In a world where fossil fuels are increasingly expensive and less desirable, it makes sense to unleash the innovation of one's best engineers on developing new materials - free from fossil constraints. This goes double for a car company looking for not only new materials, but ways to make traditional materials both lighter and stronger.
Take injection molding. Almost every panel on modern vehicles is made from a piece of injection molded plastic. Finding ways to use less plastic, while maintaining ease of manufacture and material strength could save both money and yield better fuel economy by producing a lighter car. One of the more amusing points in our tour of Ford's Emerging Technology Labs last week was a demonstration of the process using chocolate as a more delicious plastic substitute.
Ford's otherwise serious engineers showed that by injecting high-pressure gas (in this case CO2) into liquid chocolate, a bubbly finished product could be produced that would maintain the stregth and shape of a traditional chocolate bar with less material. The bubbles form a sort of lattice-work which minimizes any loss of rigidity.
Applying the same technique to plastic, a 15lb dashboard becomes an 11lb dashboard. Although, Ford's engineers were the first to admit the process has more to do with cost savings than fuel economy, a quick trip to the US Dept of Energy website suggests that a 100lb reduction in weight can improve economy as much as 2%. So a few pounds less on a dashboard is not exactly life changing, but every little bit counts.
More interesting still is Ford's research with bio-materials. Ford treated the assembled media to a lunch made primarily from local Michigan produce, specifically emphasizing materials they had been researching as automobile components. From soy to wheat, and even dandelions, we munched on materials which may make up the future of Ford's materials supply chain.
It was a very clever performance, but so far, only soy-based foam has found it's way into manufacture. The 2011 Ford Explorer, and a handful of other models feature seats made of soy.
The reality of course, is that fossil fuel based plastics remain both cheaper and easier to come by, suggesting that hemp body panels are still a long way off. Still, the best efforts of an enthusiastic research team are beginning to pay off and ever so slowly turning the company's supply chain toward a more creative and greener pasture.
(full disclosure, the conference, including travel has been paid for by Ford)
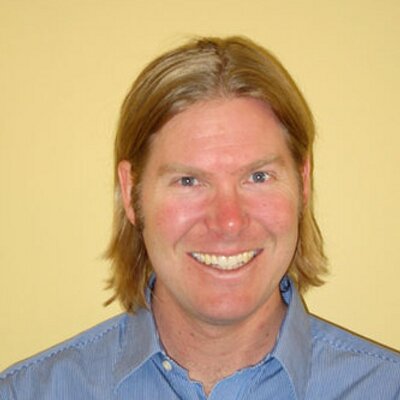
Nick Aster is the founder of TriplePundit. Prior to launching 3p, Nick worked for Mother Jones magazine, successfully re-launching the magazine's online presence. He worked for TreeHugger.com, managing the technical side of the publication for 3 years, and has also been an active consultant for individuals and companies entering the world of micro-publishing. He also worked for Gawker Media and Moreover Technologies in the early days of blogging. Nick holds an MBA in sustainable management from the Presidio School of Management and graduated with a BA in History from Washington University in St. Louis.