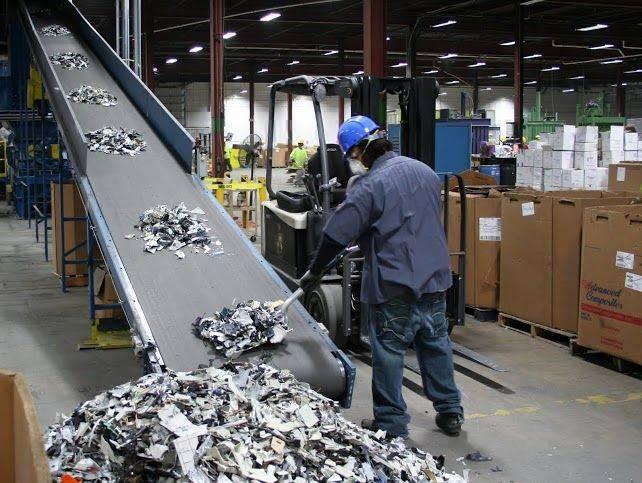
By Dawn Grimes
Every year the Consumer Product Safety Commission orders recalls of thousands of goods to protect consumers from a host of dangers ranging from toxicity to flammability to faulty construction and packaging, among others. Despite significant investment of time, energy, and money, recall can happen to the best of manufacturers.
For companies facing a product recall, here’s some advice based on our experience as a social enterprise and destination handler with a track record of processing millions of pounds in recalled electronic consumer goods at our Indianapolis-based facility.
What can manufacturers do to avoid a recall?
As an “end-of-life” electronics processor, it’s our job to break down, sort, and separate retiring IT and electronics products to create the cleanest possible streams of the sub-materials that were used to create them, mostly metals and plastics. As a result, we’ve become intimately familiar with the bits and pieces of these de-constructed consumer products in order to sell them to refiners and smelters.From our perspective, brand manufacturers who really understand the properties of the raw materials they’re using will reduce the odds of their finished goods ending up at facilities like ours. It’s surprising how often raw materials are at the heart of a recall: using non-tempered glass when tempered was needed, using a polypropylene plastic instead of an acrylic or nylon, or using raw materials that are contaminated or not fire-resistant. Working with supply chain experts like Mintec or Source Intelligence can help R&D eliminate any number of problems from contamination to mineral conflict that that can result in recall, regulatory failures, or non-compliance.
When products are recalled, what happens to them?
Savvy manufacturers can ease the burden of a recall by thinking ahead. We recommend building a relationship with a reverse logistics handler before a recall notice ever arrives. Having an established relationship with an organization with expertise in getting product off shelves, and out of distribution centers and the consumer stream has great potential for saving product-makers time and money in case of recall. Organizations like Stericycle, Inmar, and U.S. Ecology are well-versed in the consumer protection safety and environmental regulations that dictate recalls.At RecycleForce we receive electronics product recalls by the semi. Consumer packaged electronic goods typically come to us from distribution centers, warehouses, or retail shelves. Here’s what happens once the truck backs up to our loading dock:
- De-Package:The first thing we do is manual de-pack. That is, we take goods out of their consumer packaging to separate and sort cardboard, paper inserts, film plastic, Styrofoam, and blister packs. Anyone who has opened a new CD would know this can be one of the most time-consuming aspects of the process.
- Manual de-manufacture: Our employees take products apart with hand tools, then sort and separate the various components for shredding or baling.
- Mechanized destruction: Even though products are destroyed during the manual de-manufacture process, the government may require (or some customers prefer) that destruction results in bits and pieces. Therefore, after shredding we run pieces through a mechanical separator that sorts plastic from metals.
- Downstream processing: We generate 81 different sub-material products, primarily metals and plastic, that we downstream to refiners who process them for use in new products.
Making the best of a bad situation
Environmental good: There’s an environmental halo that can be claimed by even the worst of recalls. Instead of disposal by landfill, many of our customers recognize there’s an opportunity to commit to sustainability and to the environment. Most of the product recall processing we’ve handled have been at a 95 percent+ recycle rate and in many case we achieve 100 percent.Social Good: At RecycleForce we employ people recently released from correctional institutions. We provide an opportunity for more than 300 people each year to get traction through industry, classroom, and job skills training. We also help with transitional services like assisting with setting up an employee’s child support, helping them get a driver’s license, or connecting them with mentors, housing agencies, or other basic needs support organizations.
Without these foundational elements, the rate of return to the criminal justice system is incredibly high. Historically, here in Indianapolis, about half of those released from prison return within three years. The majority return on a technical rules violation, often involving unpaid fees or restitution. At RecycleForce 60% of the people we serve are placed in full-time employment—with a return-to-prison rate about a third of the national average.
We live in a throw-away culture. Society throws away electronics and it throws away people, too. At RecycleForce we reclaim the value of recalled electronics and we help people reclaim the value of their own lives.
Dawn Grimes is the VP Business and Enterprise Development at RecycleForce. RecycleForce is an Indianapolis based social enterprise – a business with a social mission – offering comprehensive and innovative electronic recycling services while providing life-changing workforce training to formerly incarcerated individuals.
TriplePundit has published articles from over 1000 contributors. If you'd like to be a guest author, please get in touch!