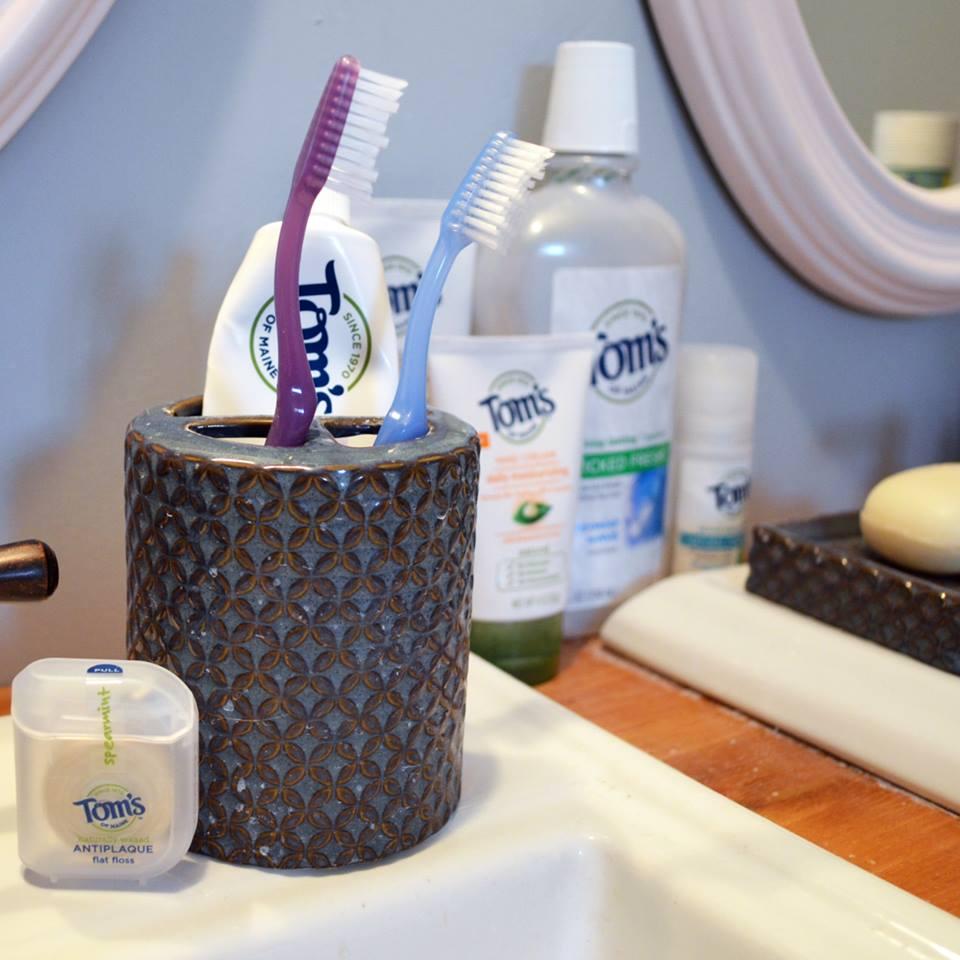
This article is part of a series on “The ROI of Sustainability,” written with the support of MeterHero. MeterHero helps companies and organizations offset their water and energy footprints through consumer engagement. To follow along with the rest of the series, click here.
Water reclamation is playing an increasingly important role in local and regional resource management these days. The threat of drought and dwindling fresh water supplies have forced many communities, businesses and organizations to rely on recycled water, particularly when it comes to serving non-potable needs. In many areas of the U.S. and Canada, golf courses, campgrounds and public parks now use recycled water to maintain their greens. In Southern California, some businesses run their air conditioning units on recovered water, and in Chattanooga, Tennessee, Volkswagen uses reprocessed water to stock its cooling tanks and flush its toilets. Orange County, California, has already taken the preliminary steps of transitioning to potable recycled water as a means of offsetting its three-year drought.
But as one company in Maine discovered, there are other ways that we use water commercially that drive up the ecological price of that resource – methods that aren’t as easy to address as, say, in the agricultural setting where irrigation can be more easily recycled.
“Steam is an important resource at Tom’s of Maine,” explains Susan Dewhirst, PR and goodness programs manager at Tom’s of Maine. The company, which makes natural personal care products such as toothpaste, deodorant and baby lotion, uses scalding-hot steam for everything from heating to cleaning and sanitizing its equipment. And that, just like running water, becomes a valuable, ephemeral resource when it isn’t recycled.
“The trick is to be more efficient with the water we use to limit how much we need,” Dewhirst said.
But how do you do that when you are using something like vapor?
The answer, says the company, is in the very system it uses to clean and sterilize its equipment, which is called “clean in place,” or CIP. The CIP system is designed to clean closed-loop production systems that can’t be taken apart or accessed by hand, such as a sealed piping system. The method began in the 1950s with a clunky system that involved a balance tank, a centrifuge pump and a manual hose fitting (and was still more efficient and easier than the elbow grease that was used prior to that time to clean less efficient equipment).
“We used to channel raw materials through a single pipe into mixing tanks. We had to clean the pipe every time we switched materials,” the company said.
Today, CIP is a state-of-the art digitalized system that is widely used in food and beverage industries. It has also made it possible for companies like Tom’s to ensure that the piping, hoses and other equipment that manufactures sticky substances like toothpaste and lotions are sterile at the end of the production schedule.
Best of all, the system allows the company to reduce its dependence on chemical cleaners and additives, which have the potential to pollute the environment.
Some of today’s CIP systems are built to recycle the water that is converted to steam. The process of heating the water into steam, condensing it back to water and recycling the resource will allow the company to meet its 2020 water conservation goal, which includes reducing its water footprint by almost half of what it used in 2011, Dewhirst said.
“We see the steam recycling system as a critical way to not only save dollars but minimize our overall water footprint,” said Dewhirst, who noted that the ability to recycle the steam means less impact on their energy footprint as well.
The company’s attitude toward water reflects a broader aim to work in concert with the environment, through its reduction of waste, carbon and extraneous packaging.
“Since our founding in 1970, Tom’s of Maine has had a deep respect for natural resources and reducing our footprint wherever possible, including in how we make our products,” said Dewhirst, who noted that the company also employs similar strategies when it comes to waste and fuel usage. “These are commitments we are continuously focused on and are always searching for new solutions. We saw an opportunity to be more efficient with the water we are using, and to think more broadly about recycling.”
Asked what advice she might have for other companies looking to reduce their footprint, Dewhirst said that tracking the company’s water and energy usage against long-term goals is essential.
“External energy audits are a great way to understand water usage and find ways to improve. It’s a continuous journey to find the best technology to recycle and reuse water efficiently and there always new methods to explore.”
https://www.youtube.com/watch?v=NgKilEPqyvc
Image credit: Tom's of Maine via Facebook
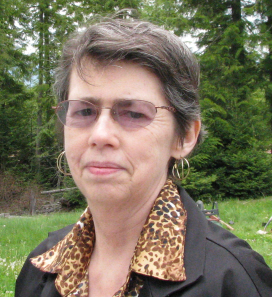
Jan Lee is a former news editor and award-winning editorial writer whose non-fiction and fiction have been published in the U.S., Canada, Mexico, the U.K. and Australia. Her articles and posts can be found on TriplePundit, JustMeans, and her blog, The Multicultural Jew, as well as other publications. She currently splits her residence between the city of Vancouver, British Columbia and the rural farmlands of Idaho.