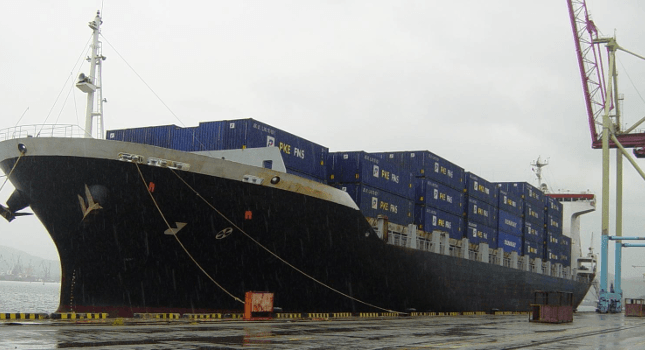
By Srini Vasan
Remember that old idea about how a butterfly flapping its wings in South America unleashes a crazy string of events that results in disaster elsewhere? Anybody who manages a supply chain understands the delicate interplay of events, and how one mishap can instantly derail your whole system. And how expensive the consequences can be.
Inbound Logistics found that 73 percent of companies they surveyed had experienced a disrupted supply chain. Almost a third of those companies took more than a month to recover.
Military coups, terrorist attacks and devastating events from Mother Nature happen. But making a contingency plan now will minimize the damage to your company and those it serves when the inevitable happens. Here are some steps you can take.
1. Map out your supply chain
To best anticipate possible problems, you need to understand your whole supply chain. If your business involves assembly parts shipped from China, for example, try to find out where the raw materials come from. How many different types of raw materials are used, and how do they get to the manufacturer? By what route does the manufacturer ship the parts to you?
2. Stay aware
Once you know what places and shipping routes are involved, stay up on the news. Sniff out possible events that could affect your company. Some things happen fast, such as a cave-in at a quarry. But other things develop more slowly, such as escalating conflict before a volatile election. Encourage any staff members who work directly with your overseas suppliers to ask for updates on developing storms or political situations. If you see trouble brewing, it’s time to fill in the details of Plans B and C.
3. Stock up on essentials
You can’t supply all of the people all of the time. But if you stockpile the essentials, you’ll keep customers happier and safer, depending on your business. For example, an American hospital will always want to maintain a large stock of antibiotics, but can probably risk running out of cobra antivenin.
4. Assess your risks
Study your supply chain. While all kinds of crazy things could potentially go wrong, some are likelier than others. California has earthquakes. Oregon has rain. If you live in Louisiana, hurricanes are a fact of life and will probably render roads impassable and knock out power. So maybe your company needs a generator.
Make a list of actions to take, depending on the emergency. And assign a responsible party to each.
5. Include your suppliers
Your suppliers need contingency plans, too. Work together to help each other come up with creative responses to big problems. For example, UPS shared their Trackpad technology with an animal rescue organization after Hurricane Katrina. During a future natural disaster, workers will be able to scan bar codes on collars to keep track of displaced animals. Together you can solve problems, while using contingency planning to increase trust and strengthen your business relationship.
6. Plan for alternate transportation
If you’re working with foreign suppliers, a storm overseas can mean a delayed shipment. Perhaps you’ll need to get part of your order by airfreight instead of waiting for that slow boat from China. Depending on the urgency, it might be worth going with the more expensive air shipping. Or finding backup suppliers in other parts of the world that you can call upon when necessary.
Contingency plans are also important for domestic shipments. What if a major derailment slows your rail shipment? Can you contract with a trucking company?
7. Audit your suppliers
How solid are your suppliers? If your foreign suppliers use the Supply Council Operations Reference model to manage their supply chain, that’s a good sign. Assess your suppliers’ risk for natural disasters, labor uprisings and geopolitical issues.
8. Clean house
Disruptive events are a good time to clean house. Are you still stocking SKUs that should have ridden off into the sunset? Might as well retire them now.
Then, back to contingency planning for the next disaster.
Image credit: Pantos Logistics - Sea Freight
Srini Vasan is the CEO of eShipGlobal, an on demand transportation management solution provider, which prides itself on bringing business applications to the market quickly and helping customers manage their transportation effectively. As CEO, Vasan is involved in business development and oversees technology infrastructure and software development.
TriplePundit has published articles from over 1000 contributors. If you'd like to be a guest author, please get in touch!