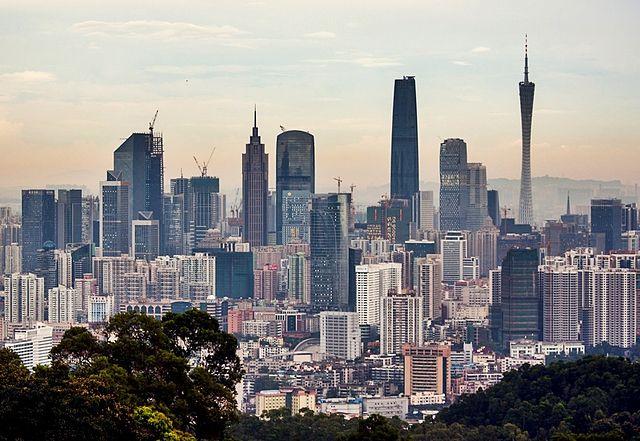
The global textile and garment industry is one of the world’s largest polluters due to its massive impacts on water, soil and of course, people. While consumers are becoming more aware that their fashion choices have on distant places such as Bangladesh, China and India, much work still needs to be done until the industry can be truly described as responsible and sustainable.
While more multinationals insist they are changing their ways, the non-profit Natural Resources Defense Council (NRDC) alleges that only five percent of the companies they monitor consider environmental performance when it comes to making decisions involving their supply chains. To that end, an NRDC report released today covering a pilot project within the fashion industry should serve as a wake-up call to companies that more environmentally responsible choices can improve their reputation while resulting in financial savings.
The report, which outlines the success NRDC’s Clean by Design program achieved in some textile mills in China, offers suggestions on how improving production efficiencies can save money and become more environmentally responsible. NRDC launched the program in a partnership with the International Finance Corporation (IFC) last year in Shaozing and Guangzhou, two cities that are large hubs of Chinese textile manufacturing. Of the over 100 mills that showed interest in the program, 33 were selected to participate. The results, claims NRDC, resulted in significant improvements: 61,000 tons of coal not burned; 400 tons of chemicals not processed; 3 million tons of water saved; 36 million kilowatt hours of electricity conserved; and on the financial side, US$14.7 million dollars saved over the year, with a five year projection totaling US$56.4 million.
The four companies partnering in this project, Gap, H&M, Levi Strauss and Target—and of course their suppliers—were the beneficiaries of these cost savings. At a time when more consumers understand the ravages of fast fashion and the water footprint of their favorite pair of denim jeans, these companies’ competitors should take notes from this project’s report and find ways to work with their suppliers in order to reduce their costs and environmental burdens. And for those in the finance department who only care about the numbers on the ledger, the NRDC points out that some of the biggest savings come from changes that result in forehead-slapping moments. Investments in more efficient motors and lighting, for example, generated the biggest cost savings at many of the mills.
Improvements at one mill alone resulted in 25 percent of the project’s total cost savings. In operation since the late 1990s, the mill dyes and prints woven textiles while employing 6,500 people. Most of the US$3.6 million savings came from retrofitting machines and installing new equipment to conserve water and energy consumption. The collection and reuse of water from dyeing machines alone saved over 500,000 tons of water a year—water that otherwise could have ended up discharged back into the local environment. The NRDC estimated that they payback time for the 13 projects at this mill had a payback period of 13 months—for other mills, the payback time from making similar improvements was far shorter.
In the end, one of the NRDC’s high-level recommendations should be compelling to any supply chain manager: the adoption of 10 best practices can account for 30 percent of a textile mill retrofit's total water and energy savings, in addition to a financial boost that would please any executive. And in China, considering the fact the country is moving towards capping its coal use by 2020, the fact that a relatively small investment can result in big savings cannot be ignored.
Image credit: Jo Sau
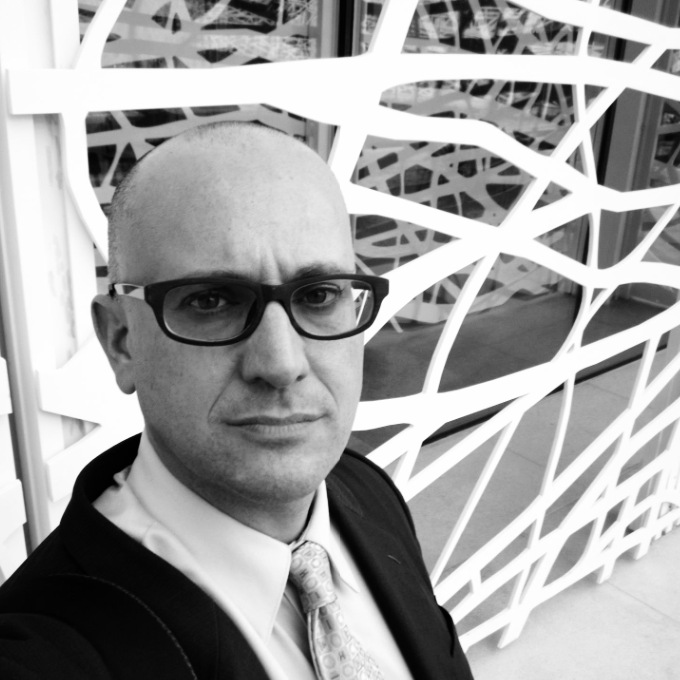
Leon Kaye has written for 3p since 2010 and become executive editor in 2018. His previous work includes writing for the Guardian as well as other online and print publications. In addition, he's worked in sales executive roles within technology and financial research companies, as well as for a public relations firm, for which he consulted with one of the globe’s leading sustainability initiatives. Currently living in Central California, he’s traveled to 70-plus countries and has lived and worked in South Korea, the United Arab Emirates and Uruguay.
Leon’s an alum of Fresno State, the University of Maryland, Baltimore County and the University of Southern California's Marshall Business School. He enjoys traveling abroad as well as exploring California’s Central Coast and the Sierra Nevadas.