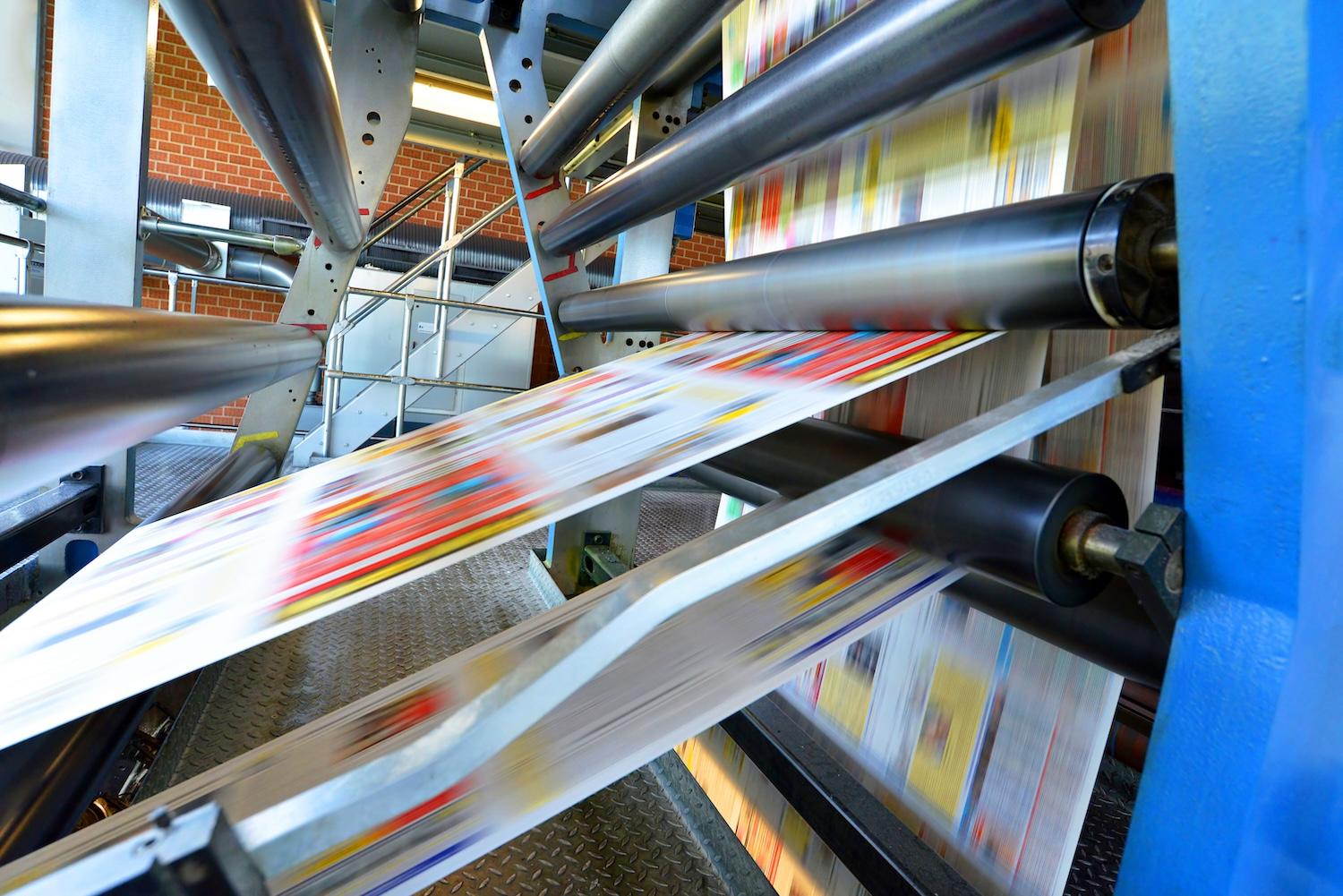
3M and Evoloh are developing a system that uses roll-to-roll manufacturing, which you might recognize as the process used to print newspapers, to reduce the cost of building the devices that make green hydrogen. (Image: industrieblick/Adobe Stock)
Green hydrogen is a key driver of the global decarbonization effort, but it faces a scale-up problem. The electrolyzer systems that generate green hydrogen are expensive and cumbersome to manufacture. A faster, cheaper manufacturing strategy is needed, and industry stakeholders are developing solutions.
From tape to the energy transition
The well-known U.S. firm 3M provides an example of stakeholder interest in new electrolyzer manufacturing systems. The company launched in 1902 with a focus on new kinds of sandpaper.
Since then, it compiled extensive background in two areas that apply directly to the electrolyzer problem, materials science and roll-to-roll manufacturing, which involves feeding a flexible material through a system of rollers to print on it, cut it, or coat it, among other things. That experience is reflected in the company’s roster of products manufactured with roll-to-roll systems, including the introduction of recording tapes in the 20th century.
The roll-to-roll difference
Tape recorders have faded from use in the 21st century with the rise of digital technology, but the rapid-fire pace of roll-to-roll manufacturing is still at work in the energy transition. The U.S. Department of Energy, for example, promoted roll-to-roll systems as a means of scaling up the manufacture of new thin film solar cell technology.
To get a picture of the difference roll-to-roll manufacturing can make in the electrolyzer field, consider its impact on the printing industry. The first printing presses emerged in the 15th century, requiring operators to place a single piece of paper on a flat surface, stamp it and remove it. The stamping method held sway until the 19th century when printing houses incorporated cylinders. Instead of breaking the process into steps, cylinders enable a continuous flow of material from one roll to another.
