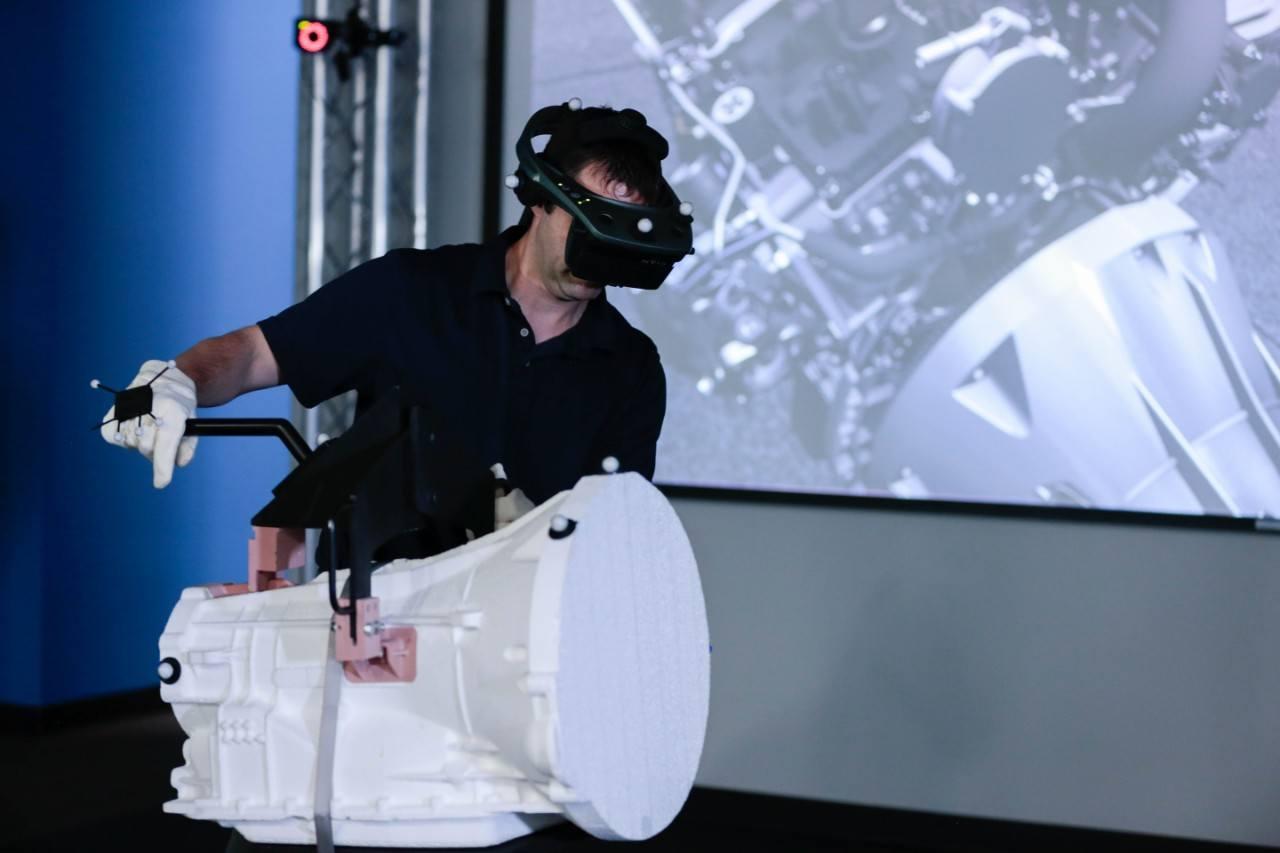
These days the buzz in the auto industry is all about autonomous vehicles and the future of personal mobility. But a technology that's less obvious -- though forms an integral part of vehicle development -- is virtual reality (VR).
This week, we were fortunate to visit Ford Motor Co.’s Virtual Reality labs in Dearborn, Michigan, to take a look at the innovative ways the automaker uses VR across a broad range of activities involved in bringing a new vehicle to market. We examine these in three main functional areas: design, engineering and manufacturing.
Design
From the moment a new vehicle is conceived, virtual reality plays a part. This begins in Ford’s “Studio 2000X," which supports the company's design organization.
Of course, in the old days, cars were designed with pencil and paper. In more modern times, designers relied on computer-aided design (CAD) tools. But in either case, the design of a car -- a three-dimensional object -- was always done on a two-dimensional plane. With VR, however, Ford’s designers can now put on a headset and sketch out their ideas in three dimensions with a digital wand; walking around on a 3-D virtual canvas, so to speak.
Unlocking the potential of designing in 3-D, and by adding animations and placing a 3-D rendering into “photo-realistic environments,” designers can see how their idea for a new car would appear in the real world.
For example, a new sports car design could be placed into a virtual pit-lane at a racetrack and, by wearing a VR headset, designers can walk around it and inspect it in its potential environment from 360 degrees. As a designer, you’d be able to appreciate a full and accurate visualization of a potential vehicle, as clearly as if you were to walk out on somebody’s driveway. This experience is something VR makes possible, even before anything has physically been created.
Engineering
When a vehicle concept is approved and Ford decides to build it, VR again plays an essential role in translating the design into a physical end product.
Engineers get involved in figuring out the finer details and have to make decisions on components, engines, interior ergonomics and so forth. As the product development comes together, the Ford Immersive Vehicle Environment Lab (FiVE) gets to work and begins building a full-size, three-dimensional, virtual version of the car that eventually will go into production.
