The principles of effective car manufacturing are now being used in New Orleans to effectively rebuild homes ravaged by Hurricane Katrina. Toyota is part of the St. Bernard Project which is working to improve efficiency of the rebuilding efforts. Toyota has previously used their experience in efficient management of supply chains in their CSR projects like the Community Kitchen and Food Pantry in Harlem.
Before the company stepped in to help, the food pantry had lines down the block. Patrons generally had to wait more than an hour for service. "It's not too different from a production line. There are often a lot of wasted steps, and often a lot of wasted material--in this case, food," says Jim Wiseman, Group VP at Toyota. "The first thing you do is you talk to the folks putting the plates together and figure out how can we streamline this and evaluate where the waste and bottlenecks are occurring."
Toyota figured out how to reduce food waste, for example, by looking at what items of food were thrown away the most (everyone received the same plate). The food pantry was then able to customize its plates, reduce waste and in the end, Toyota was able to get the wait time down to 18 minutes.
Now with the St. Bernard Project, Toyota will help the organization by speeding up the rebuilding efforts by 20% and employ three times as many war veterans as it currently does. The organization has already rebuilt over 380 homes, but it has a largely unskilled workforce made up of war veterans, civilian volunteers, and AmeriCorps volunteers.
Since 1992, Toyota has been using its efficiency secrets for purposes like community rebuilding through the Toyota Production System Support Center (TSSC). The organization set up by Toyota shares the techniques of the ultra-streamlined Toyota Production System (TPS) with Toyota-related suppliers and other companies. By using the Toyota Production System, the organization is able to we are able to "strengthen the capability to solve problems and eliminate waste."
TPS operates on a number of principles which include: waste reduction (not having a lot of extra inventory, just-in-time delivery of parts), letting ideas bubble up from the bottom (supervisors are there to listen to what people are saying), and allowing anybody who works on the production line to stop it at any time if there's an issue.
Considering the community projects that they are targeting as part of their CSR, TPS seems to be an excellent fit. The project in New Orleans will ensure that targets for rehousing are met. Through their TSSC program, Toyota is also focusing on other areas of CSR. During this year, they plan on bringing their expertise to up to 20 community organizations. They also want to start operating TSSC as a a non-profit entity. The company already has a fire station interested in reducing its response time, and a high school interested in using the production system to reduce drop-out rates.
So far Toyota doesn't have a plan to figure out which organizations they want to work with but going by this, they will come up with a system that is definitely efficient.
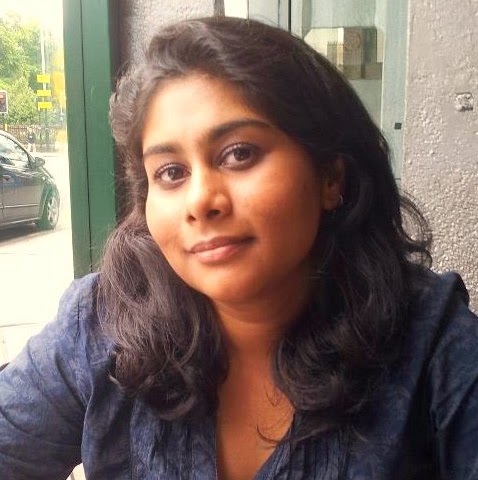
Akhila is the Founding Director of GreenDen Consultancy which is dedicated to offering business analysis, reporting and marketing solutions powered by sustainability and social responsibility. Based in the US, Europe, and India, the GreenDen's consultants share the best practices and innovation from around the globe to achieve real results. She has previously written about CSR and ethical consumption for Justmeans and hopes to put a fresh spin on things for this column. As an IEMA certified CSR practitioner, she hopes to highlight a new way of doing business. She believes that consumers have the immense power to change 'business as usual' through their choices. She is a Graduate in Molecular Biology from the University of Glasgow, UK and in Environmental Management and Law. In her free-time she is a voracious reader and enjoys photography, yoga, travelling and the great outdoors. She can be contacted via Twitter @aksvi and also http://www.thegreenden.net