The high speed of cylinder-based printing was showcased to dramatic effect in famous films of the 20th century, such as “Citizen Kane,” where newspapers are shown whizzing around machinery the size of an entire factory floor in a seamless flow.
Roll-to-roll printing and green hydrogen
Electrolyzers are composed of cells arranged in stacks. They push hydrogen from water with an electrical current. When that current is provided by renewable energy, electrolyzers offer a green alternative to the fossil resources needed for conventional hydrogen.
The implications for the energy transition are widespread. In addition to decarbonizing fuels and industrial systems, green hydrogen production can contribute to grid reliability and stimulate further investment in renewable energy projects.
“With the expansion of renewables as a clean energy input, we can align supply and demand on the grid, and we can use those otherwise unused electrons and put that in a water electrolyzer,” Andy Steinbach, senior research specialist at 3M, told TriplePundit. “This is an opportunity from a technology standpoint.”
Before that opportunity can be realized, the cost of green hydrogen needs to be competitive with fossil resources. Estimates vary, but the U.S. Department of Energy uses the standard figure of $5.00 per kilogram for green hydrogen. It’s set a goal of reducing that by 80 percent within 10 years, down to $1.00 per kilogram, with an intermediary step of $2.00 per kilogram by 2026.
In terms of competition with fossil energy, the gap is narrowing. The cost of making hydrogen from natural gas ranges from $0.50 to $1.70 per kilogram depending on the market, according to the International Energy Agency. Attaching carbon capture systems to the process bumps up the range to $1.00 to $1.70 per kilogram, further closing the gap.
The Energy Department’s goal is consistent with a 2020 report on electrolyzer manufacturing issued by the International Renewable Energy Agency. It concluded that the cost of electrolyzer systems could drop by 40 percent over the short term and up to 80 percent over the long term if the industry scales up, standardizes and draws lessons from early adopters.
As viewed by 3M, one of those lessons is to move electrolyzer manufacturing from partial to full automation.
“A lot of the components are [currently] built in a semi-automated process,” Tim Yamaya, a corporate entrepreneur at 3M, told TriplePundit. “They are partly hand-assembled, and the industry is trying to get to fully automated production.”
Yamaya also drew attention to the impact of electrolyzer costs on the competitiveness of green hydrogen.
“3M’s focus is to enable renewable hydrogen to be cost competitive. We want to enable that through high-performance materials and process expertise,” Yamaya said, referring to the $1.00 per kilogram goal of the Energy Department.
Investing in the green hydrogen industry of the future
Towards the goal of reducing the cost of manufacturing, 3M Ventures, the company’s venture capital arm, invested in the electrolyzer firm Evoloh.
Evoloh is developing a roll-to-roll system for manufacturing low-cost electrolyzer “stacks.” The company is also cutting costs by eliminating expensive or rare materials in favor of inexpensive, locally sourced materials including steel and aluminum as well as plastic. Among other cost-cutting measures, Evoloh won a grant from the U.S. Department of Energy aimed at deploying plain tap water instead of the purified water required by conventional electrolyzers.
Bill Weber, the business building director at 3M Ventures, told TriplePundit that the company plans to contribute its experience driving down material costs in the direct air carbon capture field to help Evoloh scale up its manufacturing system.
“Evoloh’s ambition is to do electrolyzer stacks roll-to-roll,” he explained, “And we also do carbon capture materials roll-to-roll, so we can rapidly create the scale that the world needs.”
More support for roll-to-roll systems
The potential to introduce rolls-to-roll systems in electrolyzer manufacturing has also caught the attention of the U.S. Department of Energy. The agency announced the launch of the new R2R Consortium, a collaborative effort involving five of its research laboratories, this year.
“Roll-to-roll manufacturing can reduce costs by increasing process efficiency and reducing material waste, but there are challenges related to materials synthesis, coating, drying, and quality control that need to be addressed to scale up these processes for industry adoption,” according to the department.
The focus on roll-to-roll printing is a timely one. In its latest global hydrogen market review, the International Energy Agency warned that demand for electrolyzers is “highly uncertain,” as the industry continues to struggle with costs.
And in May, the International Council on Clean Transportation advised that “where costs will land in the future can’t be known with certainty.”
Nevertheless, investor interest in producing green hydrogen continues to show signs of life, as recently illustrated in the U.S. by the announcement of two new projects totaling 8 gigawatts in Texas.
If 3M, Evoloh, the Energy Department and other stakeholders realize their plans for reducing the cost of electrolyzer manufacturing, the future of green hydrogen will look much more certain than it does now.
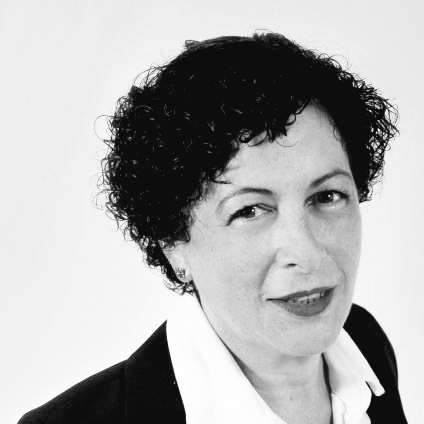
Tina writes frequently for TriplePundit and other websites, with a focus on military, government and corporate sustainability, clean tech research and emerging energy technologies. She is a former Deputy Director of Public Affairs of the New York City Department of Environmental Protection, and author of books and articles on recycling and other conservation themes.