“Most supplier responsibility programs are compliance-focused, with most of their resources consumed by conducting audits, correcting deficiencies, and following up,” Tim Mohin writes in his book “Changing Business from the Inside Out.”
How well has this approach worked so far? After the suicides in Foxconn, the building collapse in Bangladesh and other supply chain tragedies we have witnessed over the years, you already know the answer.
One approach to fixing these programs can be found in the factory safety accord in Bangladesh, which puts more emphasis on better inspection mechanisms, ensuring that factories will make the necessary upgrades to provide safe working conditions and protect workers’ rights.
But what if, instead of trying to improve these periodic audits and inspections, companies focused their efforts on establishing direct communication lines with the workers to learn about problems - and the effectiveness of solutions - in real time?
The idea is that that better communication can lead to improved worker conditions. It’s easier said than done, which is why I was glad to learn about one interesting solution offered by Good World Solutions.
At the Social Innovation Summit last month in New York Heather Franzese, the Director of Good World Solutions presented Labor Link, an initiative her organization started in 2010. Labor Link uses mobile technology to enable companies to directly engage and survey workers in their supply chain. Right now, Labor Link is used by more than 10 companies and organizations, including Marks & Spencer, Eileen Fisher and Patagonia. The company currently reaches over 20,000 farmers and workers across 6 countries in 2012.
Following the summit I got in touch with Heather to learn more about Labor Link and its potential to change companies’ approach to supplier responsibility programs.
Triple Pundit: How do you build transparency across global supply chains? Heather Franzese: Today, the world is approaching a 1:1 ratio between mobile subscriptions and people on the planet. In the developing world, mobile penetration is at 89 percent and growing. Labor Link leverages the transformative power of mobile to give workers a voice and, at the same time, give companies real-time data about true conditions in their supply chain. In the future, I see plugging consumers in to this data so they can connect directly with the workers that make their clothes and electronics. Radical transparency is a real-time connection with the people that make our favorite products.
3p: What value do services like Labor Link provide to companies? HF: Labor Link delivers data that is reliable and actionable. It’s very different from hotlines, which workers are often afraid to call. When they do, they rarely report specific information about workplace conditions. Our structured multiple-choice surveys are anonymous and free to workers and focus on specific topics to ensure the data is actionable by brands. Do workers feel comfortable speaking to supervisors? Do they feel pressure not to join a union? Have they received training on health and safety? These are the types of questions we ask.
Marks & Spencer is using Labor Link to track the effectiveness of worker training as part of their ambitious Plan A commitments to train 500,000 workers by 2015. Their “Bank the Unbanked” Financial Literacy training increases understanding of basic financial concepts so low-skilled factory workers can take control of their finances and save for the future. Our Labor Link surveys measured baseline conditions and tracked a 33 percent increase in the number of workers with bank accounts after training.
3p: What is the response you receive from workers in developing countries? Do they believe in the potential of these services to improve their working conditions? HF: We’ve been surprised at the overwhelming response from workers, averaging 45 percent participation on most mobile surveys. I was conducting post-survey evaluation on a campaign in the city of Tirupur, a garment manufacturing center in Southern India, and I asked a woman what she thought about the service. “This channel is so important,” she said, “because it gives me a voice to report my opinions and needs to people with the power to make change.” We also deliver survey findings back to workers via SMS and voice recordings (for low literacy workers) so they can advocate for change at the local level.
http://youtu.be/nzq4BhH7kxA
3p: Have you seen more interest in your services after the latest tragedy in Bangladesh? HF: Our phone has been ringing off the hook from people asking how we can prevent disasters like the one at Rana Plaza. Over 1,000 people died. If those workers had a channel like Labor Link to report unsafe conditions in the factory – they saw cracks in the walls several days before the collapse – those deaths could have been prevented. And, of course, if you ask the brands that have been in the headlines for the last month if they wish they had more visibility into their factories and could turn back the clock and stop production at that factory, of course they would say yes.
3p: Given that the solution offered in Bangladesh involves third-party monitoring, do you believe companies can manage their supply chains responsibly independently, or do they need some sort of third-party involvement even when using your services? HF: Technology increases visibility of problems. It’s the starting point, not the endpoint. When you go to the doctor, it doesn’t stop with diagnosis. Likewise, companies need supply chain data to drive strategic decisions that benefit workers. Because factories are shared by multiple brands, the solutions need to be shared and collaborative. We have several factories where brands are coming together to survey workers, share data, and develop collaborative solutions. Worker voice is essential to drive real improvement.
[Image credit: Good World Solutions]
Raz Godelnik is the co-founder of Eco-Libris and an adjunct faculty at the University of Delaware’s Business School, CUNY SPS and the Parsons The New School for Design, teaching courses in green business, sustainable design and new product development. You can follow Raz on Twitter.
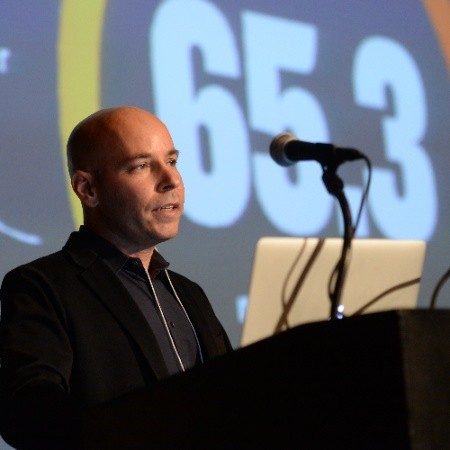
Raz Godelnik is an Assistant Professor and the Co-Director of the MS in Strategic Design & Management program at Parsons School of Design in New York. Currently, his research projects focus on the impact of the sharing economy on traditional business, the sharing economy and cities’ resilience, the future of design thinking, and the integration of sustainability into Millennials’ lifestyles. Raz is the co-founder of two green startups – Hemper Jeans and Eco-Libris and holds an MBA from Tel Aviv University.