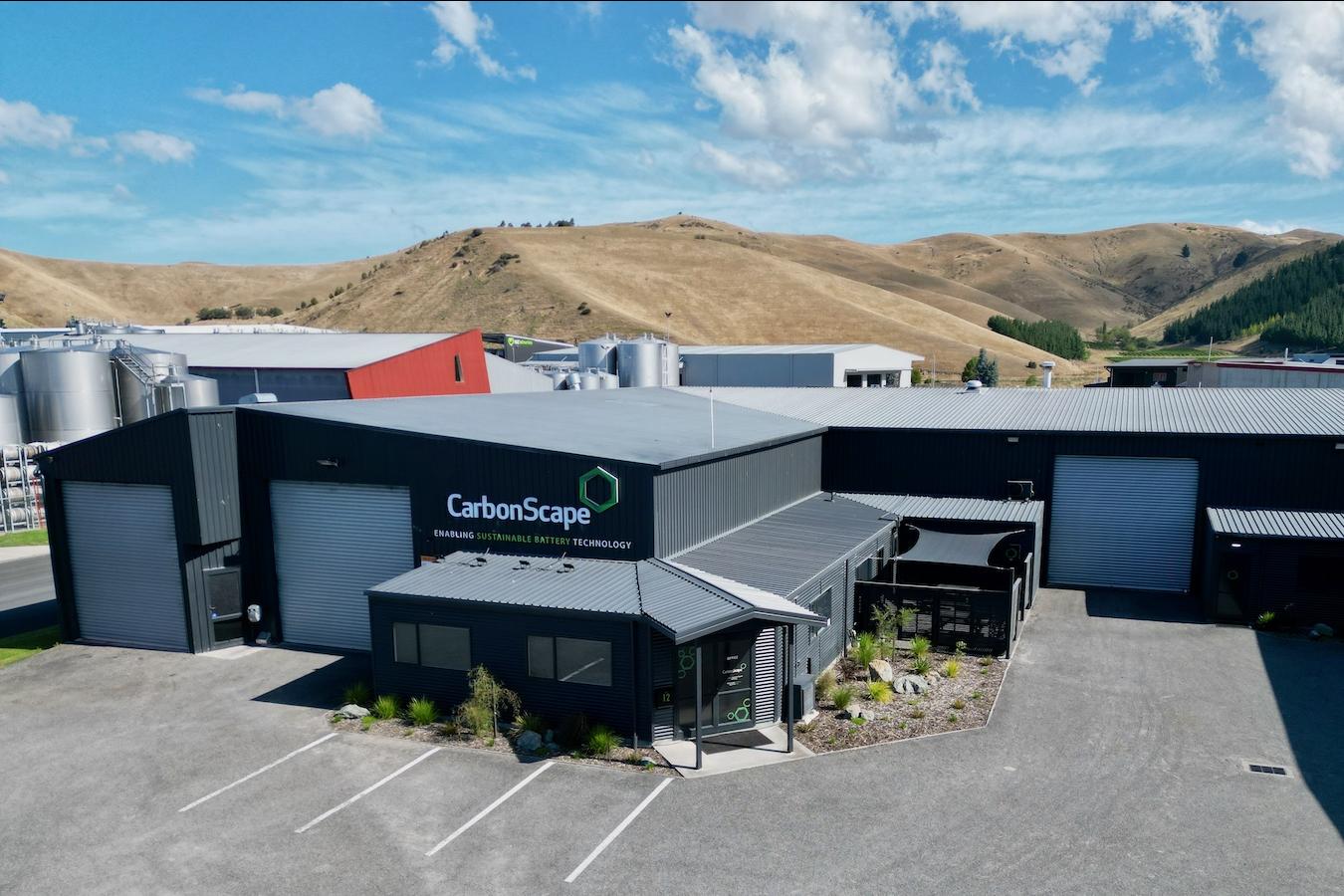
The CarbonScape pilot plant in Blenheim, New Zealand, where the company produces biographite from renewable materials to be used in lithium-ion batteries. (Image courtesy of CarbonScape Ltd.)
This article is part of our series on responsible mining solutions. The push for clean energy is fueled by a growing demand for minerals, but conventional mining has a track record of harmful social and environmental impacts. Better lithium-ion batteries are another potential solution to that problem.
If the battery world had awards, lithium-ion would be the MVP, or maybe MVB (for battery). They aren’t perfect, however. There are valid concerns over extracting lithium from environmentally sensitive areas, safety concerns over thermal runaway, the recyclability issue of lithium-ion batteries, and performance limitations.
If lithium-ion is still the best, how can its internal composition be improved to offer a better-performing, more sustainable, and potentially, lower-cost alternative?
How does a lithium-ion battery work?
