GM is joining the growing crowd of companies joining the “landfill-free” agenda. Many companies tout their “zero-waste” policies in their factories - claims that often lie on a slippery slope. “Zero waste” is a noble, but impossible goal: hazardous waste, for example, adds to the complexity because local regulations often govern how such materials are disposed. Nevertheless, "landfill-free" is becoming the mantra at GM, a curious car company amplifying its talk about “sustainability.” The company says it is on a mission to slash waste globally, with the two latest landfill-free facilities in Thailand and South Korea.
Waste diversion efforts are about more than saving on disposal costs: they are a way to inspire innovation and competition within a company as well as engage and motivate employees. Last week, I had another conversation with John Bradburn, GM’s manager of waste reduction efforts, to learn about what the automaker has done to slash waste across its global operations.
“Because perfection doesn’t exist,” says John Bradburn of GM, when asked why the company avoids using the ever-popular term “zero waste.”
So what does "landfill-free" mean? Here’s the answer in GM’s book: any and all waste generated during daily operations skips the landfill. In working with waste processors and recyclers, any stray materials - think food waste somehow ending up in bins of shredded plastic or metal - are landfill-bound but their volumes cannot exceed one percent. Other exceptions exist: for example, construction, demolition and remediation materials are exempt from this definition because in GM’s view, these are not part of the company’s daily operations (future GM construction sites in North America, however, will be held to a “green construction” standard).
So what are the steps GM takes to prioritize this “almost” landfill-free policy? First, GM claims it strives to reduce the amount of such materials in the first place. Next, is the rest of the “3Rs” routine: after reuse, the company pledges to reuse, then recycle. Onsite is preferable to offsite for obvious reasons, such as reduced transport costs and emissions. Next is composting and, if possible, recovering energy from materials. As a last resort — which will raise eyebrows amongst those dubious of “zero waste” and “landfill free” claims — is “incineration without energy recovery.”
Meanwhile GM, with Bradburn and other colleagues at the helm, work with suppliers to also reduce, reuse and recycle within their own operations. One of the company’s largest suppliers, Delphi, is a beneficiary of GM’s best practices shared throughout the supply chain as well as companies outside the automotive industry.
GM’s waste reduction agenda leads to South Korea and Thailand, two countries with their own landfill solid waste problems. But according to Bradburn, the company’s waste diversion effort is also about GM’s facilities challenging each other. Each region within the GM’s global operations also has specific goals to cut waste, and the challenges vary within each country. The Rayong, Thailand plant ditched wood pallets for reusable and recycled-content plastic crates, explained Bradburn, because mulching the wood or turning them into pellets was not a good enough option. In Incheon, South Korea, the company’s Cheongna proving ground has an aggressive recycling program ranging from batteries to plastic to chemicals. Other projects across the region include capturing vapors from fluorescent light bulbs; minimizing sludge from wastewater treatment, painting or grinding; and even sourcing, sanitizing and redistributing gloves locally. The company now has 105 such “landfill-free” sites and aims for 125 by the end of this decade.
Some may sniff at GM’s waste diversion efforts, and it is easy to get caught up in the semantics over terms such as zero-waste and landfill-free. And while the automotive industry clearly has a huge carbon footprint, the products themselves are highly recyclable. Depending on the source, 50 to 75 percent of cars junked worldwide end up recycled; GM claims its cars are 85 percent recyclable by weight, and the company makes about $1 billion annually from recycling. Other automakers, including Subaru, are on the zero-waste or landfill-free bandwagon. So compare the automakers' efforts to the consumer packaged goods industry, including companies such as Procter & Gamble, that crow about their zero-waste facilities while shirking any responsibility for waste, such as disposable razors, that end up in...landfills.
Based in Fresno, California, Leon Kaye is the editor of GreenGoPost.com and frequently writes about business sustainability strategy. Leon also contributes to Guardian Sustainable Business; his work has also appeared on Sustainable Brands, Inhabitat and Earth911. You can follow Leon and ask him questions on Twitter or Instagram (greengopost).
[Image credit: GM]
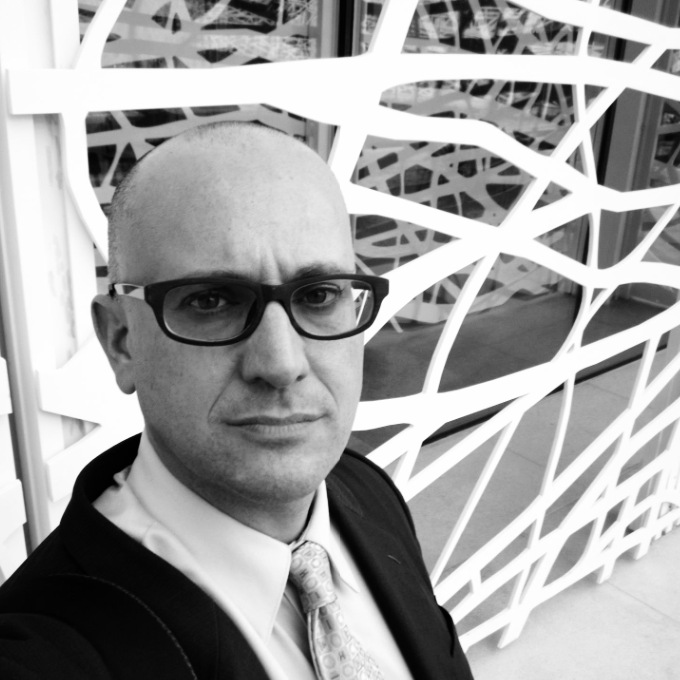
Leon Kaye has written for 3p since 2010 and become executive editor in 2018. His previous work includes writing for the Guardian as well as other online and print publications. In addition, he's worked in sales executive roles within technology and financial research companies, as well as for a public relations firm, for which he consulted with one of the globe’s leading sustainability initiatives. Currently living in Central California, he’s traveled to 70-plus countries and has lived and worked in South Korea, the United Arab Emirates and Uruguay.
Leon’s an alum of Fresno State, the University of Maryland, Baltimore County and the University of Southern California's Marshall Business School. He enjoys traveling abroad as well as exploring California’s Central Coast and the Sierra Nevadas.