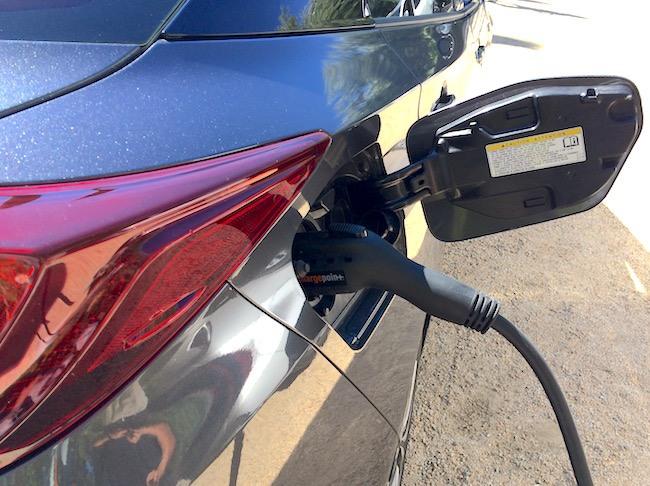
Lithium-ion batteries are still king in the energy storage market, but their shortcomings are holding back the transition to electric vehicles. One main problem is cost. Li-ion battery packs are expensive, and they push up the price of an EV. Their function as an energy storage unit also means they take up a lot of space, and their weight is a drag on efficiency.
The good news is that Li-ion batteries are constantly being improved. In one of the latest developments, a Columbia Engineering researcher tweaked the manufacturing process with the common plastic PMMA. The result is a 10 to 30 percent jump in energy density, which translates into a smaller, lighter and less expensive energy storage product.
The Li-ion energy storage hiccup
The new development zeroes-in on a hiccup that results from the conventional Li-ion manufacturing process. The problem comes up after the battery is completed, when it is charged for the very first time.
As described by Columbia researchers, part of the electrolyte transitions from a liquid to a solid during the first charge, and that solid adheres onto one of the electrodes. That transition can reduce the energy of a Li-ion battery from 5 to 20 percent. That lowers the capacity of the battery and can interfere with its lifespan, too.
(For those of you new to the topic, the electrodes are the parts of the battery that receive and discharge an electrical current. The electrolyte is the part that stores the charge.)
The numbers are even higher for more sophisticated, high-efficiency Li-ion batteries:
"The loss is approximately 10 percent for state-of-the-art negative electrodes, but can reach as high as 20 to 30 percent for next-generation negative electrodes with high capacity, such as silicon, because these materials have large volume expansion and high surface area."
One way to work around the problem is to add lithium-saturated materials during the manufacturing process, to counterbalance the lithium "lost" during the first charge.
However, lithium is unstable in ambient air. The conventional process requires a moisture-free manufacturing environment, which adds significant costs.
Plastic to the rescue
Columbia Engineering researcher Yuan Yang tackled the problem by developing a tightly focused way to protect lithium-based electrodes during the manufacturing process, eliminating the need to create a moisture-free environment in the factory. Here's the rundown from Columbia:
"In these electrodes, he protected the lithium with a layer of the polymer PMMA to prevent lithium from reacting with air and moisture, and then coated the PMMA with such active materials as artificial graphite or silicon nanoparticles."
Once the electrode comes into contact with the electrolyte, the PMMA dissolves away. There is no contact with ambient air during the entire process.
The new process is not ready for commercial development -- yet. The next steps involve refining the process to reduce the thickness of the PMMA coating, and to ramp the steps into high-volume mode.
You can get all the details from the study, published online at the journal Nano Letters.
Energy storage and EVs
Getting back to the EV market, if Yang's new electrode makes it into the market, auto manufacturers have more flexibility. With a higher-capacity battery, an electric vehicle could have greater range without increasing the size and weight of the battery pack.
Another option is to shrink the size of the battery pack without sacrificing range.
That could bring about some interesting options for auto manufacturers like Toyota. Last month I went on a "ride and drive" with Toyota on behalf of TriplePundit, and the company emphasized the extent to which plug-in hybrid EVs can satisfy the needs of most drivers, even with a relatively low driving range.
Toyota executives explained that the goal for the company's signature plug-in hybrid EV, the Prius, is to keep the battery pack relatively small in order to keep the price of the vehicle within an affordable range. (The company is dedicated to increasing fuel efficiency, too.)
Even with a small battery pack, the 2017 Prius can operate in full EV mode for the daily commute of up to 80 percent of U.S. drivers (the high end combines home and workplace charging).
Introducing a smaller energy storage unit with the same range would provide Toyota with an opportunity to keep pushing down the price of a Prius.
That would make the car even more affordable, and bring the zero-emission driving experience to more of the motoring public.
A smaller battery pack would also take up less space. That could provide hybrid manufacturers with an opportunity to introduce new design options and other aesthetic features that attract drivers to the EV experience.
Photo: 2017 Toyota plug-in Prius hybrid EV by Tina Casey.
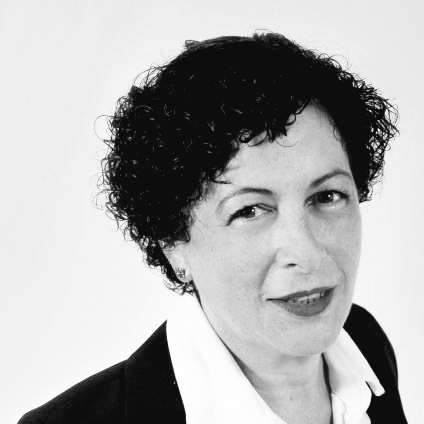
Tina writes frequently for TriplePundit and other websites, with a focus on military, government and corporate sustainability, clean tech research and emerging energy technologies. She is a former Deputy Director of Public Affairs of the New York City Department of Environmental Protection, and author of books and articles on recycling and other conservation themes.