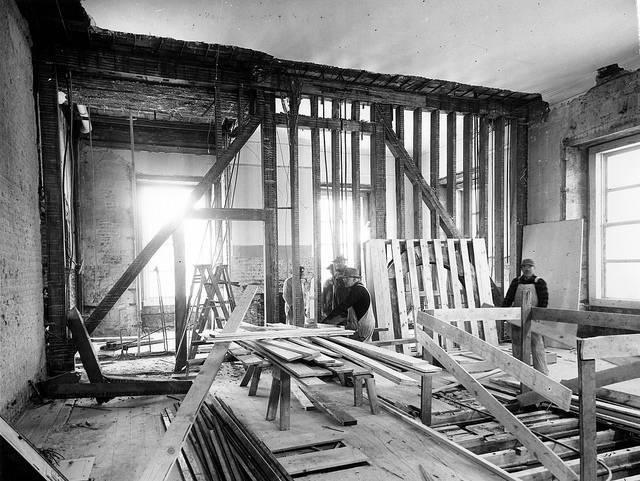
By Charles MacGregor
Prior to the 1970s, it was rare to see a new home built without some sort of asbestos. The once prized mineral, heralded for its durability and resistance to heat, was an easy choice to include in dozens of products. Whether it was the roofing felt and tar paper used on the exterior of a home or the duct and pipe insulation in the basement, chances were good you had some asbestos material in your home. But it didn’t end there. Vehicles often generate high levels of heat while braking, and asbestos eventually found its way into brake linings and pads, too, along with clutch plates and several other parts.
Today, federal laws dictated by the Toxic Substances Control Act (TSCA) ban asbestos from being included in certain types of products, while other newly-manufactured products are only allowed to contain less than 1 percent asbestos. A full ban under the TSCA was put in place in 1989 by the Environmental Protection Agency but was vacated by the Fifth Circuit Court of Appeals in 1991.
The reason for the sudden change of view is due to several types of lung diseases directly connected to the inhalation of asbestos, including asbestosis and mesothelioma, a rare and aggressive cancer with a poor prognosis. Once asbestos was linked to the diseases, companies began replacing asbestos with safer alternatives in the housing and automotive industries.
Although new home and building construction projects no longer contain asbestos, older homes, buildings, schools and hospitals still might. To help employers and employees mitigate risks pertaining to asbestos, the EPA issued an Operations and Maintenance program for all workers coming into contact with asbestos. Employers are expected to either provide training on their own with an Asbestos Program Manager who has sufficient training or hire an outside consultant to come and conduct proper training. By ensuring employees are properly educated, the chances of asbestos entering the air and possibly being inhaled are drastically reduced.
The Occupational Safety and Health Administration (OSHA) requires employers to ensure workers who could be exposed to asbestos are participating in initial training programs, along with refresher courses held annually. Those working in schools and in areas where they may come into contact with asbestos, per EPA guidelines, are required to attend 16 hours of training, including 14 hours of Special O&M training. Beyond training, OSHA also requires employers to provide workers with regulated areas, proper personal protective equipment (PPE) for abatement and even medical monitoring for employees when legal limits or exposure times are exceeded in the workplace.
The need for periodic health screenings and monitoring are incredibly important for employees working in areas where exposure to asbestos is possible. One of the most frightening facts related to asbestos exposure and the threat of mesothelioma or asbestosis are the diseases’ long latency periods. Symptoms related to mesothelioma can take anywhere from 10 to 40 years to present, and by the time it’s caught the disease is more difficult to treat. Employers are held by OSHA standards to keep track of asbestos exposure and to maintain detailed records regarding employee health, while also covering the costs of tests and monitoring for workers exposed to asbestos above the permissible limits.
Proper employee training isn’t just a safeguard for employers whose employees may come into contact with the toxic material. By providing the right training at the right intervals, the risk of potential problems decreases. In schools, office buildings and other public locations, highly successful training prevents the possible spread of asbestos fibers through the air where it poses a significant risk to people.
From a moral standpoint, providing asbestos education to workers seems like a good fit. But it also makes economic sense. The cost of the training is far outweighed by the possibility of large fines for poor removal methods and lax health considerations. There is absolutely no “safe” level of asbestos exposure, and even short-term exposure to the material has resulted in mesothelioma. For most people, they might not even know they’ve been exposed to asbestos until decades later when mesothelioma symptoms begin to present.
Though the burden of training is on employers to make sure workers are equipped with the right knowledge and equipment to contain and remove asbestos, the worker also needs to effectively use the information they have to make the right decisions.
Asbestos isn’t the wonder material it once was, and the risks of poor abatement run far too high for businesses to not provide the right training, equipment and protections for employees. However, those workers must fully understand what they’re handling and be fully cognizant of the situation every time they enter the work area. With those thoughts in mind, mistakes can be kept at a minimum and any removal or encapsulation process can move along smoothly and safely.
Image credit: Flickr/The U.S. National Archives
Charles MacGregor is a health advocate specializing in mesothelioma, a rare and aggressive disease affecting 3,000 people annually in the U.S. He works to spread awareness about the disease and advocating for the ban of asbestos in the United States.
TriplePundit has published articles from over 1000 contributors. If you'd like to be a guest author, please get in touch!