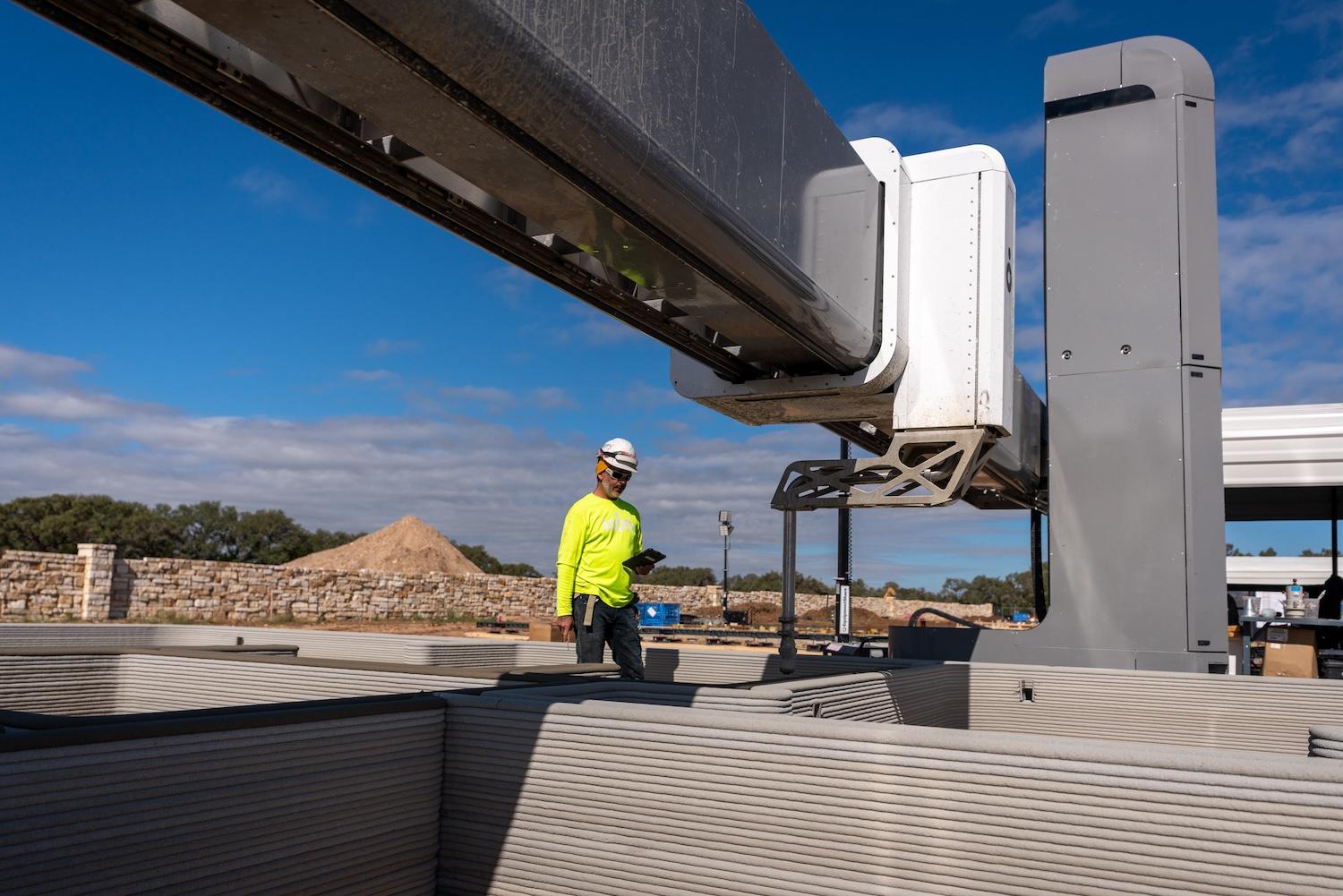
The Texas-based construction and technology startup Icon partnered with the legacy home builder Lennar on a community of 100 3D-printed homes in Georgetown, Texas, that went up for sale in 2023. Now, with a plan to add over 100 more homes to an Austin community for the chronically homeless, the partners are looking to prove printed homes can work at scale. (Image credit: Lennar)
Innovators in the construction industry have been scaling up 3D printers to build entire homes in just a matter of hours. The practice has quickly grown from a high-tech curiosity to a potential means of constructing more affordable housing, a remedy for worker shortages, and a strategy for reducing carbon emissions in the construction industry. Still, there are many hurdles to be crossed before 3D-printed homes become commonplace.
