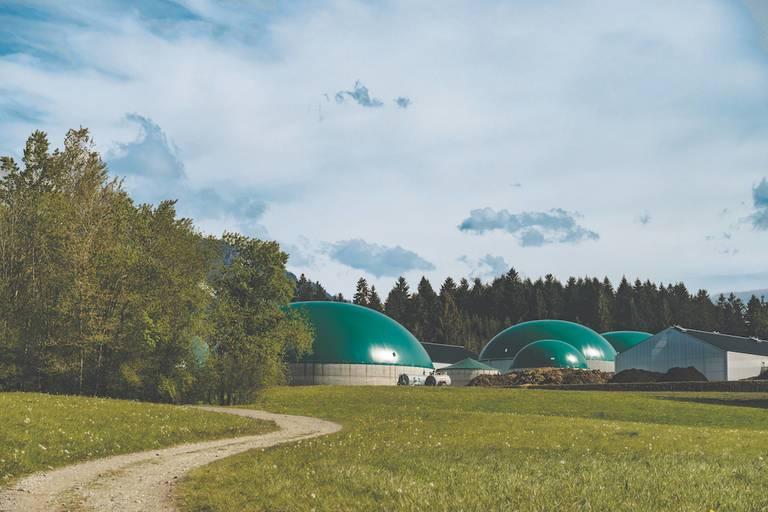
Last week, spring water giant Evian unveiled a carbon-neutral bottling site in the French alps. The plant is not new per se, but rather the culmination of a six-year effort to modernize a facility Evian has called home since 1965.
Unlike most bottled waters on the North American market, Evian comes from a single underground spring. Water flows nearly five miles through the earth from a catchment area on the plateau of Gavot in the French Alps to the bottling plant. The company says this 15-year journey through sand and rock gives Evian water a unique mineral composition. But it also means the water is constantly flowing and the plant had to remain operational while modifications took place.
"We've not lost a drop of water in the process," Stéphane Dupays, director of the Evian bottling site, said of the plant upgrade.
The need to maintain 24/7 operations while under construction presented a distinct set of challenges for plant employees. And their future became even more uncertain thanks to a trend that's sweeping the manufacturing sector: automation.
While globalization and access to cheap labor are often blamed for lost manufacturing jobs, research indicates that the rise of robots poses an even greater threat. In the U.S., for example, it took 25 jobs to generate $1 million in annual manufacturing output in 1980. Today, thanks to automated assembly lines, it takes only five jobs.
Here's where Evian's story stands out. Its modernized factory includes multiple automation upgrades, but rather than issuing sweeping layoffs, the company was actually able to bring on new workers. How? By doing something other companies often claim to do, but far too often let fall by the wayside.
Preparing employees for the future
Between 2011 and 2020, Evian will spend more than US$335 million on upgrades to its bottling plant. Included in that total is a broad-sweeping retraining initiative designed to empower employees for tomorrow's workplace and ensure they have a spot at the new factory.
"Around 600 out of 1,200 jobs have been modified," Véronique Penchienati, president of Evian, told TriplePundit after the plant opening.
Rather than hire new people for new tasks, the company offered a collective 30,000 hours of training to retain its current workforce.
Managers held weekly working groups to discuss changes at each level of the assembly line, and employees learned new skills to adapt to these changes. Former forklift drivers, for example, were transitioned to technician roles and trained to remotely operate automated shuttles. At the time of the plant's opening, not only did Evian maintain its team, but it also added 200 new jobs.
"You cannot have this type of transformation — without stopping the factory, with a lot of impact on the jobs people are doing and will do in the future — without having a fully collaborative approach that includes all employees," Penchienati told 3p. "Training was one of the key levers of success." For their part, employees were receptive to the change, and the company won major buy-in from the unions representing them.
Unlike in the U.S., all French factory workers are represented by a labor union. And if a company wants to make a change to its operations that affects employees, it has to get the union's approval first. Evian had 28 consultations with the local union during its six-year construction project, all of which came back with a favorable result.
"It really shows what you can achieve when the people are part of the project," Penchienati told 3p. "It was not a project of the plant director or the boss, but it was a project of all of the employees."
Building on community partnership
More than 90 local companies contracted with Evian to complete the plant remodel, a milestone that builds on a longstanding relationship with the local community. For decades, the company has worked with the Alpine town that bears its namesake, Évian-les-Bains, to preserve its water source and catchment area.
Standing on a picturesque plateau surrounded by mountains, Dupays spoke of the company's people-first mindset. "One approach to preserving the watershed would be to buy everything, but we didn't want to to do that," he said simply.
