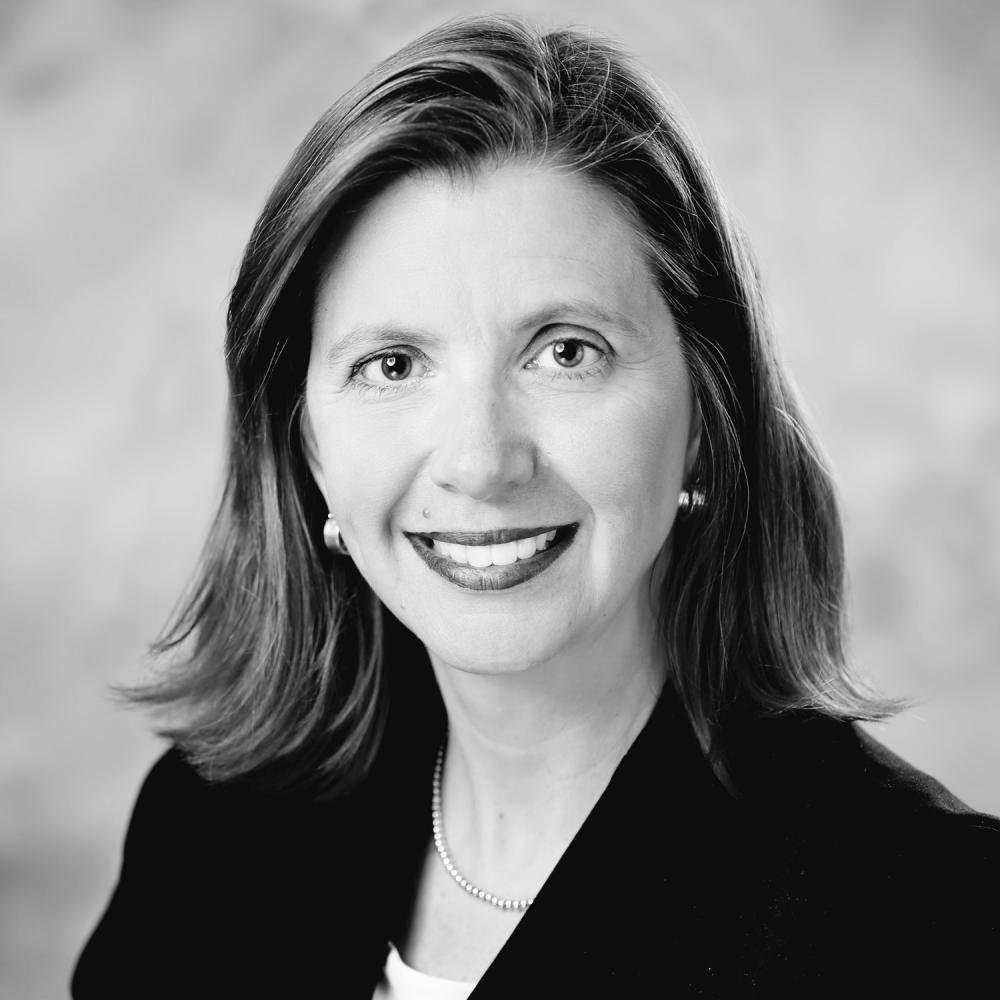
Maggie Kohn is excited to be a contributor to Triple Pundit to illustrate how business can achieve positive change in the world while supporting long-term growth. Maggie worked for more than 20 years at the biopharma giant Merck & Co., Inc., leading corporate responsibility and social business initiatives. She currently writes, speaks and consults on corporate responsibility and social impact when she is not busy fostering kittens for her local animal shelter. Click here to learn more.