3D printing for affordable housing
Factory-made homes and modular construction can already reduce the cost of buildings and shorten the construction timeline. The factory setting helps to save on materials, and it enables work to continue despite inclement weather. 3D printing — also knowns as additive manufacturing — represents the next level in efficiency. Instead of shipping modules from a factory to a plot of land, 3D printing enables builders to bring the factory equipment right to the construction site.
The 3D printers used in the construction industry are large and frame-like. Instead of the resins used in small-scale 3D printing, they extrude a concrete mixture or other cementitious material.
One early example of 3D printing for affordable housing emerged in 2019 when the Texas-based construction and technology startup Icon partnered with the California housing nonprofit New Story and the organization Échale to produce two new homes in the Mexican state of Tabasco. Both homes were printed in just 24 hours. Another California startup, Mighty Buildings, also established a time frame of just 24 hours for printing the floor, walls and ceiling of a small home.
One firm aiming to scale up for the global market is the Angolan startup Power2Build. The company’s first project was a small house of just 570 square feet, built in 2021 over the span of 48 hours. It was the first 3D-printed home in the world to extrude actual concrete, as defined by the particle size of more than 8 millimeters, according to the Danish firm COBOD, which supplied the 3D printer.
Power2Build’s second home was more than twice as big at 1,507 square feet and was printed in just 30 hours — 4.5 times faster than the original house — while saving 90 percent on construction costs compared to conventional buildings. The second home was also designed with a family-style layout including three bathrooms.
3D printing opportunities and challenges
3D printing has attracted the attention of NASA, which is exploring the feasibility of constructing printed abodes on the moon and Mars. The opportunity to deploy local materials instead of relying on expensive rocket shipments is one benefit, along with the potential to operate 3D printers remotely.
Both of these factors can also contribute to reducing the cost of 3D-printed homes on Earth, though there are still some hurdles to overcome. That includes the high up-front cost of building-sized 3D printers and the absence of internationally recognized construction standards, reports Jesse Bedayn of the Associated Press.
In addition, while 3D printing can reduce the number of workers needed to construct a building, it does not entirely resolve workforce shortage issues in the construction industry. Workers will need to be equipped with new skills that qualify them to set up and operate 3D printers. Transporting the printing equipment to remote communities in need of housing is another obstacle observed in a 2021 feasibility report focused on affordable housing in Alaska.
