A recent Deloitte study offers a concise overview of the challenges companies face within their supply chains and how they, in turn, can partner with their suppliers to solve current problems and prevent new ones. The challenge is huge for multinational companies and their vendors because the increased demands for transparency clashes with the reality that the supply chain for many a business is becoming more complex and opaque.
As energy prices become more volatile, commodities surge in price and manufacturers look for new markets in which to hire workers, it behooves companies even more to ensure their supply chains are more resilient and socially responsible. NGOs are scrutinizing supply chains across the globe in this age of social media that can turn the shenanigans of a wayward supplier into a massive global headache for a company. Add the recent tragedy in Bangladesh, which follows only a few months after another avoidable catastrophe, and the importance of a more collaborative and transparent supply chain becomes even more crucial.
So what are the “four steps to effective supplier collaboration,” according to Deloitte, and what are some examples of what leading companies are doing to confront these challenges head on?
Establish goals and expectations from the beginning
The authors of the Deloitte study remind us that engaging suppliers is about more than setting demands: companies must set clear goals and expectations for their vendors. And if a company does not have a lucid supply chain code of conduct, the organization is already way behind on its social responsibility agenda.
PUMA, for example, has worked with its suppliers on transparency and sustainability challenges as far back as 2006. And Ford Motor Co. was amongst the first multinational companies to declare human rights to be a central component within its supply chain code of conduct.
Identify “hot spots” and opportunities within the supply chain
How is your supply chain, as an ecosystem, performing? A life cycle assessment (LCA) is one tool to identify social and environmental hot spots within your supplier base. Finding a solution to such flare-ups within a firm’s supply chain could end up an expensive proposition, but they prevent even more costs and crises in the near future and even offer a chance for increased collaboration between a company and its suppliers.
Novozymes, the Danish enzyme manufacturer, has conducted life cycle assessments for almost a decade, and uses the data to identify impacts and potential savings within its customer base. As an important cog in leading firms’ supply chains (and, of course, having its own complicated supplier base), such as its largest customer Proctor & Gamble, Novozymes’ LCAs help the company understand the effects of all of its products from their origins as raw materials to how customers use them in their final products.
Evaluate and prioritize suppliers
When the number of your suppliers reaches into the hundreds or even the thousands, managers need an idea of how to gauge potential risks within the supply chain.
Within its food product lines, Unilever developed its Sustainability Stakeholder Rating Tool (SSRT), which the company’s managers can use to assess supply chain actions based on environmental, financial and social issues.
Execute the plan
Once expectations fall into place between a company and its suppliers, the execution of the plan will give everyone the data necessary to assess future risks, performance and potential for new innovations. Everyone should share how results are measured, and of course, share in the successes and benefits.
Nike is one company that transformed how it evaluated its supply chain performance. Last year, the company implemented a new manufacturing scorecard that placed sustainable practices “on equal footing” with conventional metrics such as costs, quality and delivery. Lean, however, does not have to be mean. Nike has worked with suppliers to engage their employees and even empower them because those on the shop floor actually have the best insight on how to optimize efficiency within factories.
The Deloitte report, done in collaboration with ASQ, is accessible here.
Based in Fresno, California, Leon Kaye is the editor of GreenGoPost.com and frequently writes about business sustainability strategy. Leon also contributes to Guardian Sustainable Business; his work has also appeared on Sustainable Brands, Inhabitat and Earth911. You can follow Leon and ask him questions on Twitter or Instagram (greengopost).
[Image credit: Deloitte]
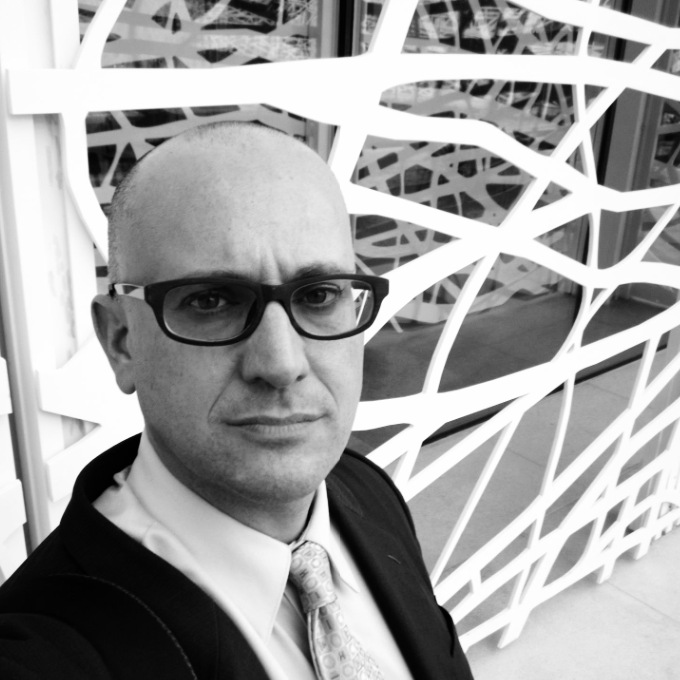
Leon Kaye has written for 3p since 2010 and become executive editor in 2018. His previous work includes writing for the Guardian as well as other online and print publications. In addition, he's worked in sales executive roles within technology and financial research companies, as well as for a public relations firm, for which he consulted with one of the globe’s leading sustainability initiatives. Currently living in Central California, he’s traveled to 70-plus countries and has lived and worked in South Korea, the United Arab Emirates and Uruguay.
Leon’s an alum of Fresno State, the University of Maryland, Baltimore County and the University of Southern California's Marshall Business School. He enjoys traveling abroad as well as exploring California’s Central Coast and the Sierra Nevadas.