So, by the time a car is ready to be built, every nut and bolt is accounted for; the seats, dashboard, headlamp support brackets -- you name it -- become part of a fully-realized, virtual version of the car. And again, with a VR headset, designers and engineers are able walk around and inspect the vehicle as if it were really in the room.
They can even see through the car as well if need be. For example, engineers discussing the hinges for a trunk lid could choose to view them through virtual sheet metal of the closed trunk itself.
But why go to the trouble of building a virtual version of the car at all?
It brings efficiency and infinite possibilities to the engineering process that would be hard to achieve physically. For example, parts can be rapidly -- and digitally -- switched out to evaluate things like passenger ergonomics, assess the fit and finish of panels, or work through dashboard design. Designers can also see how subtle changes to the shape of a body panel will affect shadows and light reflection when the car is out there in the real world.
As a result, such immersive VR, as Ford calls it, allows rapid prototyping throughout design and engineering development. It is highly iterative, and can accommodate any necessary engineering variations too. For example, designers encountered a challenge with how an interior panel should be placed in right- and left-hand driving versions of the new Mustang, which they were able to work through using VR, Ford told us.
And the really cool part is designers and engineers can collaborate in remote locations. For example, in creating the new Mustang, teams in the VR lab in Dearborn were able to collaborate with teams in their sister lab in Australia -- and in real time, using VR, engineers were able to walk around the same full-size, 3-D virtual Mustang together and address any detail of the vehicle inside or out.
It’s certainly painstaking to build a virtual vehicle in this detail. But Ford says time is saved in engineering a new car using this technology, while rapid digital prototyping reduces the number of physical clay models Ford would otherwise have to build. In addition, remote collaboration cuts down on travel.
All of this, of course, saves cost. But, perhaps more importantly, Ford says the technology speeds up production timing and allows for superior craftsmanship. Ford claims to be the only car company, to its knowledge, using high-definition, 4-K, real-time VR in its engineering process.
Manufacturing
As the engineering is coming together, another Ford VR lab is busy at work in the area of virtual manufacturing technology, an important process that feeds back information into the design and engineering process.
The virtual manufacturing lab’s chief function is assessing the feasibility in building a vehicle, and it also introduces the human story. Because as much as you can design and engineer a perfect vehicle, it’s for nothing if it’s impossible or unsafe for workers to build.
At the virtual manufacturing lab, Ford’s team uses VR in combination with 3-D printing to create virtual workstations that will eventually be replicated on physical production lines around the world. And with the use of sensors strapped to an employee, full-body motion capture provides data on how a future production line worker would have to move in order to assemble subsystems for a new vehicle.
For example, in the photo to the right, you can see someone wearing a VR headset next to a white 3-D printed object, which is a dimensionally-accurate transmission. He has been asked to line up the transmission -- which you can see -- with the engine, which only he can see in his VR headset.
This was an actual test used to make sure workers would have a good sight-line to the bolt holes needed to attach the engine to the transmission. Based on the VR results, information went back to engineering team, requiring the length of the bolts to be changed in order to allow proper assembly.
A key point of using VR to plan production line workstations is that if something is easy to build, it both enhances quality and reduces the risk for worker injury.
For example, body motion capture allows Ford to measure things like spinal compression values on the lumbar spine if a worker must reach forward in a particular assembly process, and evaluate if these would exceed safe human limits. If they do, engineering teams change the process.
It also allows calculations as to whether, for example, sufficient physical force can be applied to fit a body panel at a given arm-joint angle. Does that change for workers of a different height? If so, how must the process be modified to accommodate workers at the extremes?
Being able to predict how workers will have to move around on a future production line by using VR has been tremendously valuable, Ford says. Impressively, since beginning its virtual manufacturing program, the automaker has:
- Reduced employee injury by 70 percent using the latest ergonomic research
- Reduced over-extended movements, difficult hand-clearance and hard-to-install parts at new vehicle launch by 90 percent
- Reduced employee days away from work due to injury by 75 percent
Putting it all together...
In combination, using VR to enhance design, engineering and manufacturing has proved itself to be a powerful tool for Ford at every stage in a product development lifecycle.
Not only is VR an accurate proxy for real-world activities, but it also provides the benefit of being able to create an infinite number of possible realities, evaluate them all, and select for the most effective one at each stage. In this way, everything can be optimized.
Image credits: 1) Ford (press use only); 2) Courtesy of author
Editor's Note: Flights and accommodation for the author's trip was paid for by Ford Motor Co. Neither the author nor TriplePundit was required to write about the experience. Opinions of the author are his own.
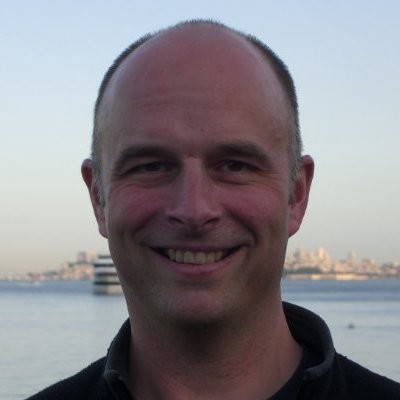
Phil Covington holds an MBA in Sustainable Management from Presidio Graduate School. In the past, he spent 16 years in the freight transportation and logistics industry. Today, Phil's writing focuses on transportation, forestry, technology and matters of sustainability in business.