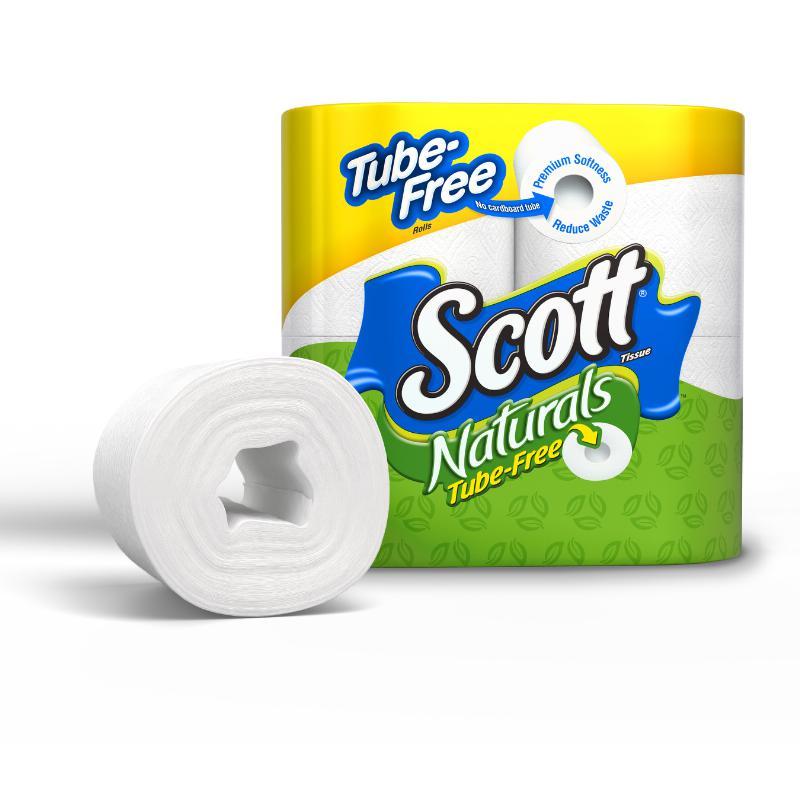
Kimberly-Clark produces mainly paper-based personal care products, including popular brands such as Cottonelle, so it’s only fitting that the global company focuses on sustainable forestry.
Its latest corporate social responsibility report lists short- and long-term goals to make its products more sustainably produced. One of the short-term goals is to source 100 percent of its wood fiber from suppliers who have achieved third-party certification by 2015. It has already achieved this goal. Two of K-C’s long term-goals also involve sustainable forestry, including obtaining 90 percent of the fiber in its tissue products from environmentally-preferred sources by 2025. At the end of 2013, K-C was at 71.1 percent. Second, the company planned to transition to at least 50 percent of wood fiber sourced from natural forests to alternative fiber sources by 2025. At the end of 2013, K-C achieved 24 percent reduction of fiber sourced from natural forest.
K-C states it will not knowingly use conflict wood, illegal fiber or fiber procured from special forest areas, including endangered forests. All K-C tissue mills in North America and about 50 percent of mills in other regions are chain-of-custody certified. The goal is to achieve 100 percent chain-of-custody certification for all of its mills by 2016.
Reducing water use
K-C uses vast amounts of water in its manufacturing process, so focusing on water use reduction is also important. Its water reduction goal is to reduce water use by 25 percent by 2015, a goal it met the goal in 2013 by achieving a 26.4 percent reduction. K-C met the goal through a more efficient manufacturing footprint, water conservation programs, and upgrading water and waste systems. In addition, mill staff optimized water use reduction programs and effluent recycling systems that were installed in 2012. K-C also completed six major water reduction projects in 2013.
Striving to keep waste out of landfills
Some goals are harder than others to achieve. The goal for 2013 was to have 85 percent of its manufacturing waste diverted from landfills, but the company only achieved an 81.6 percent diversion rate. However, it is an increase from 78 percent in 2012, and 58 percent of the company’s facilities met the 2015 goal of sending zero manufacturing waste to landfills. K-C is on track to be near 90 percent landfill-free by the end of 2014.
One of the ways the company is reducing its waste is to stop making it. For example, K-C is on track to eliminate the production of over 210 million diapers that don’t mean its quality standards. Its manufacturing team is developing similar plans for other child care products in 2014.
Reducing greenhouse gas emissions through energy conservation
In 2013, K-C achieved greenhouse gas (GHG) emissions reductions of 3 percent from 2012 levels, and a 6.4 percent reduction from the baseline year of 2010 -- meeting its 2015 goal two years early. The majority of K-C’s operational GHG emissions come from energy use at its manufacturing facilities, so the company focuses on energy conservation and increasing renewable energy use.
Renewable energy use ranges from biofuels sourced from wood waste or landfill gas in the U.S., Switzerland, Brazil and Thailand to solar power installations in the U.S. and Italy. K-C has deployed cogeneration at four manufacturing plants since 2005. The latest cogeneration system is in a mill in Millicent, Australia and produces over 90 percent of the facility’s electricity needs. All of the mill’s steam is produced through a waste heat recovery steam generator, and additional waste heat is incorporated into the tissue manufacturing process to reduce over 60 percent of the natural gas used to dry its tissue.
Image credit: Wikipedia
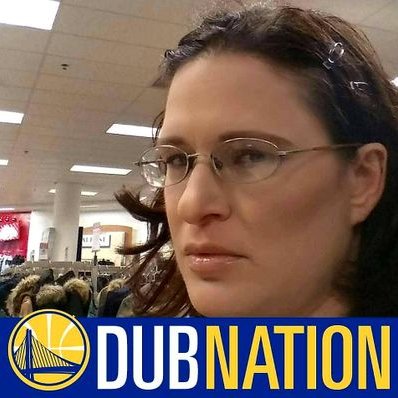
Gina-Marie is a freelance writer and journalist armed with a degree in journalism, and a passion for social justice, including the environment and sustainability. She writes for various websites, and has made the 75+ Environmentalists to Follow list by Mashable.com.