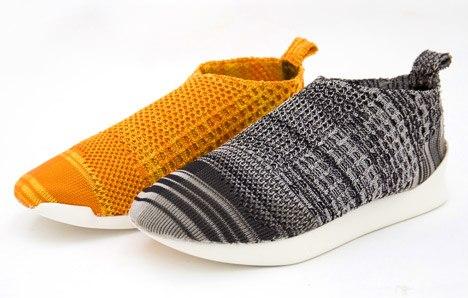
We love our athletic shoes, sneakers, tennis shoes or whatever your preference is in describing them. Long ago barely functional and, quite frankly, dowdy and frumpy sneakers have evolved into sophisticated products. Companies from Nike to Brooks to Adidias have turned the athletic shoe industry into what is now an approximate $80 billion dollar market. And why wouldn’t we wear them? They perform better now than ever, use the latest in cutting-edge in technology, and for those of us who just wear them for looks, they often make for that perfect fashion accessory.
But there is a downside to the ongoing surge in athletic shoe sales when it comes to the environmental front. Depending on the model, the average athletic shoe can use up to 65 different parts and incorporate as many as 360 different manufacturing processes — which are why the athletic-shoe industry’s supply chain is almost as long-winded and complex as that of electronic gadgets. For the carbon bean counters, the complicated manufacturing journey athletic shoes endure account for their high carbon footprint. More companies, such as Nike, have acknowledged the products’ environmental footprint and are taking steps to address these challenges. Nevertheless, the industry has a long ways to go.
Enter Ammo Liao, a designer based in the U.K., who has re-imagined the sneaker, and in doing so, created a shoe that looks pretty sweet as well.
Liao has designed the Bio-Knit shoe, which eschews the multi-faceted approach taken toward the manufacturing of sneakers as he only uses one material. For both the upper and the sole, Liao uses the exact same composite. The upper is derived from a knitted material, which avoids using bolts of fabric, much of which goes to waste on the cutting-room floor. The knit is heated, pressed and engraved by laser, all of which contributes to the material's strength. Liao created the sole using a 3-D printer. The result is a shoe that can be recycled along with plastic water bottles once it is no longer needed. Liao claims this process, which he calls “textile biomimicry,” can be applied to other products, too, including luggage and bicycle helmets.
The end result is a chic looking product: Unlike another famous one-composite shoe (Crocs), they actually look good. The question, however, is whether his concept can scale and be picked up by any of the large manufacturers in the market.
One reason why the manufacture of athletic shoes has become such a byzantine process is that consumers, and not just professional athletes, demand high performance and are often willing to pay for it. Fast fashion has not helped either, as the large global apparel chains churn out goods as quickly and cheaply as possible. Suppliers are often willing to manufacture quickly and cost-effectively — and often outsource components and functions such as stitching and gluing if it means those orders are met on time.
Nevertheless, Liao has given us a rethink about how we could make shoes — and if his idea can go from project to production and, ideally, recycling -- a transformation of the shoe industry is not impossible.
Image credit: Ammo Liao
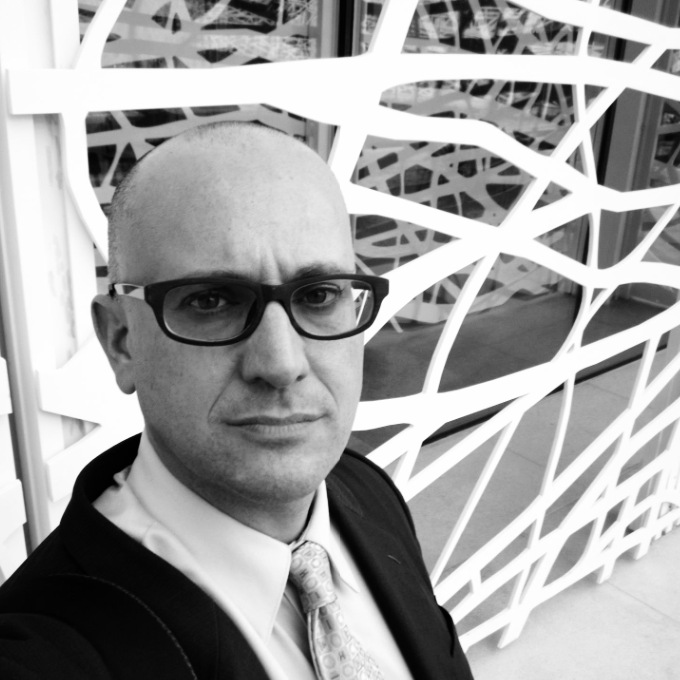
Leon Kaye has written for 3p since 2010 and become executive editor in 2018. His previous work includes writing for the Guardian as well as other online and print publications. In addition, he's worked in sales executive roles within technology and financial research companies, as well as for a public relations firm, for which he consulted with one of the globe’s leading sustainability initiatives. Currently living in Central California, he’s traveled to 70-plus countries and has lived and worked in South Korea, the United Arab Emirates and Uruguay.
Leon’s an alum of Fresno State, the University of Maryland, Baltimore County and the University of Southern California's Marshall Business School. He enjoys traveling abroad as well as exploring California’s Central Coast and the Sierra Nevadas.