A tailings facility at a copper mine in South America. (Image: Michael Ingwersen for Circular Mine)
This article is part of our series on responsible mining solutions. The push for clean energy is fueled by a growing demand for minerals, but conventional mining has a track record of harmful social and environmental impacts. Zero waste mining is another potential solution to that problem.
Mining is big business. The capital expenditure to start a mining project and annual profits can be in the order of billions of dollars. The amount of material processed is also enormous. The largest copper mine in the world, Escondida in Chile, produces more than 1 million metric tons of copper per year.
Miners move a lot of rock, and most of the rock they extract isn’t used.
“Base metal mines effectively recover less than 1 percent of the volume of rock extracted,” according to the Canadian government’s Mining Innovation Council. “Gold deposits recover less than a hundredth of a percent.” Base metals are abundant and easily extracted metals like copper, nickel and zinc.
Reports estimate that global mining waste could be around 65 billion tons to over 100 billion tons annually. The weight of all humans on Earth is around 440 million tons. Using conservative estimates, the global mining industry discards the equivalent weight of all humans on Earth every 2.5 days.
Mining’s waste problem is enormous, but researchers and mine waste management companies say zero waste mining could become a reality, and it would be in the best economic interests of mining companies to do so.
How to eliminate mine waste
“We believe that 100 percent of mine waste can be avoided,” said Stuart Sandler, global director of business development at Circular Mine, a company that provides mine waste management solutions that is currently in the pilot project stage.
Bear in mind that mines are not neglectfully wasteful. Getting resources to remote mines is expensive. Mining companies have to build roads to get there, power stations to generate electricity, and anything they want to use needs to be transported from far away. It’s not in their economic interest to be wasteful, but there is still a large portion of material they don’t see value in, yet.
Mine waste is separated into two categories: waste rock and tailings. Waste rock is ore that doesn’t contain enough minerals to be processed and is discarded in a pile near the mine. At the Escondida copper mine, waste piles cover four square miles and are more than 400 feet tall.
Tailings are what’s left once a mine has crushed the good rock and extracted all the minerals that it can. Due to the water and chemicals added to the rock during processing, tailings are usually a liquid mixture held in ponds or dams, which can also span multiple square miles and are usually highly toxic.
“Copper tailings have a wide variety of minerals beyond copper,” said Abe Jalbout, CEO of Auxilium Technology Group, a company that repurposes mine tailings. “We're looking at copper, nickel, zinc, cobalt, and even rare earths, and they’re all really accessible.”
Copper mine waste can be reprocessed to recover an extra 30 percent of copper, enough to meet copper demand for the next 70 years, Jalbout said.
After valuable minerals are removed, the remaining waste can be cleaned and processed for use in other industries like construction, cement or even agriculture.
“We’re able to concentrate these deleterious components, get rid of them, and produce a clean material that can be used for construction or other types of applications,” Jalbout said. “We’re able to use 100 percent of the input stream. The byproducts can be used directly on the mine site, sold as value-added products, or reintegrated into our system.”
The untapped value of mine tailings is around $3.4 trillion, Jalbout said. The process to recover that value is not a one-size-fits-all approach, however.
“Every mine's tailings and processes are different,” Sandler said. “Something that works here may or may not work at the next mine. We have to do a detailed study every time to identify opportunities.”
Tailings management is costly and dangerous
Building a tailings pond or dam is a massive engineering project. The scale is enormous and due to the toxic nature of tailings, companies have to ensure their waste is safely contained.
The Brumadinho disaster in Brazil killed 272 people when about 2.6 billion gallons of waste burst from the tailings dam at an iron ore mine, destroying local communities. Other tailings breaches have also cost human lives and wreaked havoc around the world.
“One company we spoke with has a mine in South America that we estimate is spending over $100 million per year to manage their tailings,” Sandler said. “And there’s no return on that investment. It’s just an expense.”
Although tailings can be highly toxic, cleaning and repurposing can create clean, reusable raw materials for other industries. By repurposing them, mines can eliminate the tailings management costs and even find an additional source of revenue.
A brickmaker, for example, needs rocks to make bricks. A mine could repurpose its waste and sell it to brickmakers or give it away for free and still be in a better position, Sandler said.
“Even though you’re not giving me any money, you’re still lowering my costs because I don’t have to manage that waste anymore,” he said. “This is what we call the circular economy, where the waste of one industry becomes the raw material of another.”
At a smaller mine, Auxilium can “completely eliminate the need for the tailings storage facility,” Jalbout said. The company can process around 10 million tons of annual waste per mine and is installing its first six on-site plants in 2025 in the U.S., Peru, Australia and West Africa. Having a strong tailings management strategy can be the difference between getting a project approved or rejected.
While this solution may not be ready to tackle waste from mammoth mines, it can have a significant impact on smaller operations.
Are miners willing to change?
If you talk to people who present innovative solutions to mining companies, they will often tell you it is difficult to get the mining industry to try something new. It is somewhat surprising then, that Auxilium is already seeing commercial success.
“I must say the mining industry is very receptive,” Jalbout said. “I think these companies are hungry for innovation and ways to improve their operations.”
He projects Auxilium’s six on-site installations next year to mitigate over 30 million tons of tailings.
“Like anything else, it’s just about market adoption and traction in terms of getting these things standardized,” Jalbout said.
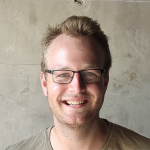
Andrew Kaminsky is a freelance writer with no fixed location. He travels all corners of the globe learning about the different groups that call this planet home, seeing natural wonders, and sharing laughs with the people he finds along the way. An alum of the University of Winnipeg's International Development program, Andrew is particularly interested in international relations and sustainable development. In his spare time you are likely to find Andrew engaging in anything sport-related, or finding common ground with new friends over a craft beer.