Lithium-ion batteries have an anode on one side and a cathode on the other. When charged, the lithium ions start in the anode. When an electric vehicle (EV) starts up and needs power, for example, the lithium ions begin moving one by one across the battery to the cathode. This movement of lithium ions creates energy that is used by the electric car.
When all of the lithium ions have moved to the cathode, the battery is at 0 percent and needs to be recharged. During recharging, the ions all move back to the anode.
In conventional lithium batteries, the anode is made of graphite and the cathode is made of a lithium compound, usually lithium cobalt oxide. The extraction, processing and production of these raw materials carries negative environmental and social consequences like carbon emissions, land degradation and, particularly with cobalt, human rights violations.
Businesses and researchers are exploring new alternatives to the lithium status quo.
A more sustainable graphite solution
Traditional graphite comes from a byproduct of the oil industry, called synthetic graphite, or by mining, called natural graphite. Both carry significant environmental concerns. On top of that, China controls graphite production and processing, with over 95 percent of battery-grade synthetic graphite coming from China. Synthetic graphite is preferred to natural graphite in batteries for its higher performance.
CarbonScape is challenging graphite’s heavy reliance on China and the oil industry by making graphite out of waste from the timber industry.
“You have a lot of byproducts from cutting down wood like wood chips, sawdust or thinnings,” said Vincent Ledoux-Pedailles, chief commercial officer at CarbonScape. “The technology we’re developing is to extract the carbon from that biomass and convert it into a graphite that can be used directly in a battery application.”
CarbonScape calls it biographite. The bioproduct is similar to synthetic graphite in terms of performance, but with a fraction of the environmental impact and without reliance on China.
“If you look at the chemicals used when producing biographite, the reagents intensity is much lower than when you produce synthetic graphite or natural graphite,” Ledoux-Pedailles said. “We're not using fossil fuel feedstock. We're not using a mined feedstock. We're using something which is fully sustainable.”
One of the limitations of being a graphite producer is that graphite is a specialized customized product — not all graphite is equal.
“Your graphite is going to be like 99.98 percent pure, but what’s important is that remaining 0.02 percent,” Ledoux-Pedailles said. “From your first commercial plans, you’re only going to have a maximum of three customers because you need to customize these products to their performance requirements. The collaboration with downstream players is key because it will also impact the design of your plans.”
