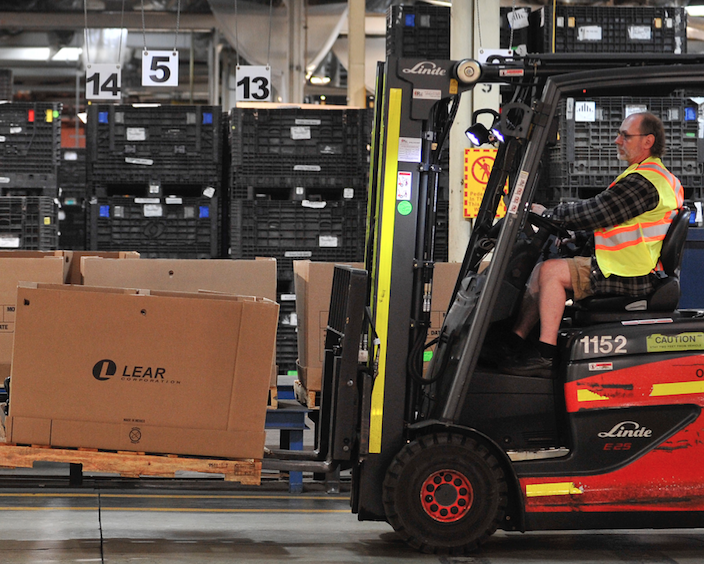
Despite regional pressures on municipal landfills, the U.S. still has plenty of space in which to dispose of its garbage. The waste management industry is quick to dispel the concept of the disappearing landfill as a myth, and the costs of solid waste disposal are, at worst, increasing at a modest rate year-to-year.
Nevertheless, Americans generate a lot of garbage. One estimate suggests that if all the garbage collected in the U.S. over one year was dumped in a pit 400 feet deep, that hole would consume 1,000 acres of land.
At a time when companies are trying to cut costs wherever they can -- and prove to their stakeholders that they are a lean, responsible or environmentally-conscious organization -- tackling waste is one place to start. So it make sense that more companies are striving to go zero waste to landfill (ZWTLF), or as close to it as possible.
One company that is moving toward a total zero-waste operation is Ford Motors. “We feel that from a company perspective, it’s something we need to stand for,” said Andy Hobbs, sustainability, environment and safety engineering director for Ford. “Environmental stewardship is important to us, and we take the view that we should not just collect waste and put it in a hole in the ground.”
Put in a more elegant way, Hobbs describes Ford’s zero-waste program as taking action on conservation, specifically toward eliminating landfill disposal while also reducing water consumption.
The challenges that companies face when they transition to a zero waste operation often vary by industry and location, Hobbs told us. But the overall process in which a project leader should go about this route is fundamentally the same.
The person managing the process needs to evaluate both broad company-wide objectives, as well as facility-specific goals, Hobbs advised. “Establish aggressive short-, intermediate- and long-term goals to eliminate waste being disposed in a landfill, and include percentage reduction goals, as well as deadlines for accomplishing such goals."
In Hobbs' view, it is critical for any business leader working on a zero-waste project to be realistic. Make it clear what you and your company want to accomplish, as in establishing short-term waste minimization targets while setting long-term, zero-waste-to-landfill goals. And all of these targets should be measurable, achievable, ambitious and implemented over a specified time, Hobbs told us.
For those who are conceptualizing a zero-waste program from scratch, Hobbs suggested following a seven-step framework – which, again, can vary based on industry or a company’s location:
- Gain management’s support
- Develop accurate and measurable metrics
- Define what zero waste means to the company
- Finalize and communicate those zero-waste goals across the organization
- Decide on a “top five” priority list
- Develop, implement, and share zero-waste steps and actions
- Finally – and arguably most importantly -- share your company’s successes
Furthermore, Hobbs insisted that any corporate zero-waste program must be a cross-functional effort; it will not succeed if is only driven by one department such as engineering or EHS (environmental, health and safety). A company should allocate dedicated personnel from across its operations to ensure the zero-waste agenda succeeds.
On that last point, Bill Hoffman, senior scientist at UL-EHS Sustainability, underscored that a zero-waste program cannot succeed as a top-down approach. “On nuts and bolts, you have to get everyone involved because it really is one of those types of projects where yes, you can set ambitious goals and processes, but in the end, it’s the person on the loading dock sending discarded materials out the door who has the control over where that waste is going out.”
