Following up on Nick Aster's post last week, Ford Motor Company works with a local Detroit manufacturer to churn old recycled tires and soy into parts that now make their way into 11 of Ford’s vehicles.
Ford and its partner, Recycled Polymeric Materials (RPM), have joined forces to make the components since 2008. If the technology can scale, this will serve an example of how the manufacture of “sustainable” automobiles can progress far beyond battery technology and alternative fuels. Opportunities to find more sustainable materials will arise everywhere in a company’s supply chain.
For now the technology is used to make gaskets and seals. Those parts are the finished product of 25% post-consumer recycled tire materials, and 17% from soy. According to Ford, its work with RPM has resulted in the recycling of 2.2 million pounds of recycled rubber, or about 210,000 tires. Furthermore, 150,000 pounds of soy have ended up processed into the parts, too. The reduced weight is also a benefit because the parts collectively have removed over 1600 tons of weight from the road. That reduces the fuel usage of the vehicle.
Ford’s development of products from bio-based or recycled materials reveals the market opportunities for entrepreneurs who can develop alternatives to everything from plastic to lubricants. Ford has already experimented with injection molding processes that could reduce the weight of cars--and therefore improve fuel performance. At a recent NASCAR event I attended with another Triple Pundit writer, a representative of the track mentioned that lubricants and auto fluids derived from bio-based fuels will become the norm. And companies can always innovate using recycled product, as Valvoline has done with its release of its recycled motor oil product in March.
Automobile manufacturers and their supply chain partners really do not have much choice. The rising cost of commodities are forcing companies to innovate. Everything is on the table, from recycling carpet to a focus on water efficiency.
The long term feasibility of plant-based materials is unknown, due to consumer acceptance and concerns about food availability. Nevertheless the innovation and drive to make parts that are both light and offer high performance make this an exciting time to work within the automobile industry.
Leon Kaye, who blogs about Detroit regularly, is the Editor of GreenGoPost.com and contributes to The Guardian Sustainable Business; you can follow him on Twitter.
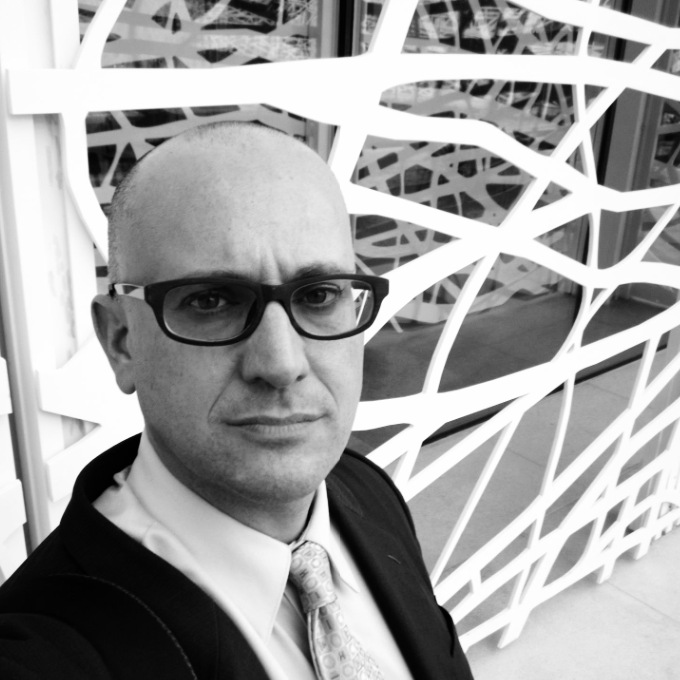
Leon Kaye has written for 3p since 2010 and become executive editor in 2018. His previous work includes writing for the Guardian as well as other online and print publications. In addition, he's worked in sales executive roles within technology and financial research companies, as well as for a public relations firm, for which he consulted with one of the globe’s leading sustainability initiatives. Currently living in Central California, he’s traveled to 70-plus countries and has lived and worked in South Korea, the United Arab Emirates and Uruguay.
Leon’s an alum of Fresno State, the University of Maryland, Baltimore County and the University of Southern California's Marshall Business School. He enjoys traveling abroad as well as exploring California’s Central Coast and the Sierra Nevadas.