CarbonScape is still in the early stages, but it is constructing a demonstration plant in Finland, with plans to expand commercially into Europe and North America.
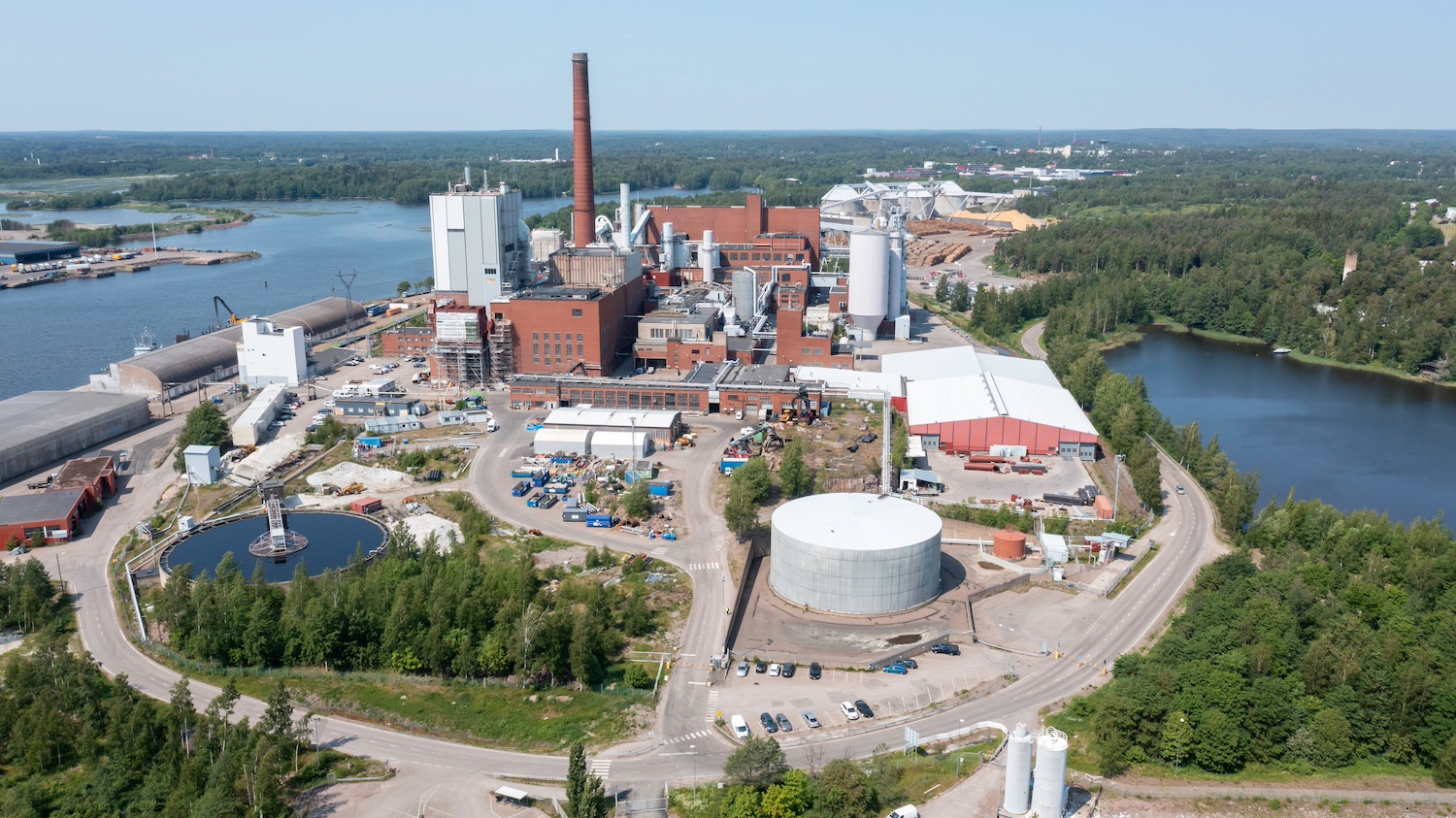
Replacing graphite with silicon
Another option is removing graphite altogether and replacing it with a more sustainable, and potentially better-performing, material: silicon.
Silicon isn’t exactly free from environmental impacts because a lot of energy is required to heat silica so it can be processed and turned into battery-grade silicon. The process is, however, friendlier to the environment than graphite production and without some of the social harms associated with mining natural graphite, like poor worker conditions and human rights violations.
Performance-wise, the energy capacity of silicon anode lithium-ion batteries as compared to graphite anode lithium-ion batteries is much, much higher.
“The advantage of silicon over graphite is that one silicon atom can store 4.4 lithium atoms,” said Magda Titirici, chair in the Sustainable Energy Materials Department at the Imperial College London. “In graphite, one lithium gets stored per six carbons.”
With such high energy density, there are some challenges. One is that the lithium-based cathode cannot match the storage capabilities of silicon, and another is that it brings the life cycle of the battery down.
“When we dial up energy density to the maximum today, we typically give it up on the cycle life side,” said Ronnie Tao, vice president of business development at Amprius, a company that produces lithium-ion batteries with silicon anodes. “Our life cycle in those cases is about 100-150 cycles. The unspoken rule for consumer electronics is 500 cycles.”
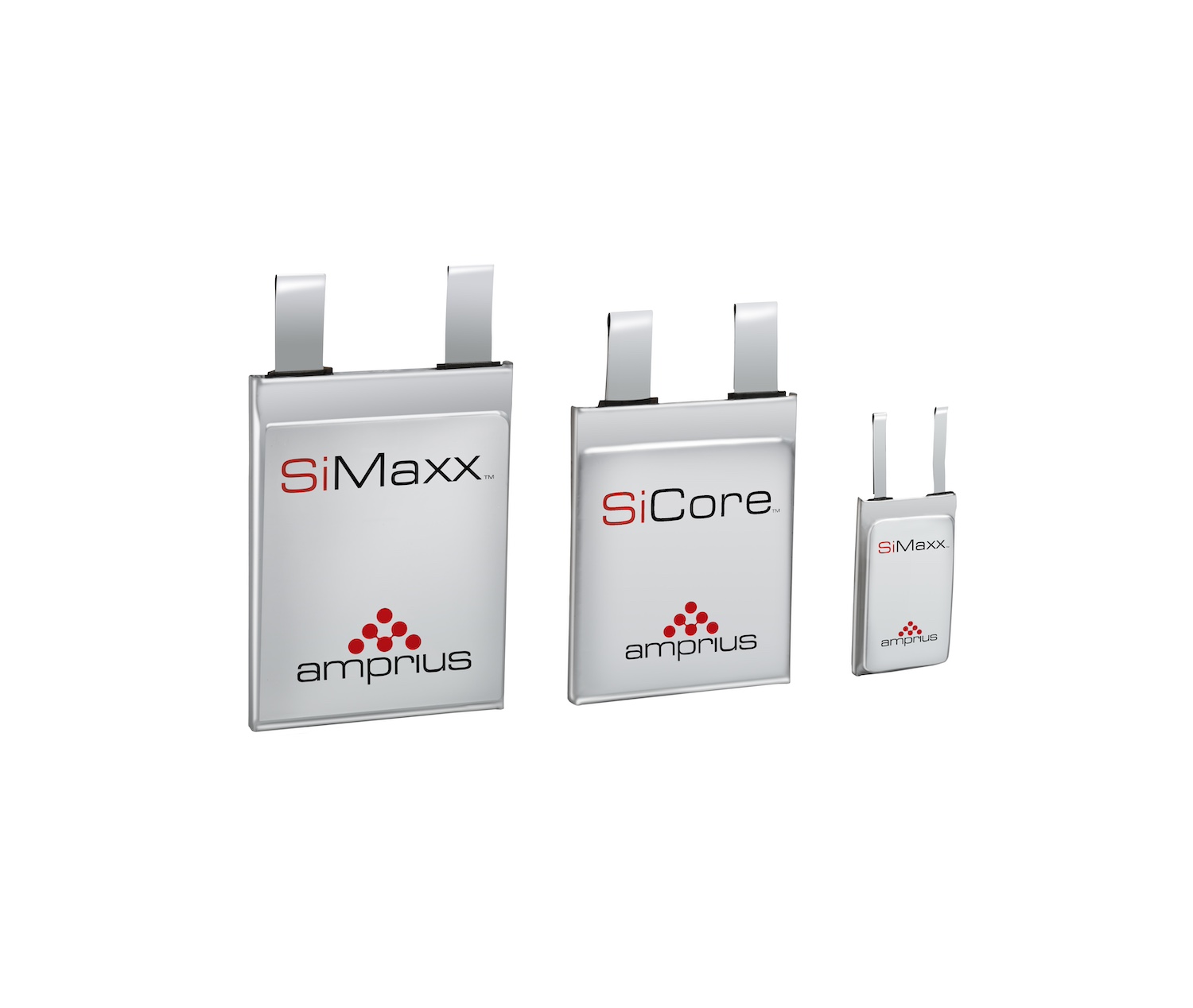
This high energy, low lifecycle battery is well-suited to some applications like high altitude satellites, Tao said.
In terms of costs, silicon anode batteries are more expensive than the graphite versions. But scaling the silicon anode supply chain would likely bring costs below graphite.
“Silicon is literally made out of sand, so it is abundantly available all over the world,” Tao said. “The overall cost would be lower at scale. We’re just not there yet.”
Silicon anode batteries also offer recyclability advantages.
“You could dissolve it in water, and it'll separate out,” Tao said. “It's a much easier process to get a fully recyclable battery.”
Despite the advantages that silicon anode batteries offer, market uptake of this technology is hesitant.