To that end, UL-EHS provides three validation levels for companies that wish to ensure their waste diversion claims are audited and can be verified: greater than or equal to 80 percent waste diverted from landfills; 98 percent or higher; and, of course, 100 percent zero waste, which means that not one item goes to an offsite landfill.
The reality is that for most companies, achieving a waste diversion rate of 80 to 90 percent is relatively easy. After all, an auto manufacturer such as Ford will have little problem offloading scrap metal; a brewing company can easily find someone who can take spent grains and turn them into animal feed. Packaging materials and recyclables such as paper, plastic, and even pallets are the low-hanging fruit. Other materials may need more thought, but they can often be reused within a facility, or even donated.
But once these first steps are accomplished, project leaders can find themselves in the weeds as they hone in on that final 10 to 20 percent. What do you do with random objects such as air filters or the vinyl banners a marketing team used for a one-off event? Those last few percentage points can stump even the most thoughtful and creative professional.
But there are answers, said UL’s Hoffman, even if the solutions hard to find at first. Incineration may not be the ideal option, but if that can be part of a waste-to-heat or waste-to-energy option, it can help your company meet its goals. That hazardous chemical lurking in plastic jugs, it may turn out, could be reused over and again as a solvent.
But the bottom line is: Zero means zero. Hobb noted that Ford has always found non-landfill solutions for its waste. Hoffman explained that as an organization that issues certifications, UL is not in a position to advise a company what to do what those pile of materials in a storeroom refusing to go away. Nevertheless, Hoffman said, “We can tell them there’s a way.”
Finally, there is that question of timing. Companies with operations in locations across the country and even the world will find different logistics and regulatory challenges. Launching a program and seeing it in action can happen in six to 12 months, Hoffman told us, but the key is being realistic.
Hobbs noted that Ford views zero waste from an engineering perspective, a poignant example for other companies: After one of Ford’s plants or offices appears to reach that zero-waste point, the company waits three months and validates data in the interim to ensure that absolutely nothing -- including a bottle of water on someone’s desk -- is going to a landfill.
To date, Ford counts 77 of its facilities as zero waste. The company expects all of its engine and power train assembly plants to reach that metric this year, with an additional eight to 10 sites going zero waste during 2018.
Will your company follow suit?
Photo credit: Ford Motor Co.
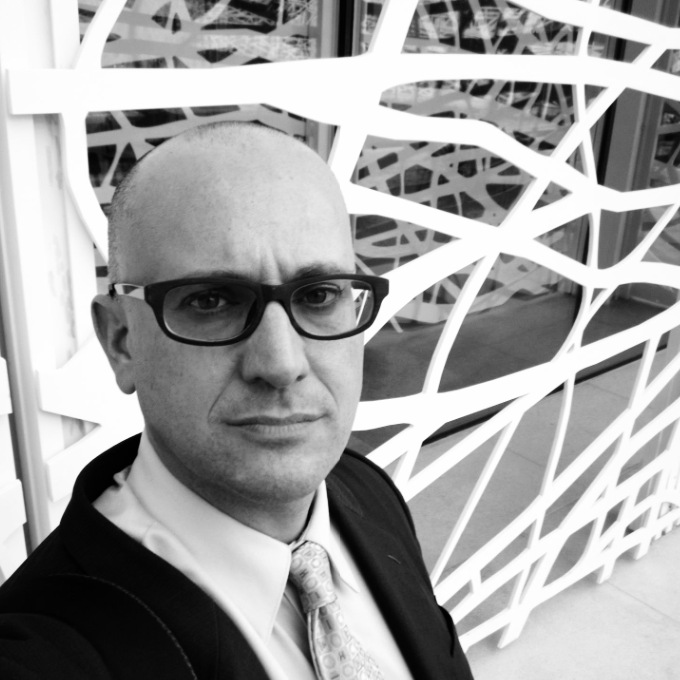
Leon Kaye has written for 3p since 2010 and become executive editor in 2018. His previous work includes writing for the Guardian as well as other online and print publications. In addition, he's worked in sales executive roles within technology and financial research companies, as well as for a public relations firm, for which he consulted with one of the globe’s leading sustainability initiatives. Currently living in Central California, he’s traveled to 70-plus countries and has lived and worked in South Korea, the United Arab Emirates and Uruguay.
Leon’s an alum of Fresno State, the University of Maryland, Baltimore County and the University of Southern California's Marshall Business School. He enjoys traveling abroad as well as exploring California’s Central Coast and the Sierra Nevadas.