Instead of gobbling up land, Evian spearheaded a public-private partnership with 13 municipalities near the catchment area. Since 1992, the partnership represented a collaboration between the villages around Évian-les-Bains to protect local ecosystems -- and thereby Evian's product, spring water -- through sustainable agriculture.
The effort came to a peak last year with the roll-out of a project that converts waste from local dairy farms into renewable biogas. Around 70 percent of the region's farmers agreed to send their manure to the Terragr’Eau methanizer, which now processes 40,000 tons of material annually and is the largest of its kind in France.
The result is a watershed free of runoff, a no-cost organic fertilizer for local farmers and enough renewable energy to power 1,200 homes, equal to the annual gas consumption of Evian's bottling site.
Penchienati said people-focused efforts like these speak to Evian's history and that of its parent company, French multinational food products company Danone. "Antoine Riboud [the founder of Danone] was convinced that you cannot split the economic part and the social part of a company," she told 3p. "Everything is combined together, and that’s the only way to do business. You need to involve everyone."
"It's all about the people," Dupays agreed. "The employees and the community feel ownership over the company because they are included."
Image credits: Evian
Editor's Note: Travel and accommodations to the French alps were provided by Evian. Neither the author nor TriplePundit were required to write about the experience.
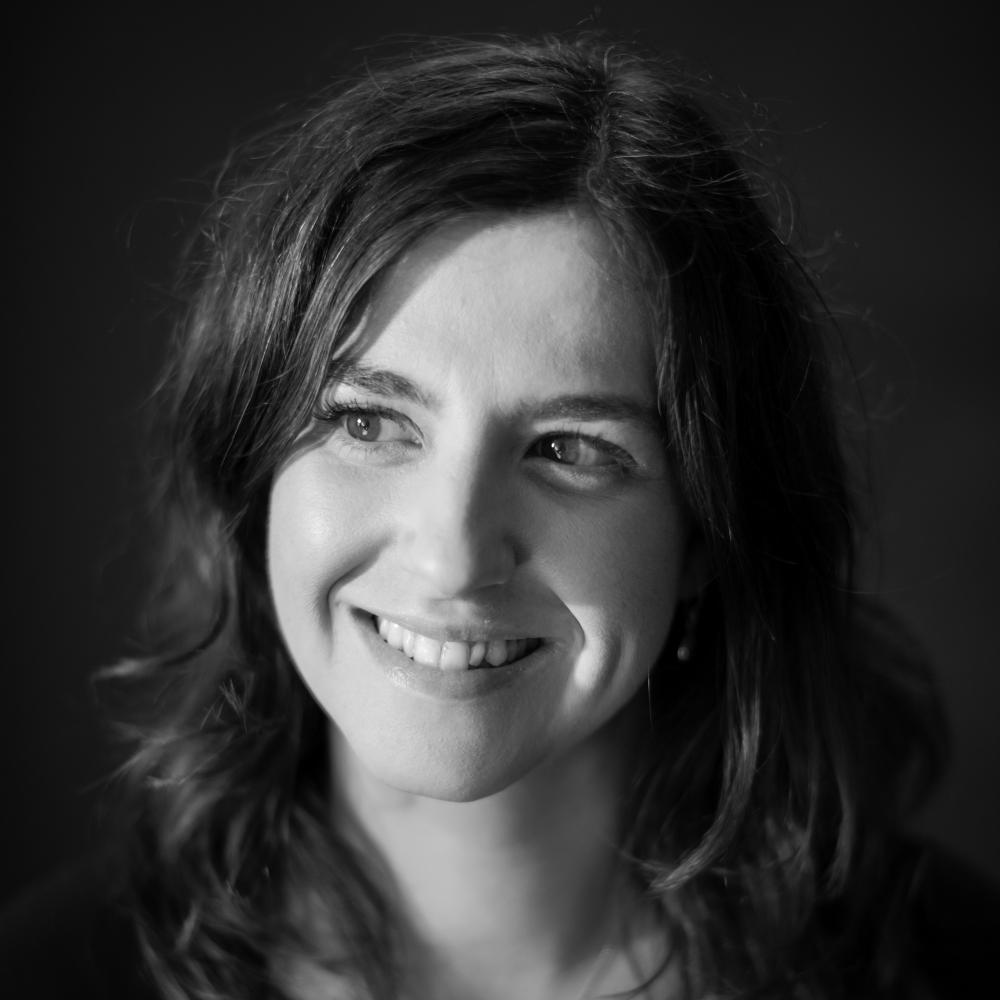
Mary has reported on sustainability and social impact for over a decade and now serves as executive editor of TriplePundit. She is also the general manager of TriplePundit's Brand Studio, which has worked with dozens of organizations on sustainability storytelling, and VP of content for TriplePundit's parent company 3BL.