“There are so many things out there that it leads to a lot of market confusion,” Tao said. “Until there's a clear industry focus to move in this direction, it’s kind of hard to grow at scale.”
Removing cobalt from lithium batteries
One of the most problematic minerals in terms of environmental and social costs is cobalt. Most lithium-ion batteries rely on cobalt to make up part of the lithium cathode. Battery makers and researchers are pursuing innovative methods of creating a lithium-ion battery without cobalt.
Researchers at the Massachusetts Institute of Technology (MIT) produced a lithium-ion battery that replaces cobalt with organic materials in the cathode. The battery is cheaper to produce and competes on performance. Lamborghini licensed a patent on the technology.
“It is already competitive with incumbent technologies, and it can save a lot of the cost and pain and environmental issues related to mining the metals that currently go into batteries,” Mircea Dincă, the W.M. Keck Professor of Energy at MIT, told MIT News.
Researchers at the University of Tokyo replaced cobalt with a combination of manganese, silicon and oxygen. The batteries perform well but face some longevity issues.
Lithium-iron-phosphate batteries are also promising options, though they have roughly half the energy density of regular lithium-ion batteries, meaning they need to be bigger to achieve similar performance metrics. Despite this, Tesla used these batteries in its Model 3 cars. But Tesla recently discontinued the use of lithium-iron-phosphate batteries in its U.S. models due to complications with its China-based supply.
Government regulations and international trade spats can limit the range of options available to producers and consumers.
Always room for improvement
Lithium-ion batteries aren’t going anywhere. By making small changes, battery makers can mitigate some of the environmental and social impacts associated with their production and material sourcing, while potentially bringing down costs. Given the size of the industry, those changes can make a huge difference to the people and the environments affected by lithium-ion battery production.
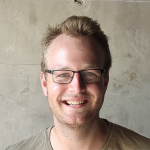
Andrew Kaminsky is a freelance writer with no fixed location. He travels all corners of the globe learning about the different groups that call this planet home, seeing natural wonders, and sharing laughs with the people he finds along the way. An alum of the University of Winnipeg's International Development program, Andrew is particularly interested in international relations and sustainable development. In his spare time you are likely to find Andrew engaging in anything sport-related, or finding common ground with new friends over a craft beer.