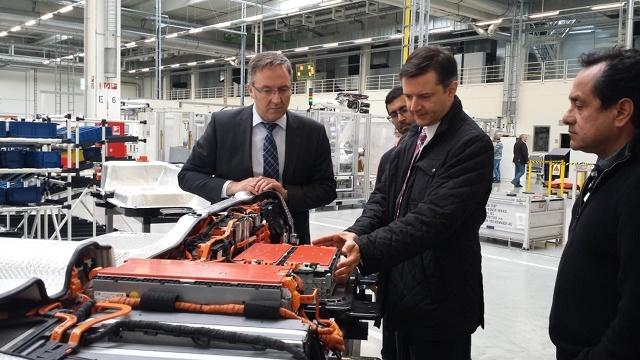
Last month, I was lucky enough to be one of the first Americans to hop behind the wheel of the 2015 e-Golf, Volkswagen’s first fully-electric vehicle for the North American market. The car offers a smooth ride and a good deal of pep, with a best-in-class torque of 199 foot-pounds (the standard torque measure).
Its 24.2 kilowatt-hour lithium-ion battery is no slouch either, providing 70 to 90 miles of range on a single charge. Like the e-Golf's electric motor and transmission, the battery was developed in-house and is made at Volkswagen’s manufacturing facility in Braunschweig, Germany.
The Braunschweig plant, the oldest in operation for Volkswagen Group, has been manufacturing conventional batteries for more than 75 years. Eighteen months ago, it began producing batteries for the automaker's first electric vehicle, the E-Up! (available in European markets only). Earlier this year, Braunschweig added batteries for the European and North American e-Golf models to its portfolio, and it's now the only plant to churn out batteries for Volkwagen's two electric vehicles.
Before the batteries ever hit the manufacturing floor, a team of 170 engineers at Braunschweig spent months developing their design. In the development phase, the biggest challenge for VW engineers was how to get the most energy out of the battery with the smallest size, while still meeting safety standards, said Dr. Holger Manz, head of the battery development department in Braunschweig.
Sounds pretty familiar, but the result here at Volkswagen is nothing less than a testament to the ingenuity of German engineering. For the e-Golf, the automaker decided on the same Modular Transverse Matrix (MQB) architecture it uses for the regular Golf, its most popular model in Europe, enabling engineers to place the large battery within the chassis architecture. In the 2015 e-Golf, the battery rests in the center tunnel just ahead of the rear axle and below the rear seats, eliminating cabin intrusion or a reduction in interior space.
In a move that seemed curious to some, Volkswagen also eliminated the use of active liquid cooling systems in favor of a simpler air cooling design. As Manz put it, the Panasonic battery cells VW chose are so efficient, an active cooling system "wasn't necessary."
"Our battery system here at Braunschweig is very well developed, so the customer can be sure he's driving a very safe car," Manz told a group of journalists at the battery plant last week.
Each battery is comprised of up to 2,500 individual parts, and Braunschweig produces one electric vehicle battery every 20 minutes. While in Germany last week, I had a chance to tour the battery plant in Braunschweig, along with nine other American journalists, and catch an up-close look at how e-Golf batteries are made. Click the first photo to open the gallery and catch a glimpse for yourself.
[gallery link="attachment page" ids="196544,196545,196546,196547,196548,196549,196550,196551,196552,196553,196554,196555"]
All images by Mary Mazzoni
Editor's Note: Travel expenses for the author and Triple Pundit were provided by Volkswagen.
Based in Philadelphia, Mary Mazzoni is a senior editor at TriplePundit. She is also a freelance journalist who frequently writes about sustainability, corporate social responsibility and clean tech. Her work has appeared in the Philadelphia Daily News, the Huffington Post, Sustainable Brands, Earth911 and the Daily Meal. You can follow her on Twitter @mary_mazzoni.
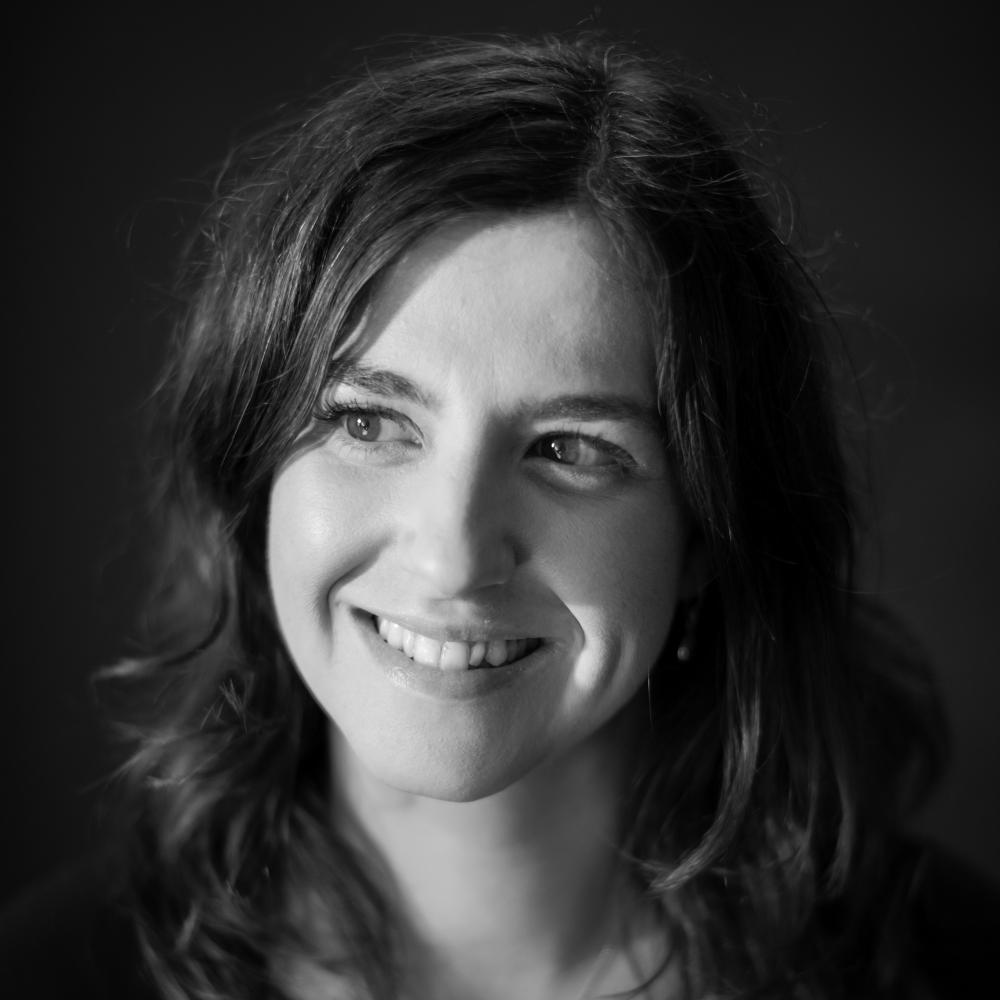
Mary has reported on sustainability and social impact for over a decade and now serves as executive editor of TriplePundit. She is also the general manager of TriplePundit's Brand Studio, which has worked with dozens of organizations on sustainability storytelling, and VP of content for TriplePundit's parent company 3BL.