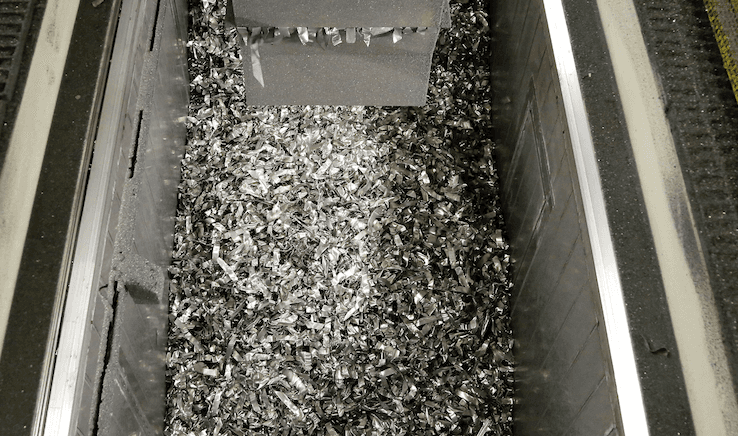
Automakers, especially the American Big Three, are longtime recycling leaders. After all, those large sheets of metal, particularly the steel that comprises a car’s body, are easy pickings.
General Motors, for example, has said in the past that it generates $1 billion in revenues annually from recycling. In recent months, the company partnered with its peers, as well as NGOs, to boost its waste diversion efforts.
Nevertheless, there is always room for improvement on waste diversion. As automobile designers and engineers consider approaches to creating cars that are lighter and more fuel-efficient, new materials find their way into newer models of cars. This is particularly true of aluminum, more of which is finding its way in cars for both its durability and reduced weight.
In the case of Ford Motor Co., the recent adoption of more aluminum in those F-150 pickups reduced their weight by as much as 700 pounds. But the flip side is that new materials throw a wrench into companies’ sustainability and waste management plans. The effort is worth it, however, as using recycling aluminum is 95 percent more energy efficient than refining raw aluminum from bauxite.
Three Ford plants benefit from closed-loop recycling systems, allowing the company to recycle and additional 5 million pounds of aluminum a week. Not only have these factories witnessed a significant decrease in waste, but they benefit from increased energy savings as well.
The result is the accumulation of high-strength and military-grade aluminum alloy each month that can be repurposed to build the equivalent of 51 commercial jets, or over 37,000 of Ford’s F-series truck bodies – a huge spike in aluminum recycling over previous years, the company said this week.
Chip Conrad, a Ford stamping engineer, led the design of these updated recycling systems. Now operating at Ford’s Dearborn Stamping, Kentucky Truck in Louisville and its Buffalo, New York Stamping factories, the systems present a dizzying tangle of vacuum motors and tubes. After various parts are cut into shape, the scraps, which are about the size of a dollar bill, are vacuumed into the pipes, which stretch for miles across these factories.
These pipes are necessary as different sections of a car -- such as fenders, doors or smaller parts -- require various grades of aluminum. Therefore, in addition to these long and winding tubes, computer controls directs different grades of alloys to four separate semi-trucks, which then haul the scrap aluminum to a reprocessing plant so it can be smelted and the aluminum stamping and fabrication process can launch all over again.
Ford’s sustainability team says the system is crucial for the company to meet its long-term sustainability and greenhouse gas emissions reduction targets.
Prior to the new systems Conrad and his team implemented at these three plants, Ford previously reported it was able to conserve enough aluminum to make new bodies for 30,000 F-150 trucks. The redesign of these three factories’ systems alone account for a 23 percent increase in the company’s total aluminum recycling.
While such improvements in recycling allows such companies as Ford to show stakeholders their sustainability chops, the conservation of materials such as aluminum is largely driven by cold hard numbers. In previous years, Ford said that for every F-150 that had rolled off its assembly lines, approximately $300 worth of aluminum scrap were left behind on the shop floor. Considering the company’s claims that its F-Series has been the highest selling truck in America for four decades, that is a lot of energy, metal and cash that Ford had been leaving behind before this latest recycling innovation.
Image credit: Ford Motor Co.
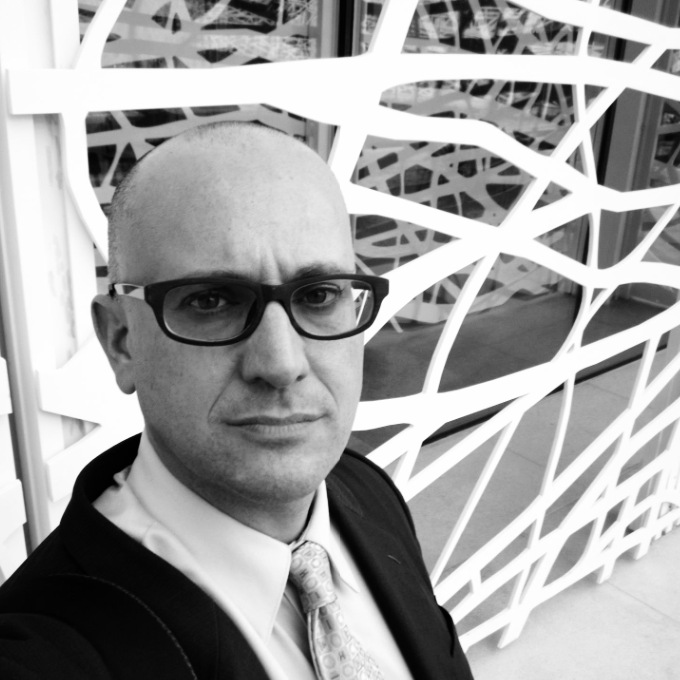
Leon Kaye has written for 3p since 2010 and become executive editor in 2018. His previous work includes writing for the Guardian as well as other online and print publications. In addition, he's worked in sales executive roles within technology and financial research companies, as well as for a public relations firm, for which he consulted with one of the globe’s leading sustainability initiatives. Currently living in Central California, he’s traveled to 70-plus countries and has lived and worked in South Korea, the United Arab Emirates and Uruguay.
Leon’s an alum of Fresno State, the University of Maryland, Baltimore County and the University of Southern California's Marshall Business School. He enjoys traveling abroad as well as exploring California’s Central Coast and the Sierra Nevadas.