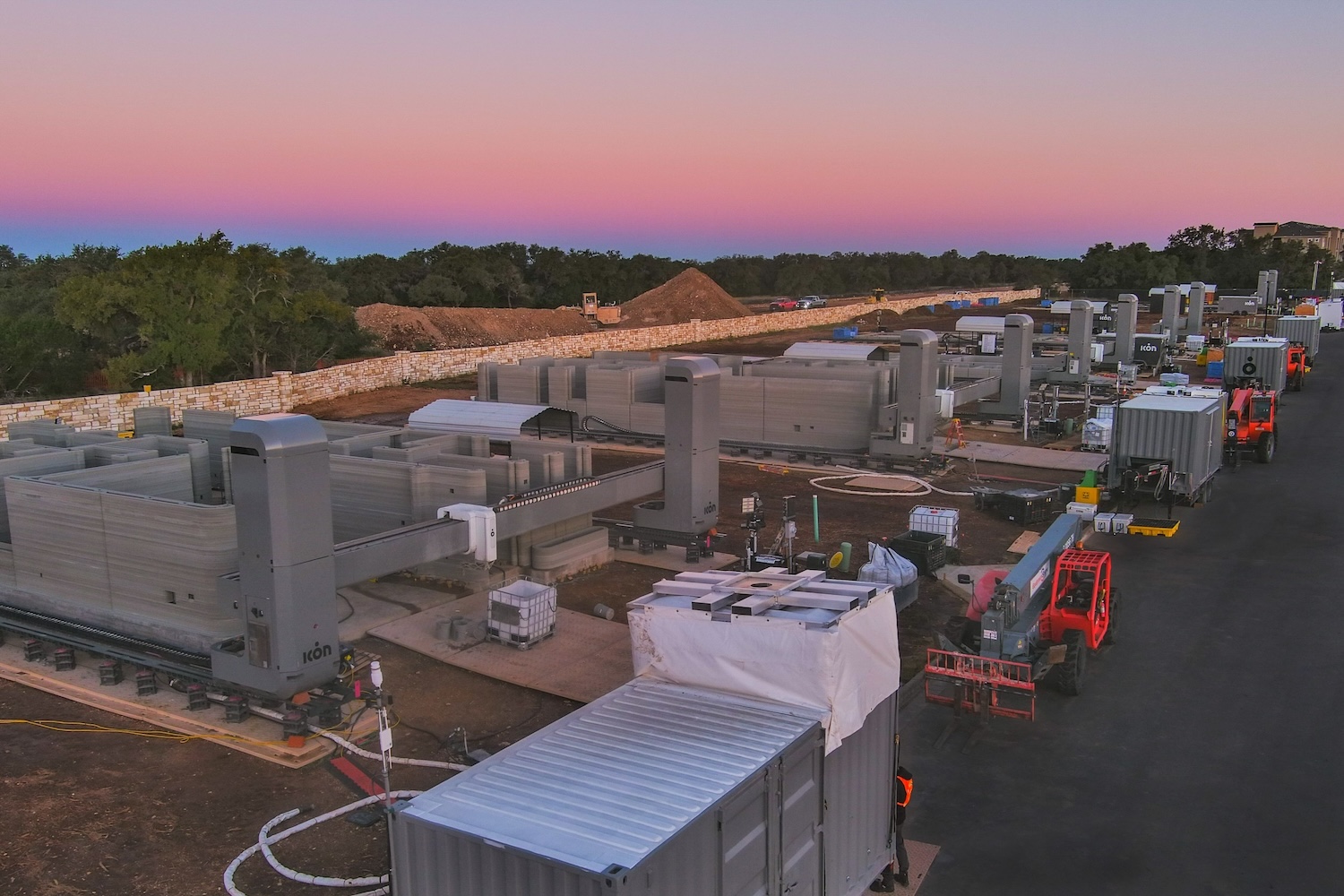
Environmental opportunities for 3D printing
Despite the obstacles, the law of unintended consequences may help propel 3D-printed homes into the U.S. mainstream. Trade analysts are already concerned that new U.S. tariffs imposed on lumber from Canada will raise costs for conventional construction, making the low-cost domestic supply chain of 3D printing a more attractive option.
Further, as the Donald Trump administration’s proposal to log more forests on federal lands threatens environmental conservation, 3D printing presents an alternative for builders and home buyers who value sustainability.
In addition, innovators in the field of 3D printing concrete are beginning to deploy formulas aimed at reducing the carbon footprint of printing mixtures while improving strength and durability. Last year, for example, researchers at the University of Virginia introduced a high-performing cementitious composite that could reduce carbon emissions by 31 percent compared to conventional 3D printing concrete.
In the meantime, the notion of home printing is already starting to catch on. Icon, for example, is constructing 104 new 3D-printed homes at Community First! Village, a 51-acre neighborhood of permanent residences for the chronically homeless in Austin, Texas, run by the nonprofit Mobile Loaves & Fishes.
The Community First! Village project demonstrates that today’s 3D printing technology is ready for scale-up. Icon previously printed just 17 homes and other buildings at the Austin community over a four-year period. Its last build — a 100-home project in Georgetown, Texas, in partnership with the home builder Lennar — only took about a year to complete. The firm’s charitable branch, Lennar Foundation, is also supporting the new 3D-printed homes at Community First! Village.
It would be more than a little ironic if President Trump’s trade wars spark additional momentum in the sustainable housing movement. As Icon observes, the concrete used in 3D-printed homes can also provide energy-efficiency savings, helping households on a budget to manage their utility bills while lowering their carbon footprint.
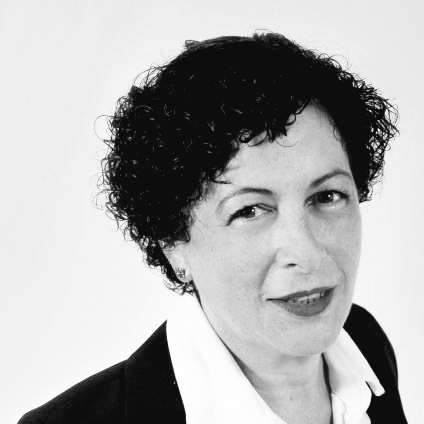
Tina writes frequently for TriplePundit and other websites, with a focus on military, government and corporate sustainability, clean tech research and emerging energy technologies. She is a former Deputy Director of Public Affairs of the New York City Department of Environmental Protection, and author of books and articles on recycling and other conservation themes.